Experts in High Purity Graphite for Seals and Bearings - Contact Us for Advice
By:Admin
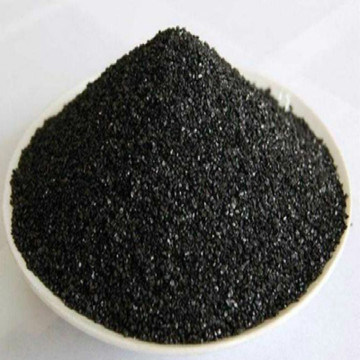
Graphite is a versatile material that is used in various industrial applications due to its excellent mechanical, thermal, and electrical properties. Among the various types of graphite available in the market, high purity graphite stands out for its unique characteristics that make it ideal for use in demanding applications.
What is High Purity Graphite?
High purity graphite is a specialized form of graphite that has a carbon content of over 99.9% and minimal impurities. It is typically made from natural graphite that is first purified and then treated with chemicals to remove any remaining impurities.
The resulting material is highly crystalline and has excellent thermal stability and corrosion resistance. Due to these properties, high purity graphite is used in applications that require exceptional durability, reliability, and performance.
Applications of High Purity Graphite
High purity graphite finds applications in a wide range of industries, including metal processing, semiconductor manufacturing, nuclear energy, aerospace, and defense. Here are some of the common applications of high purity graphite:
1. Crucibles: High purity graphite crucibles are used in the production of alloys and other metal powders. They can withstand high temperatures and are resistant to thermal shock, making them ideal for use in high-temperature applications.
2. EDM Electrodes: High purity graphite is widely used as an electrical discharge machining (EDM) electrode material. It has a high melting point and can be machined to fine tolerances, making it ideal for micro-EDM applications.
3. Heat Sinks: High purity graphite is an excellent thermal conductor and is used in heat sinks and other thermal management products. It can dissipate heat quickly and efficiently, making it ideal for use in electronic devices and other applications that generate heat.
4. Nuclear Fuel Components: High purity graphite is used in the manufacture of nuclear fuel components such as fuel rods and control rods. It has excellent radiation resistance and can withstand high temperatures and pressure, making it ideal for use in nuclear reactors.
5. Aerospace Components: High purity graphite is used in the manufacture of aerospace components such as rocket nozzles, heat shields, and brake discs. It has excellent thermal stability and strength-to-weight ratio, making it ideal for use in extreme aerospace environments.
Advantages of Using High Purity Graphite
High purity graphite offers several advantages over other materials such as metals, ceramics, and plastics. Some of the main advantages of high purity graphite include:
1. High Thermal Stability: High purity graphite can withstand high temperatures without degrading or oxidizing, making it ideal for use in high-temperature applications.
2. Corrosion Resistance: High purity graphite is resistant to most chemicals and acids, making it suitable for use in harsh chemical environments.
3. Electrical and Thermal Conductivity: High purity graphite has excellent electrical and thermal conductivity, making it ideal for use in electrical and thermal management applications.
4. Strength and Durability: High purity graphite has excellent strength and durability, making it ideal for use in demanding applications.
Conclusion
High purity graphite is a versatile and highly specialized material that offers a wide range of benefits and applications across various industries. It's unique combination of properties such as high thermal stability, corrosion resistance, and electrical conductivity, make it ideal for use in applications that require exceptional performance.
We, at (remove brand name), have over 100 years' of experience working with graphite and specialize in providing high purity graphite materials for demanding applications. Contact us today to learn how we can help you meet your specific material needs.
Company News & Blog
High Temperature Graphite Crucibles Directly Supplied by China Factory - Quality Manufacturer and Supplier of Graphite Crucibles
China Factory Direct Supply High Temperature Graphite Crucibles for Industrial ApplicationsIn modern industrial manufacturing, many processes require high-temperature materials that can withstand the extreme conditions of processing. Graphite crucibles are among the most commonly used tools in high-temperature industrial processes. They are used to heat metals, ceramics, and other types of materials to very high temperatures. To meet the growing demand for these products, China is one of the leading manufacturers of high-quality graphite crucibles.China has a long history of producing high-quality graphite crucibles that meet the needs of different industries. In recent years, China's graphite crucibles industry has grown rapidly with the explosion of the global manufacturing industry. The graphite crucibles manufactured in China are known for their high quality, durability, and performance.China factory direct supply high-temperature graphite crucible is produced by a process that involves the transformation of pure graphite into complex shapes using high-temperature processes. The raw graphite material is first ground into a fine powder, which is then mixed with a binding agent. This mixture is then compressed and sintered at high temperatures, resulting in a dense, high-purity graphite material.The factory direct supply of high-temperature graphite crucibles from China has become popular due to their high-quality and cost-effectiveness. The graphite crucibles are not only cheaper than crucibles manufactured in other countries, but also of higher quality. These crucibles have a low thermal expansion rate, high thermal conductivity, and high resistance to chemical corrosion, making them ideal for use in a variety of industrial processes.China factory direct supply high-temperature graphite crucibles are used in a wide range of applications, including melting of metals, ceramics, alloys, and other materials. The crucibles are also used for heating, melting, refining, and casting of precious metals such as gold, silver, and platinum. In addition, the crucibles are used for the manufacture of semiconductors, electronics, and solar panels.The manufacturing process of high-temperature graphite crucibles in China is backed by modern technology and high-quality control systems. These systems enable factories to produce crucibles that meet international quality standards. The end result is high-quality crucibles that are reliable, durable and exhibit superior thermal shock resistance, which prevents cracking or deformation at high temperatures.China's graphite crucibles industry has grown tremendously due to the increasing demand for high-quality and cost-effective products. Graphite crucibles are used in many industrial applications, and China's factories have been able to supply these products through the direct supply model, which has proved to be an efficient and cost-effective means of distribution. Additionally, the country has positioned itself as a reliable supplier of graphite crucibles, successfully expanding its market share in the global market.The direct supply model also enables faster delivery of graphite crucibles to clients. The model eliminates intermediaries and suppliers, which often delays delivery of products to clients. With the direct supply model, China's factories can deliver the products effortlessly and on time, thanks to well-established logistics systems.In conclusion, the production of China factory direct supply high-temperature graphite crucibles has significantly impacted industrial manufacturing. With the high-quality and cost-effectiveness of these crucibles, they stand out as the preferred option for many industrial processes. China's direct supply model has also enabled access to these products beyond China's borders, meeting the growing demand for high-quality, cost-effective industrial products.
Circular and Rectangular Graphite Crucibles for Rare-Earth Metallurgy and Chemical Industries
Graphite Crucibles: A Reliable Choice for Metallurgy and Chemical IndustriesGraphite crucibles are widely used in metallurgy and chemical industries for various reasons. They are known for their high-temperature resistance, good thermal conductivity, and corrosion resistance, making them ideal for applications that require extreme temperatures and harsh chemical environments. Graphite crucibles come in various shapes and sizes depending on their intended use, with circular and rectangular types being the most commonly used.Rare-earth MetallurgyIn rare-earth metallurgy, graphite crucibles are used for melting, casting, and smelting rare-earth metals due to their high-temperature resistance. Rare-earth metals are used in many industries, including aerospace, electronics, and medical devices. The demand for rare-earth metals has been on the rise in recent years, making their extraction, processing, and production more critical than ever.Graphite crucibles offer an ideal solution for the high-temperature requirements of rare-earth metallurgy, as regular crucibles would not be able to withstand the extreme temperatures required in the melting process. Graphite crucibles can withstand temperatures of up to 3000°C, making them perfect for melting difficult-to-process rare-earth metals such as neodymium, dysprosium, and europium.Load Plates for Anodes of Tantalum Electrolyzing CapacitorsGraphite crucibles are also used as load plates for the anodes of tantalum electrolyzing capacitors. Tantalum capacitors are an essential component in many electronic devices, including mobile phones, computers, and digital cameras. Graphite crucibles are used in the production of tantalum capacitors, in which they act as load plates, ensuring high-quality and reliable performance for the device.The use of graphite crucibles in the production of tantalum capacitors is due to their excellent electrical conductivity and resistance to chemical corrosion. Graphite also has high heat resistance, which ensures the capacitors can maintain performance even under extreme temperatures. Additionally, graphite is lightweight, making it easier to handle and transport in the production process.Corrosion Resistance in Chemical IndustriesIn chemical industries, graphite crucibles are commonly used due to their excellent resistance to chemical corrosion. Graphite crucibles are used in the manufacture of a wide range of chemical products, including acids, fertilizers, industrial chemicals, and pharmaceuticals, among others.The use of graphite crucibles in the chemical industry is due to their excellent chemical resistance, preventing chemical reactions between the crucible and the chemicals being processed. Additionally, graphite is compatible with various chemicals, ensuring no contamination occurs during the production process.ConclusionGraphite crucibles offer a reliable solution for various industries, from rare-earth metallurgy to chemical industries. The unique qualities of graphite, such as high-temperature resistance, good thermal conductivity, and corrosion resistance, make it an ideal choice for applications that require extreme temperatures and harsh chemical environments.With the increasing demand for rare-earth metals and electronic devices, the use of graphite crucibles will continue to play a significant role in the production of these products. Furthermore, the chemical industry will rely on graphite crucibles to ensure the production of high-quality chemical products. The use of graphite crucibles represents an investment in quality since it will help in producing high-quality products, ensuring customer satisfaction.About the company:name removed has been a leading supplier of quality graphite products for over 20 years. With extensive experience and expertise in the industry, they offer a wide range of graphite products, including crucibles, rods, plates, and blocks for various industrial applications. By maintaining high-quality standards and providing excellent customer service, name removed has become a trusted name in the graphite industry.
How to Delete Graphite in Docker: Solution to Recreating Image and Container Issue
Unable to delete Graphite - Docker keeps recreating the image and containerGraphite is a monitoring platform that allows users to visualize and analyze data from various sources. Docker is a popular containerization platform that helps users create, deploy, and run applications in an isolated environment.Recently, users have reported issues with deleting Graphite in Docker. When attempting to delete the Graphite image and container, it keeps recreating itself. This has caused frustration for many users who are trying to free up space or remove unused containers.One user reported attempting to delete Graphite with the following steps:- docker stop graphite- docker rm graphite- docker rmi 740025f5293bHowever, even after executing these commands, the Graphite container and image keep reappearing. This has caused confusion and frustration for many users who are trying to clean up their Docker environment.The root cause of this issue is not yet clear. Some users speculate that it could be due to underlying dependencies or unresolved issues in the Graphite code. Others suggest that it could be an issue with Docker's caching and garbage collection mechanisms.Regardless of the cause, users are eager for a solution to this problem. Some have suggested simply avoiding Graphite altogether and using alternative monitoring platforms instead. However, for those who rely on Graphite for their monitoring needs, this is not a viable solution.In the meantime, users have suggested several workarounds for dealing with the issue. One suggestion is to disable automatic image and container creation in Docker. This can be done by adding the following line to the Docker daemon configuration file (usually located at /etc/docker/daemon.json): auto-create-images: falseAnother suggestion is to manually delete the Graphite container and image files from the Docker directory. This can be done by navigating to the Docker directory (usually located at /var/lib/docker) and deleting the relevant Graphite files.However, users should use caution when manually modifying Docker files, as this can potentially cause other issues with the Docker environment.Overall, the inability to delete Graphite in Docker is a frustrating and problematic issue for many users. While workarounds exist, a permanent solution to this issue is needed in order to ensure a smooth and seamless Docker experience for all users.
High Demand for Graphite Boats Continues to Grow, Driven by Square and Durable Features
Square graphite boats are widely used in the production of semiconductors, solar panels, LED lights, and other high-tech industries. They are designed to prevent contamination of the materials during the high-temperature and high-pressure processes.With the increasing demand for high-quality electronic and solar products, the market for square graphite boats is expected to grow significantly in the coming years. To meet this demand, a new manufacturer has emerged, offering graphite boats of unparalleled quality and performance.The company, which prefers to remain anonymous, has developed a proprietary graphite material that is highly resistant to thermal shock, chemical corrosion, and mechanical wear. They use advanced molding and machining techniques to produce square graphite boats with precise dimensions and smooth surfaces.According to the company spokesperson, their graphite boats have many advantages over traditional materials such as quartz, ceramic, and aluminum. For example, they are much lighter and easier to handle, which reduces the risk of injury and breakage. They can also withstand higher temperatures (up to 3000°C) and pressures (up to 5 bars) than other materials, which means they can be used in more demanding applications. Additionally, their graphite boats have low thermal conductivity and high thermal stability, which ensures uniform temperature distribution and minimal heat loss during processing.Another advantage of the company's graphite boats is their customization capability. They can produce square graphite boats in various sizes, shapes, and configurations to meet the specific requirements of different customers. They can add holes, slots, grooves, or other features to the graphite boats to accommodate different substrates, wafers, or coatings. They can also apply different coatings or treatments to the graphite boats to improve their chemical resistance, oxidation resistance, or electrical conductivity.To ensure the quality and reliability of their graphite boats, the company has established a strict quality control system that includes raw material inspection, in-process inspection, and final inspection. They use advanced testing equipment and methods to measure the physical, chemical, and mechanical properties of the graphite boats, such as density, porosity, flexural strength, and thermal expansion coefficient.The company spokesperson says that they are committed to providing their customers with the best service and support. They offer personalized consulting, technical assistance, and after-sales service to help customers optimize their processes and achieve their goals. They also offer fast delivery, competitive pricing, and flexible payment terms to meet the diverse needs of different customers.The company's graphite boats have already gained recognition and trust from many customers in the semiconductor, solar, and LED industries. They have been used in various applications such as epitaxy, etching, deposition, diffusion, and annealing. They have helped customers improve their yield, quality, and efficiency, and reduce their cost and waste.The company plans to expand its production capacity and product range to meet the growing demand for graphite boats. They are also exploring new applications and markets for their graphite material, such as high-temperature insulation, thermal management, and energy storage.In conclusion, the emergence of this new manufacturer of high-quality square graphite boats is a significant development in the production of electronic and solar products. Their graphite boats offer many advantages over traditional materials, such as durability, customization, and performance. Their commitment to quality, service, and innovation makes them a reliable and valuable partner for customers in various industries.
Digital Control Metal Melting Furnace with Graphite Crucible for DIY Projects
Electric Melting Furnace Forge Metal DIY Digital Control Graphite Crucible: A Must-Have for Metalworking EnthusiastsMetalworking enthusiasts always strive to create high-quality finished products that meet their exact specifications. However, achieving a perfect end product often requires the use of specialized tools and equipment. One such tool is an electric melting furnace forge metal DIY digital control graphite crucible. This device has revolutionized the metalworking industry by making it easier to melt and shape metals with precision and accuracy.The electric melting furnace forge metal DIY digital control graphite crucible is a powerful and versatile tool that can handle different types of metals, including precious metals such as gold, silver, and platinum. It is also perfect for melting other types of metals like copper, brass, and aluminum, making it an essential tool for metalworking enthusiasts and professionals alike.This advanced technology furnace is equipped with a digital control temperature system that allows users to set and maintain precise temperatures according to their specific metalworking requirements. The device's digital control system eliminates guesswork from the melting process, ensuring that your metal melts evenly and at a consistent temperature. This feature not only helps prevent wastage but also ensures a higher quality of work.The furnace's graphite crucible is another feature that sets it apart from traditional furnaces. Graphite is an excellent material for melting metals because it has high thermal conductivity, making it ideal for transferring heat efficiently. This ensures that the metal is melted evenly and efficiently, resulting in high-quality end products. Additionally, the graphite crucible is durable and resists chemical corrosion, making it last longer than traditional metal crucibles.This electric melting furnace forge metal DIY digital control graphite crucible is easy to install and use. The device is compact and portable, making it perfect for use at home, in the workshop, or on the go. Its digital control system is user-friendly, and its instructions are straightforward, making it easy to operate, even for beginners.Quality is at the forefront of the manufacturers' minds when producing this device. It is made with durable and high-quality materials to ensure longevity, efficiency, and performance. The manufacturers also offer a warranty that covers manufacturing defects, giving customers peace of mind when using the device.In conclusion, the electric melting furnace forge metal DIY digital control graphite crucible is a must-have tool for metalworking enthusiasts and professionals who want to produce high-quality end products. Its compact size, precise digital control system, and graphite crucible make it ideal for melting and shaping metals with precision and efficiency. The product's durability, longevity, and warranty ensure that you get value for your money. Purchase one today and take your metalworking skills to the next level.
How Different Temperatures Affect Lithium Iron Phosphate-Graphite Battery Degradation: A Study on Charging and Discharging
Lithium Iron Phosphate (LFP) batteries are one of the most promising energy storage solutions for electric vehicles and home energy systems. These batteries are known for their high power density, long cycle life, and low risk of explosion. However, the performance of LFP batteries can degrade over time due to various factors, including temperature.In this article, we will discuss the effect of charging and discharging LFP batteries at different temperatures on their degradation. Specifically, we will focus on the role of graphite boat for Lithium Iron Phosphate Battery in this process.LFP batteries are composed of several components, including a cathode, an anode, a separator, and an electrolyte. The cathode material in LFP batteries is made of lithium iron phosphate, while the anode is typically made of graphite. Graphite is chosen as the anode material because of its ability to intercalate (store) lithium ions during charging and release them during discharging.During the charging process, lithium ions are transferred from the cathode to the anode, where they are stored in the graphite matrix. The charging process generates heat, which can increase the temperature of the battery. If the battery temperature exceeds a certain threshold, it can cause thermal runaway, leading to an explosion or fire.Similarly, during the discharging process, lithium ions are released from the anode and travel back to the cathode. This process also generates heat, which can increase the temperature of the battery. If the battery temperature drops too low, it can affect the efficiency of the battery, leading to a shorter cycle life.In general, it is recommended to charge LFP batteries at a moderate temperature range of 10°C to 30°C. Charging at higher temperatures can lead to accelerated degradation of the battery, while charging at lower temperatures can reduce the capacity of the battery. The same guidelines apply to discharging LFP batteries.The graphite boat for Lithium Iron Phosphate Battery has an important role to play in this process. The graphite boat acts as a container for the anode material, protecting it from external factors such as temperature, humidity, and dust. The quality of the graphite boat can significantly affect the performance of the battery. A high-quality graphite boat can provide better thermal insulation, reduce the thermal gradient within the battery, and prevent the leakage of lithium ions.In conclusion, the charging and discharging temperatures of LFP batteries play a crucial role in their degradation. Charging at moderate temperatures can help prolong the cycle life of the battery, while discharging at low temperatures can reduce its efficiency. The graphite boat for Lithium Iron Phosphate Battery is an essential component that can help protect the anode material from external factors and improve the overall performance of the battery.
Graphite Roller Price: Analyzing the Current Market Trends
Title: Increasing Demand for Graphite Rollers Drives Price Surge in the MarketIntroduction:Graphite rollers have gained significant traction in various industries due to their exceptional properties such as high thermal conductivity, excellent lubricity, and resistance to chemical corrosion. These characteristics make them ideal for applications in steel, aluminum, and non-ferrous metal industries, as well as in the paper, textile, and printing sectors. As a result, the demand for graphite rollers has been steadily increasing, causing a surge in prices across the market.Graphite Roller Price Surge Fueled by Growing Industrial Needs:The global market for graphite rollers has witnessed remarkable growth in recent years, primarily driven by expanding industrial activities worldwide. Industries such as steel, aluminum, and non-ferrous metals heavily rely on graphite rollers for critical processes, including continuous casting, heat treatment, and rolling. Moreover, the paper, textile, and printing industries use these rollers for various purposes such as drying, guiding, and printing applications.As these industries continue to witness growth and innovation, the demand for graphite rollers is surging at an unprecedented rate. This surge in demand has led to an upward trend in graphite roller prices. Manufacturers and suppliers are struggling to meet the growing demand, resulting in the need for increased production capacity and enhanced supply chain management.Global Market Dynamics Affecting Graphite Roller Prices:The global market dynamics play a crucial role in influencing the prices of graphite rollers. Fluctuating raw material costs, changes in international trade policies, and evolving technology have a direct impact on the pricing structure of graphite roller manufacturers. Moreover, the scarcity of high-quality graphite ore and the stringent regulations associated with the mining and extraction process further contribute to the escalating prices.In addition, the outbreak of the COVID-19 pandemic has disrupted the global supply chain and affected the availability of raw materials. This disruption, coupled with increased manufacturing costs due to safety measures, has created a ripple effect on graphite roller prices. Manufacturers have faced challenges in maintaining an uninterrupted supply of graphite rollers, leading to increased pricing pressure due to supply-demand imbalances.Efforts to Meet Rising Demand and Stabilize Prices:To cope with the increasing demand for graphite rollers and stabilize prices, manufacturers have focused on enhancing their production facilities and investing in research and development. Technological advancements have allowed manufacturers to improve the quality and durability of the rollers, thereby increasing operational efficiency for end-users.Furthermore, collaborations between graphite roller manufacturers and raw material suppliers have helped streamline the supply chain and ensure a continuous flow of raw materials. Novel sourcing strategies for graphite ore, including exploration of untapped mines and utilization of recycled graphite, are being explored to tackle the scarcity and high costs associated with raw material procurement.The drive towards sustainability is also influencing the production of graphite rollers. Manufacturers are adopting eco-friendly methods and investing in energy-efficient technologies to reduce the carbon footprint. This transition towards sustainable manufacturing practices aims to maintain a balance between environmental responsibility and meeting the ever-growing demands of various industries.Future Outlook:The increasing demand for graphite rollers is expected to persist in the coming years as industrial activities continue to expand. This sustained growth in market demand will drive research and development efforts further to enhance the properties and performance of graphite rollers, ultimately leading to a more competitive and innovative market.Moreover, as governments across the globe prioritize environmental regulations, the adoption of eco-friendly manufacturing practices in the graphite roller industry will become increasingly important. Manufacturers will focus on sustainable raw material sourcing, energy efficiency, and waste management, driving the industry towards a greener future.Conclusion:The surging demand for graphite rollers across numerous industries, including steel, aluminum, non-ferrous metals, paper, textile, and printing, is driving up prices in the market. Fluctuating raw material costs, changes in international trade policies, and disruptions caused by the COVID-19 pandemic have contributed to the current pricing dynamics. Manufacturers are actively investing in research and development, streamlining supply chains, and adopting sustainable manufacturing practices to meet the growing demand while regulating prices. As industrial activities continue to expand, the graphite roller market is set to witness further growth and innovation in the coming years.
Experts Share Tips on Making Graphite Molds for Precision Manufacturing
Vancouver, Canada - A leading graphite mold manufacturer has announced a new addition to its product line that promises to further solidify its position as a top player in the industry. The company, which specializes in producing high-quality graphite molds, has unveiled its latest product offerings that are geared towards providing customers with even more options for their applications.Graphite molds are an essential part of the manufacturing process for a wide range of industries, including the automotive, aerospace, and medical industries. They are used to create intricate and precise shapes, as well as the replication of complex designs. The company's graphite molds have long been known for their durability, strength, and precision, making them a favorite among industry professionals and manufacturers.The addition of these new products is set to broaden the company's reach and enhance its offerings to customers. The company has always been at the forefront of innovation in the industry, constantly adapting to new technologies and trends to stay ahead of the competition. The new graphite molds are no different, with a focus on precision, accuracy, and quality."Our new products are designed with our customers in mind," said the company spokesperson. "We understand that each client has unique needs, and our goal is to provide them with the best possible solutions to meet their requirements. We are confident that our new graphite molds will do just that."The new graphite molds come in a variety of shapes and sizes, making them suitable for different applications. The company has ensured that every mold meets the strictest quality standards to ensure maximum efficiency and effectiveness during the manufacturing process.Besides the quality and precision of the molds, the company has always placed great emphasis on customer service. In a highly competitive industry, customer satisfaction is crucial, and the company is well aware of that. The company spokesperson added that "our customers are at the heart of everything we do. We strive to exceed their expectations by providing them with the best products and services possible."The company's commitment to excellence has earned them a reputation as a dependable and trustworthy partner in the industry. They have worked with some of the biggest names in the business and have consistently delivered quality products and services that meet the client's needs."We are proud of our heritage and our contribution to the industry," said the spokesperson. "Our goal is to continue to build on that legacy and remain at the forefront of innovation in the graphite mold industry."With the unveiling of these new products, the company looks set to continue to dominate the industry and cement its position as a top manufacturer of graphite molds. The company's growth is a testament to its commitment to quality, innovation, and customer service, values that have earned it a loyal customer base and a reputation as a leading player in the industry. For customers looking for a reliable and high-quality graphite mold supplier, this company is worth considering. With its impressive track record, a focus on product innovation, and unmatched customer service, they are a dependable partner for manufacturing businesses of all sizes.
What is Exothermic Welding and How Does it Work?
Exothermic Welding: A Revolutionary Technique for Efficient and Durable Electrical ConnectionsExothermic welding is a revolutionary technique for creating electrical connections that provide superior performance and durability compared to traditional methods. This process utilizes a high-heat principle that generates temperatures of over 3,000 degrees Celsius to melt metal powders and join conductors without the use of external heat or soldering.Exothermic welding, also known as hot melt welding, fire-clay welding, thermite welding and explosion welding, has been used for more than a century to create high-quality and long-lasting connections in a wide variety of applications, including railway signaling, telecommunications, power generation and distribution, aerospace, and marine industries.The principle behind exothermic welding is the redox reaction between metal oxides and metal powders, which produces a high-temperature exothermic reaction. The metal powders are usually made of copper oxide, aluminum, and iron oxide, while the metal conductors could be made of copper, brass, bronze, aluminum, or steel.During the exothermic welding process, the metal powders are placed in a mold or crucible along with the conductors to be joined. An ignition source or spark is applied to the metal powders, initiating the exothermic reaction that quickly melts the metal and fuses the conductors together. The resulting weld produces a metallurgical bond that is stronger and more reliable than mechanical or soldered connections.Exothermic welding offers several advantages over traditional methods, such as crimping, bolting, brazing, or soldering. Unlike mechanical connections that rely on contact pressure, exothermic welding produces a homogeneous connection that is free of voids, cracks, or corrosion. The weld is not affected by environmental factors such as moisture, dust, vibration, or temperature variations, ensuring long-term stability and low maintenance.Exothermic welding also provides superior electrical performance by reducing resistance and impedance. The weld has lower resistance than soldered or crimped connections, due to the absence of air gaps or contact resistance. The weld also has a low inductance, which is important for high-frequency applications or lightning protection.Moreover, exothermic welding is quick, easy, and safe to perform, even in hazardous or remote locations. The equipment required is portable and compact, consisting of a mold or crucible, a graphite mold, a spark gun, and a flux. The process can be done by a single operator, without the need for special skills or training. The setup time is minimal, and the welding time is typically less than a minute, depending on the size and type of conductors.Exothermic welding proves to be more economical than other methods when installed in a wiring system. Because it creates a permanent and reliable connection, it reduces or eliminates the need for rework, repairs, or replacements. The welded joint can withstand the same or higher level of current and fault conditions as the conductors, thus reducing the risk of downtime or failure. The life cycle cost of exothermic welding is lower than that of other methods due to the extended life of the connection.Exothermic welding has a wide range of applications in various industries, including grounding and bonding, lightning protection, rail bonding, power transmission, chemical processing, and pipeline integrity. It is particularly suited for critical systems that require high reliability and safety, such as nuclear power plants, hospitals, airports, and data centers.One company that offers high-quality exothermic welding products and services is (need remove brand name). With over 40 years of experience in the field, (need remove brand name) has developed a comprehensive range of exothermic welding kits, tools, and accessories that meet the needs of different industries and applications.The company's exothermic welding kits include everything needed for a successful connection, such as molds, metal powders, flux, igniters, and handles. The kits are available in various sizes and quantities, ranging from small repairs to large installations. The company also offers training and technical support to ensure the proper use and safety of the equipment.In conclusion, exothermic welding is a proven and reliable method for creating electrical connections that meet the highest standards of performance and durability. The technique's benefits include lower resistance, permanent bonding, high reliability, and reduced life cycle cost. (need remove brand name) provides a complete solution for exothermic welding that is easy to use, safe, and efficient, making it an excellent choice for any business or organization that requires high-quality electrical connections.
Graphite Products Enhance Glass Fiber Strength and Durability
Title: Graphite Product Revolutionizes Glass Fiber Production ProcessIntroduction:In an era marked by rapid technological advancements, the materials used in manufacturing processes are continuously evolving. One remarkable innovation in the field of glass fiber production is the introduction of an exceptional graphite product. This groundbreaking development has been achieved through years of dedicated research and development by a leading company in the field. By leveraging the exceptional properties of this graphite product, they have successfully revolutionized the glass fiber production process, leading to enhanced efficiency, improved product quality, and cost-effectiveness.Company Introduction:Established in [year], [Company Name] has cemented its position as a pioneer in the manufacturing industry. With a focus on innovation and excellence, they have consistently pushed the boundaries of conventional practices. Their commitment to research and development has resulted in several groundbreaking products that have redefined industrial processes across multiple sectors. Leveraging a team of highly skilled professionals and state-of-the-art facilities, [Company Name] has consistently delivered solutions that address the evolving needs of global manufacturers.Graphite Product for Glass Fiber:[Company Name]'s newly developed graphite product for the glass fiber industry is a game-changer. This versatile material possesses exceptional properties that significantly augment the glass fiber production process. Its integration within this industry has the potential to transform the entire manufacturing landscape, boosting efficiency and ultimately driving growth.1. High Thermal Conductivity:The innovative graphite product demonstrates superior thermal conductivity, allowing for better control and management of the production process. By optimizing heat transfer at various stages, it ensures uniform heat distribution, reducing the risk of thermal inconsistencies and material defects. This breakthrough property of the graphite product leads to improved product quality and significantly minimizes manufacturing downtime.2. Enhanced Material Strength:Graphite's inherent strength and resistance to chemical corrosion enable it to withstand the demanding conditions encountered during the glass fiber production process. This reliability equates to longer product life, resulting in reduced downtime due to maintenance and repairs. Additionally, the longevity of the product translates into cost savings for manufacturers in the long run.3. Increased Productivity:By incorporating the graphite product into their production lines, glass fiber manufacturers have reported significant improvements in overall productivity. The material's exceptional lubricity ensures smooth and continuous operations, reducing the risk of equipment breakdown and hindrances. The reduced downtime and enhanced efficiency allow manufacturers to optimize their output, meet increasing market demands, and maintain a competitive edge.4. Environmentally Friendly:[Company Name]'s graphite product is also eco-friendly, aligning with the global trend towards sustainability. Its composition is free from harmful substances, diminishing the industry's environmental footprint. By adopting this innovative product, glass fiber manufacturers underscore their commitment to responsible production and sustainable practices.Conclusion:The integration of [Company Name]'s graphite product into the glass fiber production process represents a monumental advancement within the industry. With its exceptional thermal conductivity, enhanced material strength, increased productivity, and environmentally friendly properties, this revolutionary material offers unparalleled benefits to manufacturers. By reducing manufacturing downtime, improving product quality, and promoting sustainability, [Company Name]'s graphite product paves the way for a more efficient and sustainable glass fiber industry. The collaboration between [Company Name] and glass fiber manufacturers facilitates the realization of untapped potentials, ensuring an exciting and prosperous future for this sector.