Discover the Benefits of Exothermic Welding Molds for Efficient Joining Processes
By:Admin
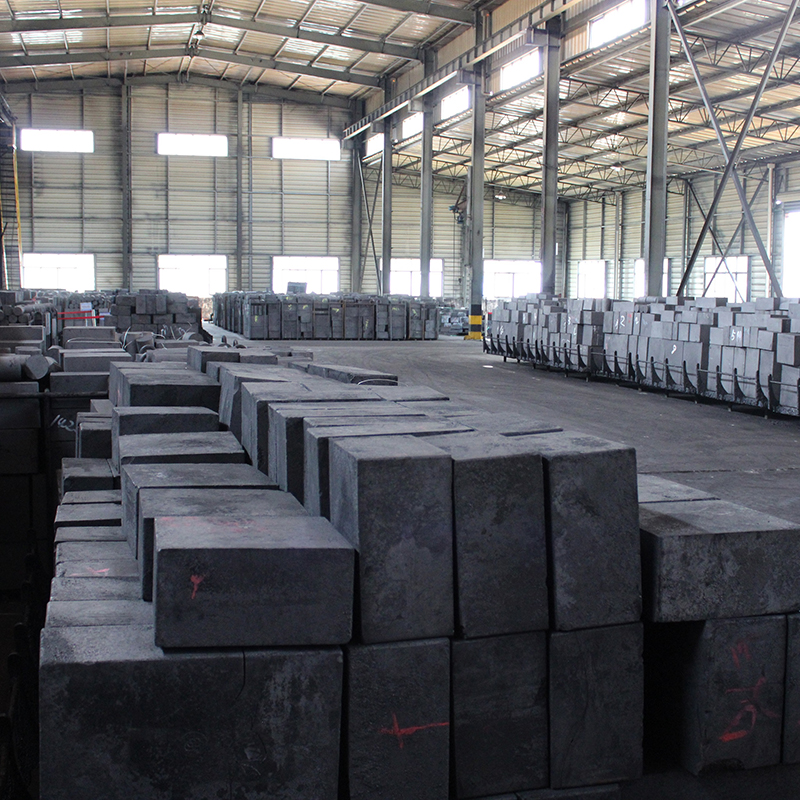
Exothermic welding, also known as cadwelding, is a popular method in the industrial sector for creating strong connections between two wires, cables or metal surfaces. This process involves a controlled explosion created by a chemical reaction that melts the wire ends and filler material, joining them into a homogeneous mass. The resulting connection is high conductivity, corrosion-resistant, and mechanically strong, which makes it ideal for applications in power and telecommunications industries.
One of the critical components of exothermic welding is the mold, which holds the wires and filler material in place during the reaction. The mold must be precisely designed and manufactured to ensure a uniform reaction and consistent results. A leading player in this field is a company that produces exothermic welding molds of the highest quality, with superior materials, innovative design, and strict quality control.
This company has been in the industry for many years, supplying a vast range of products to customers around the world. They have invested heavily in research and development, as well as manufacturing facilities, to ensure their molds meet the most stringent standards. They have also established a robust logistics network to deliver products in a timely and cost-effective manner.
Their exothermic welding molds are designed for use in a wide range of applications, from low-voltage grounding and bonding to high-voltage transmission and distribution. They are suitable for joining copper, aluminum, brass, and steel wires, and can accommodate various sizes and shapes. Their molds come in different configurations, including vertical, horizontal, and angled, to meet specific customer requirements.
The company's exothermic welding molds are made from high-quality materials, such as graphite, ceramic, and steel, which can withstand high temperatures and pressure. They are also coated with special materials that prevent oxidation, corrosion, and buildup, which can affect the quality of the connection. The molds are designed to be reusable, with easy-to-replace parts, saving customers time and money in the long run.
In addition to producing molds, the company also offers training and support services to customers, ensuring they can operate the equipment safely and efficiently. They have a team of experts with extensive knowledge and experience in exothermic welding who can provide technical support, advice, and troubleshooting. They also offer custom machining services to meet specific customer requirements.
The company's dedication to quality, innovation, and customer service has earned them a reputation as one of the leading manufacturers of exothermic welding molds in the industry. They have a vast network of distributors and partners in different countries, who can provide local support and services. They are also committed to sustainability, minimizing their environmental impact, and promoting social responsibility.
In conclusion, exothermic welding is an essential process in the industrial sector, and the quality of the molds used plays a crucial role in the final results. The company described above is a leader in this field, producing high-quality exothermic welding molds that meet the most stringent standards. Their molds are designed to be durable, reliable, and easy to use, with excellent support and training services. As the demand for exothermic welding grows, this company is well-positioned to continue providing innovative solutions for their customers' needs.
Company News & Blog
Vacuum Metallizing Machine for Roll-to-Roll Production of Alloy Films on PET, BOPP, CPP, PVC, and Paper
Roll to Roll Alloy Film Vacuum Metallizing Machine for Pet BOPP CPP PVC Paper - Graphite Crucible for Vacuum Metallizing FilmVacuum metallizing is the process of depositing a thin film of metal onto a substrate, such as plastic, paper, or glass, in a vacuum environment. This process is widely used in various industries, including packaging, automotive, cosmetics, and electronics. In this blog post, we will discuss the Roll to Roll Alloy Film Vacuum Metallizing Machine for Pet BOPP CPP PVC Paper and the importance of using Graphite Crucibles in the vacuum metallizing process.Roll to Roll Alloy Film Vacuum Metallizing MachineThe Roll to Roll Alloy Film Vacuum Metallizing Machine for Pet BOPP CPP PVC Paper is a type of web vacuum coater designed to deposit a thin film of metal alloy onto a continuous roll of material such as plastic, paper, or fabric. This type of vacuum metallizing machine is widely used in the packaging industry for producing decorative and functional films for a range of packaging applications. The machine is equipped with a vacuum chamber, a metal alloy deposition system, and a roll-to-roll web transport system. The substrate material is fed from a roll into the vacuum chamber, where it is pre-treated and then coated with a thin layer of metal alloy. The metal alloy is vaporized and deposited onto the substrate in a thin, uniform layer. The Roll to Roll Alloy Film Vacuum Metallizing Machine for Pet BOPP CPP PVC Paper has several advantages over other deposition techniques. It can produce films with high uniformity and consistency, is cost-effective, and supports high-volume production. Graphite Crucibles for Vacuum Metallizing FilmGraphite Crucibles are an essential component of the vacuum metallizing process. They are used to hold the metal alloy and heat it until it vaporizes and is deposited onto the substrate. The graphite crucible serves as a container for the metal alloy, which is heated to a temperature at which it vaporizes. The vaporized metal alloy is then deposited onto the substrate in the vacuum chamber.Graphite Crucibles are ideal for vacuum metallizing because they can withstand high temperatures, are chemically inert, and have excellent thermal conductivity. The crucibles are designed to withstand the harsh conditions of the vacuum chamber and ensure that the metal alloy is heated and vaporized evenly.ConclusionThe Roll to Roll Alloy Film Vacuum Metallizing Machine for Pet BOPP CPP PVC Paper is a critical component of the packaging industry. It enables the production of high-quality, functional, and decorative films at scale. However, to achieve the desired effect, it is essential to use high-quality Graphite Crucibles. Graphite Crucibles are essential to the vacuum metallizing process as they help to ensure that the conditions in the vacuum chamber are optimal for the vaporization of the metal alloy and the deposition of the thin film. With high-quality Graphite Crucibles, manufacturers can produce high-quality, durable, and decorative films that meet the needs of their customers.
Small Electric Foundry for Bronze Casting: Tips and Techniques for Successful Results
Electric Foundry for Small Bronze Casting – Crucible for Melting BronzeBronze casting has been around for thousands of years. It is an ancient method of creating beautiful objects of art. Today, modern technology has made it easier for people to attempt bronze casting on their own. This is where a small electric foundry comes in handy. In this article, we will discuss how to make a small foundry for melting tin bronze.First, let's talk about the materials we will need. The following items are essential for building a small foundry:1. Soft fire bricks – These bricks are used to build the walls of the foundry. They are designed to withstand high temperatures.2. Insulator – This is a high-temperature insulation material that is used to line the inside of the foundry. It keeps the heat inside the foundry and prevents it from escaping.3. Nichrome coil – This is a heating element that is used to provide the heat needed to melt the tin bronze.4. Crucible – This is a container used to melt the bronze. It must be made of a material that can withstand high temperatures and is resistant to corrosion.Now that we have the materials, let's get started on building the foundry. The first step is to build a frame with the soft fire bricks. The size of the frame will depend on the size of the crucible. The frame should be built to support the crucible and the insulator.Next, place the insulator inside the frame. The insulator should be cut to size and placed inside the frame. It should be wrapped around the sides and the bottom of the frame. The insulator is what will keep the heat inside the foundry.After the insulator is in place, wrap the nichrome coil around the outside of the insulator. The coil should be wrapped tightly and evenly around the entire foundry. It should be wired to a 240V 10amp socket. The coil is what will provide the heat necessary to melt the tin bronze.Once the coil is in place, it's time to add the crucible. The crucible should be placed inside the foundry and centered on the coil. It should be large enough to hold the amount of bronze you plan to melt. The crucible should be made of a material that can withstand high temperatures, such as graphite or ceramic.Finally, turn on the power to the coil. The heat should be gradually increased until the bronze is fully melted. Once the bronze is melted, it's ready for casting.ConclusionBuilding a small foundry for melting tin bronze is not a difficult task. With the right materials, it can be done easily at home. By using a soft fire brick frame, high-temperature insulation, a nichrome coil, and a crucible, you can create your own electric foundry. This will allow you to create beautiful bronze objects of art in the comfort of your own home. So, get started today and let your creativity flow!
How the World's First Graphite Heater is Revolutionizing Heating Systems" can be rewritten as "Discovering the Revolutionary Advantages of Graphite Heaters in Modern Heating Systems".
Graphite Heater Innovations Set to Revolutionize Heating TechnologyGraphite Heater Innovations (GHI) is a leading technology company specializing in the design and manufacture of state-of-the-art graphite heaters. The company prides itself in its ability to produce high-quality products that are energy-efficient, cost-effective, and environmentally friendly.GHI has been in operation for more than a decade and has amassed a wealth of experience in the field of heating technology. The company is committed to developing innovative products that meet the needs of commercial and industrial customers. Its products are used in a wide range of applications, including metallurgy, semiconductor manufacturing, chemical processing, and automotive production, among others.One of the company's most significant breakthroughs is the development of the Graphite Heater. The Graphite Heater is a unique heating element that can be customized to meet the specific needs of each customer. The heater is made from high-quality graphite and uses advanced technology to provide precise heating control. It is designed to be energy-efficient, which means it consumes less power compared to traditional heating systems. The result is a reduction in energy costs and an increase in overall productivity.The Graphite Heater is also environmentally friendly, as it produces lower emissions compared to other heating systems. It is designed to have a long lifespan, ensuring that customers can benefit from its efficiency and effectiveness for many years to come. The heater is easy to install and maintain, with minimal downtime required.GHI's innovative heaters have gained a reputation for their high quality, reliability, and efficiency. The company's team of experts works closely with its customers to ensure that they get the most out of their heating system. GHI offers a range of services, including technical support, maintenance, and repair, to ensure that its customers' needs are met promptly and efficiently.One of the company's recent projects involved the design and development of a heating system for a semiconductor manufacturing plant. The plant required a heating system that could provide a stable and precise temperature control to ensure the success of the manufacturing process. GHI was able to design a custom Graphite Heater that met the plant's specific needs, resulting in improved productivity and reduced energy costs.GHI has also been working with the automotive industry, developing heating systems for car parts. The company's heat technology has been used in the production of catalytic converters, which are essential in reducing the emissions from vehicles. GHI's Graphite Heater was chosen as it is energy-efficient and produces low emissions, making it an ideal solution for the automotive industry.In conclusion, Graphite Heater Innovations is a leading technology company that is revolutionizing the heating industry. Its innovative and energy-efficient products are changing the way that businesses approach heating, resulting in reduced costs, increased productivity, and improved environmental sustainability. With its commitment to quality and customer satisfaction, GHI is poised to continue leading the way in heating technology for many years to come.
Durable Graphite Boat for Square Applications Rises in Popularity: Market Insights and Analysis
Title: High-Quality Graphite Boat Facilitates Diverse Industrial ApplicationsIntroduction:Graphite, a versatile and durable material known for its excellent thermal and electrical conductivity, has taken center stage in various industrial applications. Amongst the leaders in graphite manufacturing, a renowned company has recently unveiled their cutting-edge Square Graphite Boat - a breakthrough product that is revolutionizing multiple industries. With a commitment to innovation and an unwavering focus on quality, this new graphite boat is set to address the needs of diverse sectors and contribute to their growth. 1. The Versatility of Graphite:Graphite, an allotrope of carbon, is highly valued for its unique properties, making it indispensable in numerous industries. It is widely used in manufacturing electrical products, semiconductors, batteries, fuel cells, and even in the aerospace industry due to its lightweight nature. The thermal stability and corrosion resistance of graphite also make it an ideal material for use in high-temperature furnaces, crucibles, and electrodes. Recognizing the potential of graphite, this pioneering company has introduced the Square Graphite Boat to enhance industrial processes across sectors.2. The Key Features of Square Graphite Boat:The Square Graphite Boat boasts several noteworthy features, making it stand out in the market. First and foremost, its impeccable design ensures uniform heat distribution, reducing the possibility of thermal stress cracks during high-temperature applications. The boat's superior thermal conductivity guarantees efficient heat transfer, resulting in enhanced productivity and reduced energy consumption. Furthermore, the boat's high-density graphite composition coupled with its exceptional machinability allows for intricate and precise customization, catering to the unique requirements of different industrial applications.3. Revolutionary Applications of Square Graphite Boat:(a) Semiconductor Manufacturing Sector:In the semiconductor industry, where precision and reliability are paramount, the high-purity graphite material of the Square Graphite Boat proves to be indispensable. Used as a critical component in thermal processes, this boat ensures optimal heat distribution, preventing defects in the delicate semiconductor wafers. The boat's longevity and resistance to chemical reactions make it a sustainable and cost-effective solution.(b) Energy Storage and Microelectronics Industry:With the rapid advancement in the development of energy storage devices such as lithium-ion batteries and fuel cells, the demand for quality graphite boats has surged. The Square Graphite Boat, with its excellent electrical conductivity, corrosion resistance, and uniform heat distribution, ensures the efficient functioning and extended lifespan of these energy storage devices, consequently benefiting the electric vehicle and renewable energy sectors.(c) Metallurgical and Chemical Industries:Graphite boats find their application in high-temperature processes like smelting and refining metals due to their superb thermal resistance. The Square Graphite Boat, thanks to its seamless design and superior thermal conductivity, optimizes these processes by reducing energy loss and enhancing heat transfer efficiency. Its chemical stability further ensures a clean, contaminant-free environment, making it invaluable in controlled chemical reactions and laboratory settings.4. Commitment to Quality and Sustainability:The company behind the Square Graphite Boat is committed to producing high-quality, sustainable products. They adhere to stringent quality control measures, ensuring that every boat manufactured meets industry standards and customer specifications. Additionally, their responsible sourcing practices guarantee the usage of eco-friendly materials, minimizing the environmental impact.Conclusion:The Square Graphite Boat represents a significant technological milestone in the graphite industry, addressing the evolving needs of diverse sectors. Its impeccable design, high thermal conductivity, and resistance to thermal stress cracks make it an indispensable tool in various high-temperature industrial processes. The versatile applications of this boat, from semiconductor manufacturing to energy storage and metallurgical industries, highlight its immense potential. With a strong focus on quality and sustainable practices, the company behind this innovative product is steadfastly contributing to the growth and development of industries around the globe.
Top Quality Graphite Crucibles for Aluminum Casting Available Now
Graphite Crucibles for Aluminium - The Crucial Commodity Driving the Global Metals IndustryThe global metals industry is witnessing a steady growth in demand for high-quality aluminium and its alloys, primarily driven by the rising requirements in the transportation and aerospace sectors. To meet this demand, aluminium manufacturers are required to use advanced technologies and quality materials. One such critical material used in the production of aluminium is graphite crucibles.Graphite crucibles are one of the most essential parts of the aluminium production process, and their correct selection plays a crucial role in maintaining the quality standards of the end product. In recent years, there has been a growing demand for graphite crucibles that are durable, heat-resistant, and can withstand the high temperatures required in the aluminium smelting process.A leading manufacturer of graphite crucibles for aluminium has been meeting this growing demand in the global market. This company, which has operations across Asia, Europe and North America, is known for its extensive range of quality graphite crucibles that cater to various stages of the aluminium production process. They offer an extensive range of high-performance graphite crucibles that are suitable for various furnace types, and can be customised according to specific customer requirements.The company has also been leveraging on advanced manufacturing technologies such as isostatic pressing, CNC machining, and computerized modelling to ensure consistent quality in their crucibles. They employ a rigorous quality control process at every stage of the production process to ensure that their products meet or exceed customer expectations.Moreover, this company has continued to invest in research and development to improve their product offerings and stay ahead of competitors. They have also been working closely with customers to develop customised solutions tailored to their unique manufacturing requirements.The company's graphite crucibles are highly sought after in the global market, with a considerable market share in key regions such as Asia, Europe, and North America. They serve a broad range of industries, including aerospace, automotive, construction, energy, and packaging.In recent years, the growth in demand for aluminium and its alloys has been driven by the increasing need for lightweight materials that offer high strength and durability. This trend has been particularly evident in the transportation and aerospace sectors, where manufacturers are required to reduce weight without compromising on safety or performance. Graphite crucibles have played a vital role in enabling manufacturers to meet these requirements and produce high quality aluminium and its alloys.Looking forward, the demand for graphite crucibles for aluminium is anticipated to continue growing, driven by the increasing adoption of lightweight materials in various industries. This trend is expected to result in new opportunities for the global graphite crucibles market, with manufacturers looking to expand their product offerings to cater to different stages of the aluminium production process.In conclusion, the graphite crucibles for aluminium market is a crucial commodity driving the global metals industry. The quality of graphite crucibles used in the aluminium production process is vital in ensuring consistent performance and quality of the end products. The leading manufacturer of graphite crucibles for aluminium has been meeting this demand by offering an extensive range of high-performance products, leveraging on advanced technologies and stringent quality control processes. With the increasing demand for lightweight materials, the graphite crucibles market is expected to grow, presenting new opportunities for manufacturers to cater to evolving customer requirements.
Micromachined Graphite Rotor Levitated by Diamagnetism for Frictionless Rotation: A Promising Mechanism for Microsensors and Microactuators
Based on Diamagnetic Levitation, Micromachined Graphite Rotor, and Frictionless Microsensors.The development of micromachined graphite rotor based on diamagnetic levitation is a significant breakthrough in the field of microsensors and microactuators. In this research project, a highly oriented pyrolytic graphite (HOPG) rotor is levitated above a permanent magnet structure, allowing for its friction-free rotation.The micropatterned HOPG rotor has four blades with a 1-mm inner diameter disc and a pair of 2-mm outer diameter together with the blades. The levitation height of 132 μm measured for the rotor matches well with a simulation result. The rotor's revolution is demonstrated with the application of gas flow, showing stable continuous actuation with a maximum rate of 500 r/min.The use of a sturdy diamagnetic material, such as HOPG, in micromachined rotors makes them highly valuable for frictionless microsensors. The absence of any friction allows for more precise readings and helps reduce measurement errors. Moreover, the use of diamagnetic levitation technology makes it possible to achieve frictionless motion without the need for complex mechanisms.The promising results of this research project suggest potential applications of the mechanism towards frictionless microsensors and microactuators. The use of micromachined graphite rotors based on diamagnetic levitation can lead to the development of smaller, more efficient, and accurate sensors and actuators.In conclusion, the development of micromachined graphite rotor based on diamagnetic levitation is a significant advancement in the field of microsensors and microactuators. The use of HOPG, a sturdy diamagnetic material, makes it possible to achieve frictionless motion, which can lead to the development of more accurate sensors and actuators. The promising results of this research project suggest potential applications in various industries, including healthcare, aerospace, and robotics.
Top-quality Isostatic Metal Casting Molds for High-performance EDM Graphite Marble Mold
High Performance EDM Graphite Marble Mold: A Boon for Isostatically Bearing Metal Casting MoldsMetal casting is one of the most widely used techniques employed for producing various metal products. It involves pouring molten metal into a mold and allowing it to solidify into the desired shape. However, this process is not as simple as it sounds. The metal has to be cast with precision to ensure that the final product meets the desired specifications. One way to ensure this is by using high-quality graphite molds. Graphite molds are extensively used in the metal casting industry due to their exceptional properties such as high thermal conductivity, excellent machinability, and low thermal expansion coefficient. The recent development of High-Performance EDM Graphite Marble Mold has revolutionized the industry.High-Performance EDM Graphite Marble Mold is one of the most advanced forms of graphite molds available today. This type of mold is made using high-quality isostatic graphite, which is a versatile and durable material. It is ideally suited for producing intricate and complex metal castings. The use of isostatic graphite ensures that the molds are free from any internal defects or cracks, which can affect the quality of the final product.The High-Performance EDM Graphite Marble Mold also employs the technique of Electrical Discharge Machining (EDM) to produce a precise and accurate mold. EDM is an advanced machining process in which electrical discharges are used to shape the material. It is an effective process for producing complex shapes with very high accuracy. The use of EDM in graphite mold production ensures that the molds are of the highest quality and precision.One of the key advantages of using High-Performance EDM Graphite Marble Mold is its exceptional thermal conductivity. Graphite has one of the highest thermal conductivity rates of any material. This allows the mold to quickly heat up and cool down, which is essential for producing metal castings with a high degree of accuracy. Moreover, the low thermal expansion coefficient of graphite enables the mold to maintain its shape and dimensions even at high temperatures.Isostatically Bearing Metal Casting Molds are particularly challenging to produce due to their complex geometry and tight tolerances. However, the use of High-Performance EDM Graphite Marble Mold has made this process much more manageable. The exceptional precision and accuracy of these molds make them ideal for producing isostatically bearing metal castings with a high degree of quality and consistency.The production of High-Performance EDM Graphite Marble Mold is a highly specialized process that requires expertise and experience. It involves the use of advanced equipment and techniques such as CAD modeling, CNC machining, and EDM. Therefore, it is essential to work with a reputable and experienced custom graphite molds manufacturer who can deliver high-quality molds tailored to your specific requirements.In conclusion, the development of High-Performance EDM Graphite Marble Mold has improved the quality and consistency of isostatically bearing metal casting molds. These molds offer exceptional precision, accuracy, and thermal conductivity, which are essential for producing high-quality metal castings. The use of isostatic graphite and EDM technology ensures that these molds are of the highest quality and can meet even the most demanding requirements of the industry. Therefore, the widespread adoption of High-Performance EDM Graphite Marble Mold is expected to significantly improve the efficiency and productivity of the metal casting industry.
Circular and Rectangular Graphite Crucibles for Rare-Earth Metallurgy and Chemical Industries
Graphite Crucibles: A Reliable Choice for Metallurgy and Chemical IndustriesGraphite crucibles are widely used in metallurgy and chemical industries for various reasons. They are known for their high-temperature resistance, good thermal conductivity, and corrosion resistance, making them ideal for applications that require extreme temperatures and harsh chemical environments. Graphite crucibles come in various shapes and sizes depending on their intended use, with circular and rectangular types being the most commonly used.Rare-earth MetallurgyIn rare-earth metallurgy, graphite crucibles are used for melting, casting, and smelting rare-earth metals due to their high-temperature resistance. Rare-earth metals are used in many industries, including aerospace, electronics, and medical devices. The demand for rare-earth metals has been on the rise in recent years, making their extraction, processing, and production more critical than ever.Graphite crucibles offer an ideal solution for the high-temperature requirements of rare-earth metallurgy, as regular crucibles would not be able to withstand the extreme temperatures required in the melting process. Graphite crucibles can withstand temperatures of up to 3000°C, making them perfect for melting difficult-to-process rare-earth metals such as neodymium, dysprosium, and europium.Load Plates for Anodes of Tantalum Electrolyzing CapacitorsGraphite crucibles are also used as load plates for the anodes of tantalum electrolyzing capacitors. Tantalum capacitors are an essential component in many electronic devices, including mobile phones, computers, and digital cameras. Graphite crucibles are used in the production of tantalum capacitors, in which they act as load plates, ensuring high-quality and reliable performance for the device.The use of graphite crucibles in the production of tantalum capacitors is due to their excellent electrical conductivity and resistance to chemical corrosion. Graphite also has high heat resistance, which ensures the capacitors can maintain performance even under extreme temperatures. Additionally, graphite is lightweight, making it easier to handle and transport in the production process.Corrosion Resistance in Chemical IndustriesIn chemical industries, graphite crucibles are commonly used due to their excellent resistance to chemical corrosion. Graphite crucibles are used in the manufacture of a wide range of chemical products, including acids, fertilizers, industrial chemicals, and pharmaceuticals, among others.The use of graphite crucibles in the chemical industry is due to their excellent chemical resistance, preventing chemical reactions between the crucible and the chemicals being processed. Additionally, graphite is compatible with various chemicals, ensuring no contamination occurs during the production process.ConclusionGraphite crucibles offer a reliable solution for various industries, from rare-earth metallurgy to chemical industries. The unique qualities of graphite, such as high-temperature resistance, good thermal conductivity, and corrosion resistance, make it an ideal choice for applications that require extreme temperatures and harsh chemical environments.With the increasing demand for rare-earth metals and electronic devices, the use of graphite crucibles will continue to play a significant role in the production of these products. Furthermore, the chemical industry will rely on graphite crucibles to ensure the production of high-quality chemical products. The use of graphite crucibles represents an investment in quality since it will help in producing high-quality products, ensuring customer satisfaction.About the company:name removed has been a leading supplier of quality graphite products for over 20 years. With extensive experience and expertise in the industry, they offer a wide range of graphite products, including crucibles, rods, plates, and blocks for various industrial applications. By maintaining high-quality standards and providing excellent customer service, name removed has become a trusted name in the graphite industry.
Revolutionizing the Graphite Industry: Unveiling the Power of Vibrated Graphite
Title: Groundbreaking Innovation in Graphite Materials Propels Renewable Energy TechnologiesIntroduction:In a major breakthrough for the renewable energy industry, researchers at an undisclosed company have developed Vibrated Graphite, a game-changing material that promises to revolutionize the efficiency and performance of numerous renewable energy technologies. Combining groundbreaking research and cutting-edge manufacturing techniques, the company stands at the forefront of developing advanced solutions for a sustainable future.Paragraph 1:Graphite has long been hailed as a key component in various renewable energy applications due to its excellent electrical conductivity, thermal stability, and corrosion resistance. However, the company's newly developed Vibrated Graphite takes these properties to unprecedented levels, marking a significant milestone in the industry. By combining their expertise in materials science and engineering, the company has been successful in fine-tuning the manufacturing process to deliver a product that surpasses conventional graphite in terms of performance and suitability for renewable energy technologies.Paragraph 2:One of the major applications where Vibrated Graphite is set to make a considerable impact is in lithium-ion batteries. The vast majority of electric vehicles (EVs) and grid-scale energy storage systems rely on these batteries, which are currently limited by the performance of the graphite anode. By incorporating Vibrated Graphite into battery anodes, the company aims to increase energy storage capacity, enhance charge-discharge rates, and prolong battery lifespan, ultimately driving the transition towards more sustainable transportation and grid systems.Paragraph 3:Moreover, Vibrated Graphite reveals exceptional potential in the field of solar energy. The material's unique properties allow for the efficient collection, transfer, and storage of solar-generated electricity. From solar panels and concentrated solar power systems to solar-powered devices, Vibrated Graphite has the ability to optimize energy conversion and improve overall system efficiency. This breakthrough holds immense promise in promoting the widespread adoption of renewable energy sources, fostering a greener and more sustainable world.Paragraph 4:Wind energy is another area where Vibrated Graphite could prove instrumental. Wind turbines, as vital components of wind energy generation, require lightweight and durable materials to withstand harsh environmental conditions while maximizing energy production. With its exceptional mechanical strength and thermal stability, Vibrated Graphite shows immense potential in the manufacturing of wind turbine blades, resulting in increased efficiency, reduced maintenance costs, and enhanced overall performance. This innovation paves the way for more reliable and cost-effective wind power solutions.Paragraph 5:In addition to its applications in specific renewable energy technologies, Vibrated Graphite can also benefit the broader energy industry. With the global emphasis shifting towards decarbonization and sustainability, energy infrastructure requires materials that can withstand higher temperatures and possess superior electrical and thermal conductivity. The company's Vibrated Graphite has the potential to replace conventional materials like copper and aluminum in various energy transmission and storage systems, significantly improving their efficiency and reducing environmental impact.Paragraph 6:The significance of Vibrated Graphite extends beyond the renewable energy sector. The material holds immense promise for advanced electronics, aerospace, and defense industries, where its exceptional properties can elevate the performance of electronic devices, aircraft components, and protect equipment. This versatility and potential for cross-industry applications further highlight the transformative impact of this innovative breakthrough.Conclusion:The development of Vibrated Graphite marks a pivotal moment in the evolution of renewable energy technologies. With its exceptional properties and wide-ranging applications, this revolutionary material has the potential to reshape the renewable energy landscape and propel us towards a cleaner, greener future. The company's commitment to sustainable innovation and dedication to pushing the boundaries of materials science have positioned them as a frontrunner in the renewable energy revolution.
What is Exothermic Welding and How Does it Work?
Exothermic Welding: A Revolutionary Technique for Efficient and Durable Electrical ConnectionsExothermic welding is a revolutionary technique for creating electrical connections that provide superior performance and durability compared to traditional methods. This process utilizes a high-heat principle that generates temperatures of over 3,000 degrees Celsius to melt metal powders and join conductors without the use of external heat or soldering.Exothermic welding, also known as hot melt welding, fire-clay welding, thermite welding and explosion welding, has been used for more than a century to create high-quality and long-lasting connections in a wide variety of applications, including railway signaling, telecommunications, power generation and distribution, aerospace, and marine industries.The principle behind exothermic welding is the redox reaction between metal oxides and metal powders, which produces a high-temperature exothermic reaction. The metal powders are usually made of copper oxide, aluminum, and iron oxide, while the metal conductors could be made of copper, brass, bronze, aluminum, or steel.During the exothermic welding process, the metal powders are placed in a mold or crucible along with the conductors to be joined. An ignition source or spark is applied to the metal powders, initiating the exothermic reaction that quickly melts the metal and fuses the conductors together. The resulting weld produces a metallurgical bond that is stronger and more reliable than mechanical or soldered connections.Exothermic welding offers several advantages over traditional methods, such as crimping, bolting, brazing, or soldering. Unlike mechanical connections that rely on contact pressure, exothermic welding produces a homogeneous connection that is free of voids, cracks, or corrosion. The weld is not affected by environmental factors such as moisture, dust, vibration, or temperature variations, ensuring long-term stability and low maintenance.Exothermic welding also provides superior electrical performance by reducing resistance and impedance. The weld has lower resistance than soldered or crimped connections, due to the absence of air gaps or contact resistance. The weld also has a low inductance, which is important for high-frequency applications or lightning protection.Moreover, exothermic welding is quick, easy, and safe to perform, even in hazardous or remote locations. The equipment required is portable and compact, consisting of a mold or crucible, a graphite mold, a spark gun, and a flux. The process can be done by a single operator, without the need for special skills or training. The setup time is minimal, and the welding time is typically less than a minute, depending on the size and type of conductors.Exothermic welding proves to be more economical than other methods when installed in a wiring system. Because it creates a permanent and reliable connection, it reduces or eliminates the need for rework, repairs, or replacements. The welded joint can withstand the same or higher level of current and fault conditions as the conductors, thus reducing the risk of downtime or failure. The life cycle cost of exothermic welding is lower than that of other methods due to the extended life of the connection.Exothermic welding has a wide range of applications in various industries, including grounding and bonding, lightning protection, rail bonding, power transmission, chemical processing, and pipeline integrity. It is particularly suited for critical systems that require high reliability and safety, such as nuclear power plants, hospitals, airports, and data centers.One company that offers high-quality exothermic welding products and services is (need remove brand name). With over 40 years of experience in the field, (need remove brand name) has developed a comprehensive range of exothermic welding kits, tools, and accessories that meet the needs of different industries and applications.The company's exothermic welding kits include everything needed for a successful connection, such as molds, metal powders, flux, igniters, and handles. The kits are available in various sizes and quantities, ranging from small repairs to large installations. The company also offers training and technical support to ensure the proper use and safety of the equipment.In conclusion, exothermic welding is a proven and reliable method for creating electrical connections that meet the highest standards of performance and durability. The technique's benefits include lower resistance, permanent bonding, high reliability, and reduced life cycle cost. (need remove brand name) provides a complete solution for exothermic welding that is easy to use, safe, and efficient, making it an excellent choice for any business or organization that requires high-quality electrical connections.