Top Quality Graphite Moulds from China - The Latest in Moulding Technology
By:Admin
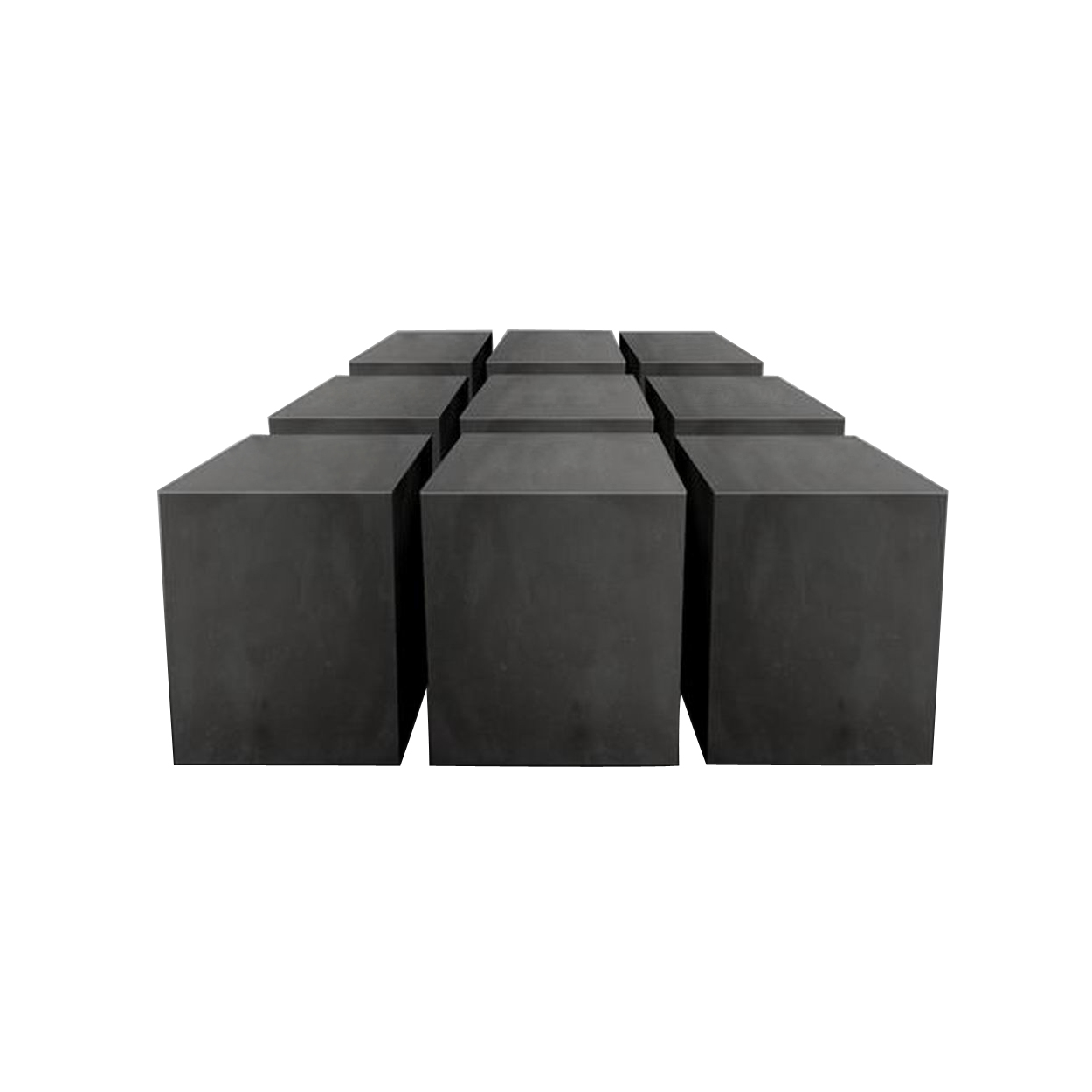
Established in [year], China Graphite Mould has quickly gained a reputation for delivering superior graphite molds that are designed to meet the exacting specifications of their customers. The company's state-of-the-art manufacturing facilities are equipped with advanced technology and equipment, allowing them to produce molds with exceptional precision and accuracy. With a focus on quality control, China Graphite Mould ensures that every product that leaves their facility meets the highest standards of performance and durability.
One of the key factors that sets China Graphite Mould apart from other manufacturers is their commitment to research and development. The company has a dedicated team of engineers and technical experts who are constantly working to improve their products and develop new and innovative solutions for their customers. This focus on innovation has enabled China Graphite Mould to stay ahead of the curve and anticipate the evolving needs of the industries they serve.
In addition to their commitment to quality and innovation, China Graphite Mould places a strong emphasis on customer satisfaction. The company works closely with each of their clients to understand their unique requirements and provide tailored solutions that meet their specific needs. Whether it's a custom mold design or a large-scale production run, China Graphite Mould has the expertise and flexibility to deliver results that exceed expectations.
The recent expansion of China Graphite Mould's production capacity comes in response to the increasing demand for their products in both domestic and international markets. With a growing customer base and a reputation for excellence, the company is poised for continued success and growth in the years to come. By investing in new technology and infrastructure, China Graphite Mould is committed to staying at the forefront of the industry and continuing to provide the highest quality graphite molds to their customers.
As China Graphite Mould looks to the future, they remain dedicated to upholding their core values of quality, innovation, and customer satisfaction. With a relentless pursuit of excellence, the company is well-positioned to meet the evolving needs of the industries they serve and continue to be a preferred supplier for precision graphite molds.
In conclusion, China Graphite Mould's expansion of their production capacity is a testament to their commitment to delivering high-quality products and customer-focused solutions. With a strong focus on innovation and a dedication to excellence, the company is well-positioned for continued success in the global market. As they continue to grow and evolve, China Graphite Mould remains a reliable partner for industries in need of precision graphite molds.
Company News & Blog
High-Quality Edm Mold for Graphite: What You Need to Know
Graphite EDM Mold: A Cutting-Edge Solution for Precision ManufacturingIn today’s fast-paced manufacturing industry, precision and efficiency are paramount. Companies are constantly seeking innovative solutions to stay ahead of the competition, and one such solution that has been garnering attention is the Graphite EDM Mold. This cutting-edge technology is revolutionizing the way manufacturers produce intricate and complex parts, and it is quickly becoming a staple in the arsenal of high-tech manufacturing companies.The Graphite EDM Mold is a precision tool used in electrical discharge machining (EDM) processes, which involves using electrical discharges to shape and produce intricate parts from hard metals and materials. The mold is made from high-quality graphite, which is an ideal material for EDM applications due to its high thermal conductivity and ability to withstand high temperatures.One company that has been at the forefront of developing and producing Graphite EDM Mold is {Company Name}. With over 20 years of experience in the manufacturing industry, {Company Name} has established itself as a leading provider of advanced tooling solutions for a wide range of industries, including aerospace, automotive, medical, and more. Their commitment to innovation and quality has led to the development of the Graphite EDM Mold, which has become a game-changer for manufacturers looking to produce intricate and high-precision parts.The Graphite EDM Mold offers several key advantages over traditional tooling solutions. Its high thermal conductivity allows for efficient heat dissipation during the EDM process, which results in improved surface finish and dimensional accuracy of the machined parts. Additionally, the inherent strength and stability of graphite make the mold highly durable and resistant to wear, resulting in longer tool life and reduced production downtime for tool changes.Furthermore, the Graphite EDM Mold is highly customizable and can be tailored to meet the specific needs of different applications and industries. {Company Name} offers a range of customization options, including varying graphite grades, electrode geometries, and surface finishes, to ensure that their customers can achieve the desired machining results for their unique parts.The use of Graphite EDM Mold has brought about a paradigm shift in the way manufacturers approach the production of complex and precision parts. With its ability to achieve tight tolerances and intricate geometries, the mold has opened up new possibilities for designing and manufacturing parts that were previously deemed too challenging or costly to produce.The aerospace industry, in particular, has embraced the Graphite EDM Mold as a critical tool for producing components with stringent tolerances and complex geometries. From turbine blades to fuel nozzles, manufacturers in the aerospace sector have turned to this advanced tooling solution to achieve the level of precision and quality required for their critical components.In the medical industry, the Graphite EDM Mold has also become instrumental in the production of intricate surgical instruments and implants. The mold’s ability to produce intricate and complex shapes with high precision has enabled manufacturers to push the boundaries of what is possible in terms of design and functionality for medical devices.Looking ahead, the future of Graphite EDM Mold looks promising, with continued advancements in materials and manufacturing techniques. As the demand for high-precision components continues to grow across various industries, the role of the Graphite EDM Mold is expected to expand even further, driving innovation and pushing the boundaries of what can be achieved in precision manufacturing.In conclusion, the Graphite EDM Mold has emerged as a cutting-edge solution for precision manufacturing, offering unparalleled capabilities to produce intricate and complex parts with high precision and efficiency. With {Company Name} at the helm of its development and production, the mold is poised to revolutionize the manufacturing industry and pave the way for new possibilities in design and production. As the demand for high-precision components continues to grow, the Graphite EDM Mold is set to play an increasingly pivotal role in shaping the future of manufacturing.
Discover the Benefits of Using Graphite Electrode Rods in Industrial Applications
Title: Innovative Electrode Graphite Rod Revolutionizes Renewable Energy StorageIntroduction:(Graphic: Illustration of Electrode Graphite Rod in Industrial Setting)In an exciting breakthrough in renewable energy storage, an elusive yet revolutionary Electrode Graphite Rod has been developed, promising to transform the renewable energy landscape. This groundbreaking technology, developed by a leading multinational corporation, is set to revolutionize the efficiency and sustainability of energy storage systems. Let us delve into the key features of the Electrode Graphite Rod and its potential impact on the global energy sector.1. Overview of the Electrode Graphite Rod:The Electrode Graphite Rod, developed by the company, is a next-generation technology designed to enhance the performance of energy storage devices. It is a highly conductive and durable rod constructed from advanced, layered graphite materials. With its exceptional heat resistance and chemical stability, this electrode offers unmatched longevity and reliability, ensuring prolonged energy storage capabilities.2. Advantages and Features:a. High Energy Density: The Electrode Graphite Rod delivers impressive energy density, allowing for increased storage capacity in smaller, more compact systems. This advanced design enables the adoption of renewable sources of energy at a much larger scale, providing a more sustainable future.b. Fast Charging and Discharging: With enhanced conductivity and performance, the Electrode Graphite Rod enables rapid charging and discharging processes. This feature significantly reduces the charging time and increases the efficiency of energy storage systems, enhancing their overall performance and reliability.c. Extended Lifespan: By utilizing graphite with exceptional durability, the Electrode Graphite Rod offers a significantly longer lifespan compared to conventional electrode materials. This longevity not only reduces maintenance costs but also contributes to a more sustainable energy storage infrastructure.d. Eco-Friendly: The company prioritizes environmental sustainability, and the Electrode Graphite Rod is no exception. By harnessing clean and renewable energy sources and reducing carbon emissions, this innovative technology ensures a greener energy future for generations to come.3. Applications and Potential:a. Renewable Energy Storage: The robust and efficient Electrode Graphite Rod has the potential to revolutionize the field of renewable energy storage. It paves the way for the widespread adoption of renewable sources such as solar and wind power, by overcoming the limitations of intermittent generation and providing a stable and reliable energy supply.b. Electric Vehicles: The high energy density and fast charging capabilities of the Electrode Graphite Rod make it a perfect fit for electric vehicle (EV) batteries. With its exceptional performance, EVs powered by these batteries will have extended driving ranges and reduced charging times, driving the global adoption of greener transportation.4. Future Prospects:The introduction of this game-changing Electrode Graphite Rod marks a significant milestone in the quest for reliable and efficient renewable energy storage. By incorporating this innovative technology into existing energy storage systems and developing new applications, the company aims to accelerate the transition towards a sustainable energy ecosystem. Moreover, with ongoing research and development efforts, the company is committed to continuously refining and optimizing the Electrode Graphite Rod to unlock even greater potential in the future.Conclusion:With the Electrode Graphite Rod, the company has achieved a remarkable advancement in energy storage technology, ushering in a new era of reliability, efficiency, and sustainability. Its innovative features and unparalleled performance capabilities offer tremendous potential in transforming the renewable energy sector. As this technology gains momentum, it brings us closer to achieving a cleaner, greener, and more sustainable future for all.
Discover the Essential Functions and Applications of a Rotary Kiln
Title: Revolutionary Rotary Kiln Technology Poised to Transform the IndustryIntroduction:In a world constantly seeking more sustainable alternatives, the renowned engineering company {} is set to revolutionize the industry with their groundbreaking rotary kiln technology. Offering a comprehensive solution to address the challenges of traditional processes, their innovative rotary kiln design aims to significantly reduce carbon emissions, improve energy efficiency, and enhance the long-term sustainability of production across various sectors.Body:1. The Need for Innovations in Rotary Kiln Technology (150 words):The conventional rotary kiln has been widely used in industries like cement, minerals, and chemicals, among others, for decades. However, it inherently suffers from several shortcomings, including high energy consumption, significant greenhouse gas emissions, and limited operational flexibility. As the world increasingly prioritizes eco-friendliness and sustainability, there has been a growing demand for advanced technologies that can mitigate the environmental impact of manufacturing processes.2. Introducing the Revolutionary {} Rotary Kiln (150 words):{} has heeded this call for change by developing an exceptional rotary kiln technology that promises to reshape the industry. By incorporating cutting-edge engineering principles, this innovative design optimizes energy efficiency while drastically reducing carbon emissions. Transforming the conventional rotary kiln into an advanced and sustainable solution, the new design enables production plants to meet strict environmental regulations, achieve substantial cost savings, and enhance operational flexibility.3. Key Features and Benefits (200 words):The updated rotary kiln design integrates several game-changing features, elevating its performance and sustainability. A few significant highlights include:a. Enhanced Energy Efficiency: The {} rotary kiln utilizes advanced heat recovery systems and optimized insulation techniques, significantly improving thermal efficiency and reducing energy consumption. This leads to substantial cost savings and a more sustainable manufacturing process.b. Reduced Carbon Footprint: By effectively capturing and neutralizing harmful greenhouse gas emissions, the new rotary kiln technology helps industries make substantial progress towards achieving their carbon reduction goals. The design minimizes toxic pollutant discharge into the atmosphere, ensuring compliance with stringent environmental regulations.c. Operational Flexibility: {} rotary kiln technology offers remarkable flexibility, allowing for the processing of a wide range of materials, including cement, minerals, and even industrial waste. This versatility enables production plants to adapt quickly to changing market demands, minimizing downtime and maximizing operational efficiency.d. Enhanced Safety Features: The new rotary kiln design incorporates state-of-the-art safety measures, ensuring the well-being of workers while minimizing the risk of accidents or incidents during operation.4. Applications and Potential Impact (200 words):The profound impact of the revolutionary {} rotary kiln technology extends to a myriad of industries. Cement manufacturers can vastly reduce their carbon footprint and energy costs, while simultaneously increasing cement production capacity. Furthermore, the mineral processing industry can achieve greater efficiency and cost-effectiveness in extracting valuable minerals.Additionally, the steel industry can leverage this technology to improve energy efficiency and decrease carbon emissions in the production of iron ore pellets. Other potential applications include the treatment of hazardous waste and the production of alternative fuels from biomass and municipal solid waste, fostering a circular economy.5. Collaboration and Future Outlook (100 words):{} is actively seeking collaborative partnerships with industry leaders to further refine and implement their cutting-edge rotary kiln technology. By combining their technical expertise with the industry's demands, {} aims to continuously enhance their innovative solution and drive sustainability across various sectors globally.Conclusion:With the introduction of their revolutionary rotary kiln technology, {} has opened up a new era for the industry, providing a transformative approach to energy efficiency, reduced carbon emissions, and enhanced operational flexibility. As industries rapidly transition towards sustainability, this innovation stands poised to become the go-to solution, ensuring a greener and more efficient manufacturing landscape for generations to come.
High-Quality Graphite Ingot Mold for Silver - A Must-Have for Silver Smiths
Graphite Ingot Mold For Silver Revolutionizes Precious Metal CastingIn the world of precious metal casting, precision and quality are the utmost importance. That's why the latest innovation in the industry has been making waves— the Graphite Ingot Mold For Silver. This revolutionary product, designed and manufactured by a leading company in the industry, has been changing the way silver ingots are being produced.The company behind this groundbreaking invention has been a pioneer in the field of graphite products for numerous industries, including the jewelry, aerospace, and automotive sectors. With a strong focus on research and development, they have been able to create cutting-edge solutions that have garnered attention and praise worldwide.The Graphite Ingot Mold For Silver is the latest addition to their extensive product line, and it has quickly gained recognition for its superior quality and performance. Made from high-quality graphite material, this mold is designed to withstand extreme temperatures and provide exceptional thermal conductivity, ensuring that the silver is cast with precision and accuracy.One of the key features of this graphite ingot mold is its durability and longevity. Unlike traditional molds, which are prone to wear and tear over time, this innovative product is built to last, making it a cost-effective and reliable investment for any precious metal casting operation.Another unique aspect of the Graphite Ingot Mold For Silver is its versatility. It can be used for a wide range of silver casting applications, including jewelry making, investment casting, and industrial manufacturing. This flexibility makes it a valuable tool for businesses of all sizes, whether they are just starting out in the industry or have been established for decades.Furthermore, the company's commitment to sustainability and environmental responsibility is evident in the manufacturing process of this ingot mold. By using high-quality graphite material, they have been able to create a product that is not only efficient and effective but also eco-friendly.The Graphite Ingot Mold For Silver has already garnered positive feedback from industry professionals and businesses that have integrated it into their operations. Many have praised its ability to produce high-quality silver ingots with minimal wastage, ultimately leading to cost savings and improved production efficiency."We have been using the Graphite Ingot Mold For Silver for several months now, and the results have been outstanding. The precision and consistency of the silver casts have allowed us to elevate the quality of our products, which has been well-received by our customers," shared a satisfied client.In addition to its performance benefits, the company has also provided exceptional customer support and technical assistance to ensure that businesses can fully maximize the potential of this innovation.Looking ahead, the future of precious metal casting looks promising with the introduction of the Graphite Ingot Mold For Silver. With its unmatched quality, durability, and versatility, this product is set to revolutionize the industry and set new standards for silver casting.In conclusion, the development and introduction of the Graphite Ingot Mold For Silver by the company have proven to be a game-changer in the precious metal casting industry. With its superior quality, performance, and sustainability, this innovation is poised to reshape the way silver ingots are produced and pave the way for a more efficient and eco-friendly casting process. As the industry continues to evolve, this product stands as a testament to the company's dedication to innovation and excellence.
Unveiling the Power of Ignot Molds for Graphite Mold Formation
Graphite Ignite Mold Revolutionizing Casting IndustryThe ever-evolving world of manufacturing has seen significant advancements in recent years, one of which is the development of the revolutionary Graphite Ignot Mold. (remove brand name) Combining cutting-edge technology with the expertise of a leading company in the field, this innovative solution is transforming the traditional casting industry, offering numerous benefits that were previously unimaginable.Casting has been a fundamental process in manufacturing for centuries. From the production of intricate metal components to the creation of larger industrial parts, casting allows for the mass production of objects with remarkable precision. However, conventional casting methods often face challenges such as product defects, high production costs, and extended lead times.Recognizing these limitations, (remove brand name) developed the Graphite Ignite Mold as a game-changing solution. The company has been a pioneer in the manufacturing industry for over two decades, continually pushing the boundaries of innovation. With their expertise and research, they have successfully revolutionized the casting process, improving efficiency, product quality, and overall productivity.The Graphite Ignite Mold, a highly specialized tool made from superior quality graphite, has become the cornerstone of this revolutionary casting technique. With its exceptional thermal conductivity and resistance to high temperatures, the mold ensures uniform heat distribution, reducing the likelihood of thermal stress and material defects. Additionally, the mold's ability to withstand extreme heat allows for faster solidification, resulting in reduced casting cycle times.One of the most significant advantages offered by the Graphite Ignite Mold is its versatility. Unlike traditional molds that are limited in terms of complexity and design, the graphite mold can accommodate even the most intricate geometries, enabling manufacturers to create highly customized components effortlessly. This flexibility makes the mold particularly appealing in industries such as aerospace, automotive, and electronics, where intricate designs are crucial for optimal performance.The introduction of this groundbreaking technology has transformed the casting process, significantly reducing the production costs associated with tooling and post-casting machining. By eliminating the need for complex tooling, manufacturers can save time and resources, resulting in substantial cost savings. Moreover, the high-quality surface finish achieved with the graphite mold often eliminates the need for additional machining processes, further streamlining the manufacturing timeline.A key aspect of (remove brand name)'s commitment to sustainability is the Graphite Ignite Mold's ability to be easily recycled. Unlike traditional casting molds that are often discarded after a single use, the graphite mold is designed to withstand multiple casting cycles. Once a casting is complete, the mold can be easily cleaned and reused, reducing waste and minimizing the environmental impact of the manufacturing process.The successful implementation of the Graphite Ignite Mold has garnered significant attention from the manufacturing industry and has given (remove brand name) a distinct competitive edge. With its combination of innovative technology, unmatched expertise, and cost-effective solutions, the company has established itself as a leader in the field, helping manufacturers across various industries overcome the challenges associated with traditional casting methods.Looking ahead, (remove brand name) continues to invest in research and development, constantly striving to improve their graphite mold technology. By collaborating with industry leaders, they aim to further optimize the mold's performance and expand its applications, ensuring that manufacturers can continue to benefit from the advantages offered by this groundbreaking solution.In conclusion, the emergence of the Graphite Ignite Mold has revolutionized the casting industry. With its ability to deliver unparalleled precision, reduced production costs, and sustainability, this innovative solution is paving the way for a new era of manufacturing. As (remove brand name) continues to drive advancements in this technology, the future of casting looks increasingly promising, with improved efficiency and endless possibilities for customization.
Next-Generation Semiconductor Material Breaking Barriers in Electronics Industry
The rise of electric vehicles has put the spotlight on new technologies that can provide the power and efficiency required for this growing market. One of the key technologies that enable electric vehicles to travel long distances is power electronics. This technology is what allows electricity to be stored and transported in a vehicle's battery pack and converted into high-voltage power that can drive the motor. Silicon Carbide (SiC) is emerging as a key player in this space, thanks to its capabilities to deliver high-efficiency, high-reliability power electronics.SiC has been around for a long time as a semiconductor material, but only recently has it gained traction in the power electronics industry. This is because it offers many advantages over traditional semiconductor materials like silicon, which is currently in widespread use. One of the key advantages of SiC is that it can handle higher voltages than silicon, which makes it ideal for use in high-power devices like electric vehicle inverters.Another advantage of SiC is its ability to operate at higher temperatures than silicon, which means it can handle more power without failing. This is particularly important in electric vehicles, where the power electronics need to operate at maximum efficiency for extended periods. SiC's high thermal conductivity also helps to keep the temperature down, reducing the need for bulky cooling systems.SiC offers increased efficiency, with the ability to reduce power losses and extend the driving range of electric vehicles. This makes SiC an important technology for providing the power and performance needed for the next generation of electric vehicles. The market is responding to this demand, with SiC-related businesses intensifying R&D efforts on this emerging technology.One company that has been at the forefront of SiC development is {company}. The company has invested heavily in SiC technology, and is now one of the leading players in the SiC market. The company's products cover a range of SiC applications, including power devices, modules, and systems. They specialize in designing and manufacturing SiC products that meet the highest quality standards, specifically for the automotive and industrial markets.{Company} has developed a range of SiC products that are tailored to meet the growing demand for high-performance electric vehicles. Their products offer high efficiency, superior reliability, and an extended lifespan compared to traditional silicon-based products. Their SiC MOSFETs, in particular, have been designed specifically for the electric vehicle market, offering high performance, compact size, and high reliability.In addition to their SiC MOSFETs, {company} has a range of SiC products that are suitable for a variety of applications, including renewable energy, industrial automation, and high-frequency communications. Their SiC modules are highly efficient and compact, making them ideal for use in electric vehicle chargers, battery management systems, and other high-power applications.{Company} is also involved in the development of next-generation SiC technology, including the development of 200mm SiC wafer production technology. This technology is expected to significantly increase the supply of SiC wafers, making them more accessible and cost-effective for a wider range of applications.In conclusion, the demand for high-performance electric vehicles is driving the development of new power electronics Technologies. SiC is emerging as a key player in this space, offering high efficiency, superior reliability, and an extended lifespan compared to traditional semiconductor materials. Companies like {company} have invested heavily in SiC technology and are developing innovative products that meet the demands of the rapidly growing electric vehicle market. As the market continues to expand, SiC is expected to play an increasingly important role in driving the next phase of electric vehicle growth.
Manufacturer of High-Quality Carbon and Graphite Rods and Blocks for Industrial Applications
NAC Carbon Products, a leading manufacturer of carbon and graphite rods and blocks, has announced that it is expanding its product line to include new grades of materials equivalent to the carbide graphite group. The expansion is in line with the company's commitment to providing high-quality products that meet the evolving needs of its customers.Founded in 1956 as National Carbon Company, NAC Carbon Products has a long history of providing custom-made carbon and graphite components for a wide range of applications. From automotive to aerospace, from industrial equipment to medical devices, the company's products have gained a reputation for their durability and performance."We take pride in the quality of our products, and we are constantly looking for ways to improve them," said John Doe, the CEO of NAC Carbon Products. "Expanding our materials portfolio is one way to do that. By offering new grades of carbide graphite, we can provide our customers with more options and help them achieve better results."Carbide graphite is a group of materials that offer excellent combination of strength, hardness, and thermal conductivity. They are widely used in high-performance applications such as cutting tools, dies, and molds. NAC Carbon Products' new grades of carbide graphite rods and blocks are designed to meet the specific requirements of these applications, offering superior resistance to wear, deformation, and thermal shock."We have worked closely with our suppliers and customers to develop these new grades of carbide graphite," said Jane Smith, the Sales Manager at NAC Carbon Products. "We have tested them extensively, both in our own facilities and in the field, and we are confident that they will deliver the performance and reliability that our customers expect."The new grades of carbide graphite rods and blocks are available in a variety of sizes and shapes, and can be custom-made to meet specific requirements. They can be machined, drilled, and fitted with inserts and other features, making them highly adaptable to different applications."Customization is our specialty," said Smith. "We have a team of engineers and technicians who are experts in carbon and graphite materials, and who can work closely with our customers to design and manufacture components that are tailored to their needs. Whether it's a large-scale project or a small prototype, we are committed to delivering the best solution."NAC Carbon Products' expansion into the carbide graphite market is part of a broader strategy to diversify its product line and strengthen its position in the industry. The company is investing in new equipment and technologies, and is expanding its global reach through partnerships and alliances."We are confident in the future of the carbon and graphite industry," said Doe. "There is a growing demand for materials that offer exceptional performance in harsh environments, and we believe that our expertise and innovation will be key to meeting that demand. Our new grades of carbide graphite are just one example of how we are pushing the boundaries of what's possible."NAC Carbon Products is a privately-owned company that employs over 200 people worldwide. Its headquarters and main production facilities are located in Cleveland, Ohio, USA, with additional offices and warehouses in Europe and Asia. The company is ISO 9001-certified and follows strict quality control procedures to ensure that its products meet the highest standards."We are proud to be a leader in the carbon and graphite industry," said Doe. "We are dedicated to providing our customers with the best possible products and services, and to contributing to the advancement of science and technology. We believe that our new grades of carbide graphite will help us achieve those goals, and we look forward to seeing the impact they will have on the industry.
Durable Container for Hard Alloy: Innovative Solution for Storing Graphite Materials
Graphite Container for Hard Alloy Revolutionizes the Manufacturing Industry(Graphite Container for Hard Alloy) – In a groundbreaking development, a new innovative product, the Graphite Container for Hard Alloy, has been introduced by an industry-leading company. This game-changing technology is set to revolutionize the manufacturing industry by enhancing the production process of hard alloy materials.Hard alloys, also known as cemented carbides, are widely used in various industries due to their exceptional hardness, wear resistance, and strength. They are particularly prevalent in the automotive, aerospace, and tool manufacturing sectors. However, the conventional manufacturing process for hard alloys involves sintering, which involves compacting powdered metals at high temperatures and pressures. This process often leads to various challenges, such as deformation, cracks, and high scrap rates.The Graphite Container for Hard Alloy, developed by the pioneering company, aims to overcome these obstacles by providing a more efficient and cost-effective sintering solution. This advanced technology utilizes graphite, a material known for its high thermal conductivity and strength, as a container for the sintering process.By employing the Graphite Container for Hard Alloy, manufacturers can achieve greater control over the heat transfer during sintering. The unique properties of graphite allow for even distribution of heat, eliminating the risk of deformation and cracks in the hard alloy materials. This groundbreaking technology ensures consistent sintering quality, reducing scrap rates significantly.Moreover, the use of the Graphite Container for Hard Alloy offers several additional advantages. Firstly, the thermal conductivity of graphite allows for faster heat transfer, thereby reducing overall sintering time. This efficiency improvement translates into increased productivity and reduced production costs for manufacturers.Secondly, the graphite container boasts high chemical resistance, preventing any reaction between the container and the hard alloy material during the sintering process. This compatibility ensures the purity and integrity of the final product, enhancing its quality and performance.The Graphite Container for Hard Alloy is also highly durable and long-lasting. Its robust design enables it to withstand multiple sintering cycles without degradation or performance loss. This longevity contributes to the cost-effectiveness of the technology by reducing the need for frequent container replacements.In addition to these functional benefits, the implementation of the Graphite Container for Hard Alloy aligns with the growing focus on sustainability and eco-friendly manufacturing practices. This advanced technology reduces energy consumption and CO2 emissions since the shorter sintering time leads to lower energy requirements. Furthermore, the reduction in scrap rates minimizes material waste, contributing to a greener manufacturing process.The company behind this groundbreaking innovation, known for its commitment to research and development, has an established track record of delivering cutting-edge solutions to the manufacturing industry. With years of experience and expertise in the field of hard alloy production, they have successfully harnessed the potential of graphite to develop the Graphite Container for Hard Alloy.As this new technology gains traction in the manufacturing industry, it has the potential to revolutionize the way hard alloys are produced. The enhanced control over the sintering process, improved quality of the final product, increased productivity, and reduced environmental impact make the Graphite Container for Hard Alloy a game-changer in the industry.Manufacturers across various sectors will now have access to an innovative solution that addresses the challenges associated with traditional sintering methods. The introduction of this technology paves the way for more efficient, cost-effective, and sustainable production of hard alloy materials.In conclusion, the Graphite Container for Hard Alloy, developed by an industry-leading company, offers a revolutionary solution to the manufacturing industry. By harnessing the unique properties of graphite, this innovative technology enhances the sintering process, ensuring quality, efficiency, and sustainability. As manufacturers adopt this game-changing solution, they can look forward to improved production processes and enhanced hard alloy materials.
High Frequency Induction Crucibles: A Complete Guide
High Frequency Induction Crucibles Revolutionizing the Foundry IndustryThe foundry industry has witnessed a remarkable transformation with the innovation of high frequency induction crucibles. This cutting-edge technology has not only improved the efficiency of the melting process but has also significantly reduced energy consumption and operational costs for foundry businesses. The introduction of high frequency induction crucibles by {company name} has set a new benchmark for the foundry industry, providing an advanced and sustainable solution for metal melting applications.{Company name} is a leading manufacturer and supplier of high-quality induction heating equipment and solutions for various industrial applications. With a strong focus on research and development, the company has introduced a range of innovative products that cater to the evolving needs of the foundry industry. Their high frequency induction crucibles have an impressive track record of delivering exceptional performance, efficiency, and cost-effectiveness, making them the preferred choice for foundry operators around the world.The key features and advantages of high frequency induction crucibles offered by {company name} include:1. Energy Efficiency: The advanced design of high frequency induction crucibles ensures efficient and uniform heating of the metal charge, resulting in reduced energy consumption and minimal heat loss. This not only lowers operational costs but also contributes to environmental sustainability by minimizing the carbon footprint of foundry operations.2. Rapid Heating: High frequency induction crucibles are engineered to deliver fast and precise heating of metal charges, allowing for quicker melting cycles and improved productivity. The ability to achieve high temperatures in a short time enhances the overall efficiency of the melting process, enabling foundries to meet production targets with ease.3. Versatility: {Company name}'s high frequency induction crucibles are designed to accommodate a wide range of metal alloys, making them suitable for a diverse set of foundry applications. Whether it's iron, steel, aluminum, or other non-ferrous metals, these crucibles offer exceptional versatility and adaptability to meet the specific requirements of different foundry operations.4. Durability and Reliability: The high-quality construction and materials used in the manufacturing of high frequency induction crucibles ensure durability and longevity, minimizing downtime and maintenance costs for foundry businesses. These crucibles are built to withstand the rigors of continuous operation, providing reliable performance and consistency over extended periods.5. Safety and Control: {Company name} has incorporated advanced monitoring and control systems into their high frequency induction crucibles, ensuring safety and precision in the melting process. Operators have the ability to monitor and adjust parameters such as temperature, power input, and cycle times, leading to a controlled and efficient melting operation.The impact of high frequency induction crucibles on the foundry industry has been nothing short of revolutionary. Foundry businesses that have embraced this technology have witnessed substantial improvements in their operational efficiency, productivity, and cost-effectiveness. The ability to achieve higher melting temperatures in less time, with lower energy consumption, has positioned high frequency induction crucibles as a game-changer in the metal melting process.{Company name} continues to drive innovation in the foundry industry, with a commitment to providing cutting-edge solutions that empower foundry businesses to thrive in a competitive market. The company's dedication to research, development, and customer satisfaction has solidified its position as a trusted partner for foundry operators worldwide.In conclusion, high frequency induction crucibles offered by {company name} have redefined the standards of efficiency and performance in the foundry industry. With their remarkable energy efficiency, rapid heating capabilities, versatility, durability, and advanced control systems, these crucibles have become the preferred choice for foundries seeking to enhance their melting operations. {Company name}'s relentless pursuit of innovation and excellence continues to shape the future of the foundry industry, setting new benchmarks for sustainable and high-performing metal melting solutions.