Sintered Ndfeb Mould Box: Latest News and Updates
By:Admin
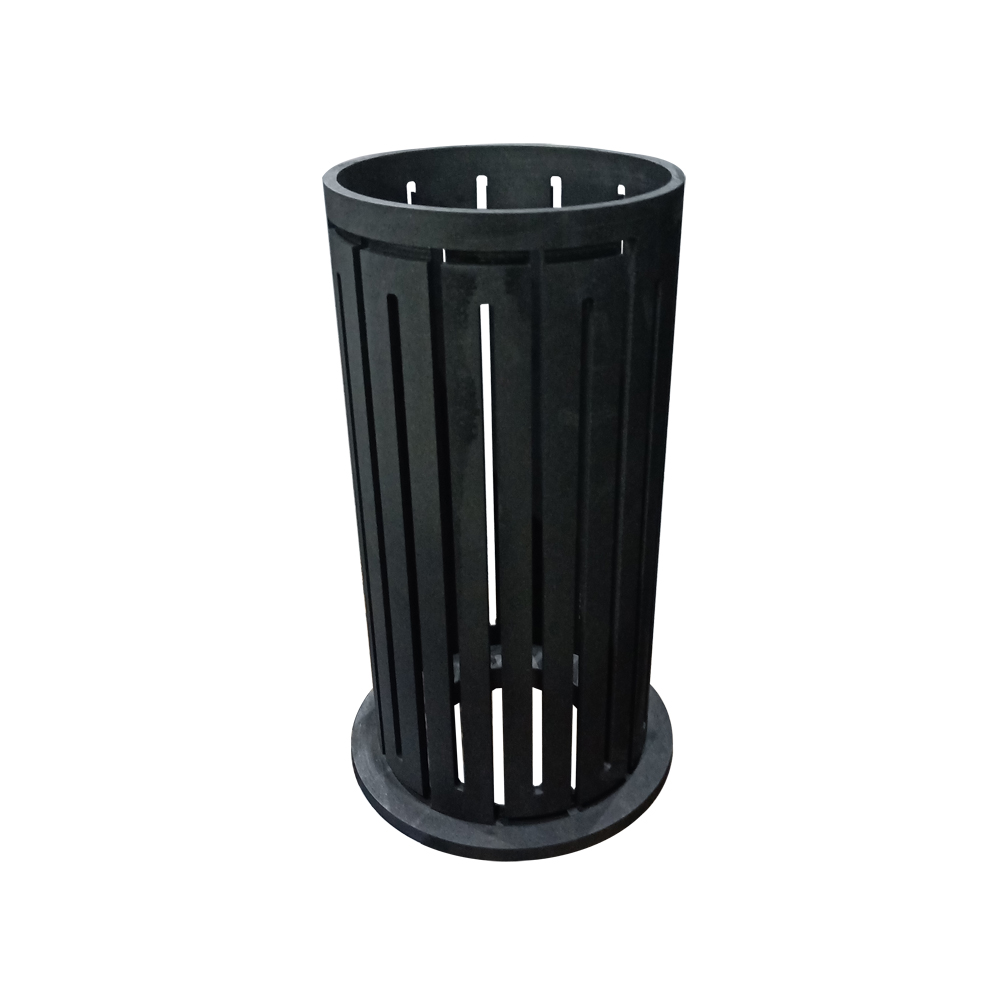
As technology continues to advance at an exponential rate, industries across the world are constantly looking for innovative solutions to improve productivity and efficiency. One such industry that has recently seen a major breakthrough is the manufacturing sector, with the introduction of the Ndfeb Sintered Mould Box. This revolutionary product has the potential to completely transform the way manufacturers approach the process of molding, setting a new standard for the industry as a whole.
The Ndfeb Sintered Mould Box is the brainchild of a leading manufacturing company, dedicated to pushing the boundaries of what is possible in the industry. Combining cutting-edge materials and design principles, this new product promises to deliver unprecedented performance and durability, ultimately benefiting manufacturers and their end customers.
One of the key features of the Ndfeb Sintered Mould Box is its use of Ndfeb sintered magnets, which are known for their exceptional strength and magnetic properties. By utilizing these magnets in the design of the mould box, the company has been able to create a product that offers superior magnetic force and resistance to demagnetization, ensuring consistent and reliable performance over time. This is a significant departure from traditional mould boxes, which often suffer from a loss of magnetism and therefore require frequent maintenance and replacement.
In addition to its enhanced magnetic properties, the Ndfeb Sintered Mould Box also boasts a unique design that promotes ease of use and flexibility. The box is meticulously engineered to provide a seamless and secure fit with the mould, eliminating the risk of slippage or misalignment during the molding process. This not only helps to improve the quality and accuracy of the final product, but also reduces the need for manual adjustments and corrections, saving valuable time and resources.
Furthermore, the Ndfeb Sintered Mould Box is constructed from high-quality materials that are capable of withstanding the rigors of the manufacturing environment. Its robust construction means that it can endure heavy use and exposure to extreme temperatures without compromising its performance, making it a reliable and long-lasting investment for manufacturers. This durability sets it apart from other mould boxes on the market, many of which are prone to damage and wear over time, leading to costly replacements and downtime.
The introduction of the Ndfeb Sintered Mould Box is a testament to the company's commitment to innovation and excellence. For years, the company has been a leading force in the manufacturing industry, constantly pushing the boundaries of what is achievable through the application of advanced materials and design concepts. The Ndfeb Sintered Mould Box represents the culmination of these efforts, offering manufacturers a game-changing solution that can significantly improve their operations and competitiveness.
As the manufacturing industry continues to evolve, it is clear that forward-thinking companies like this one will play a crucial role in driving progress and setting new standards for excellence. With the introduction of the Ndfeb Sintered Mould Box, manufacturers can now look forward to a future where the limitations of traditional mould boxes are a thing of the past, replaced by a new era of efficiency, reliability, and performance.
In conclusion, the Ndfeb Sintered Mould Box stands as a testament to the power of innovation and the potential for transformation within the manufacturing industry. Its unique combination of advanced materials, design principles, and engineering expertise has paved the way for a new standard in mould box technology, opening up exciting opportunities for manufacturers to elevate their capabilities and achieve unprecedented levels of productivity and quality.
The company's dedication to pushing the boundaries of what is possible in the industry will undoubtedly continue to drive progress and shape the future of manufacturing. With the Ndfeb Sintered Mould Box leading the charge, manufacturers can look forward to a new era of innovation and success.
Company News & Blog
Discover the Advantages of Carbon Graphite Plates: A Comprehensive Guide
Title: Carbon Graphite Plates: A Revolutionary Advancement in Industrial ApplicationsIntroduction:[Company name] is proud to introduce its pioneering line of Carbon Graphite Plates, which are set to revolutionize various industrial applications. With their exceptional strength, durability, and conductivity, these plates offer unparalleled performance, making them an ideal choice for a wide range of industries. This breakthrough innovation is expected to have a significant impact on the manufacturing sector, electrical engineering, aerospace, automotive, and other relevant industries.Body:1. Background and Significance:Carbon graphite plates are composite materials made from carbon fibers and a matrix material (typically resin). They exhibit superior properties, including high strength-to-weight ratio, resistance to chemicals and extreme temperatures, electrical conductivity, and low thermal expansion. These outstanding characteristics make carbon graphite plates highly coveted materials for industrial applications.2. Industrial Applications:Carbon graphite plates find extensive usage in various sectors, including:Automotive Industry:With the constant need to reduce vehicle weight and enhance fuel efficiency, carbon graphite plates are increasingly used in manufacturing lightweight components like chassis, body panels, and battery enclosures. The impressive strength and heat resistance of these plates ensure improved safety, sustainability, and overall performance in the automotive sector.Aerospace Industry:The aerospace industry demands materials that can withstand extreme conditions while providing reliability and efficiency. Carbon graphite plates are ideally suited for applications such as aircraft wings, fuselage structures, and rocket nozzle components. Their lightweight nature significantly reduces aircraft weight, leading to increased fuel efficiency and enhanced maneuverability.Electrical Engineering:Carbon graphite plates are excellent electrical conductors, making them ideal for manufacturing components such as current collectors, brushes, and commutators in electric motors and generators. These plates offer low resistance, optimal thermal conductivity, and outstanding resistance to wear, making them the preferred choice in electrical engineering applications.Manufacturing and Machinery:In the manufacturing and machinery sector, carbon graphite plates are utilized in fabricating heat shields, furnace parts, and other components that require resistance to extreme temperatures and harsh chemical environments. The plates' superior thermal stability and resistance to corrosion increase equipment longevity and improve operational efficiency.Renewable Energy Sector:Carbon graphite plates are instrumental in the renewable energy sector, contributing to the efficient generation and storage of clean energy. They are employed in the production of wind turbine blades, solar panel frames, and battery technologies, aiding in the transition towards a sustainable future.3. Advantages of Carbon Graphite Plates:- Lightweight: Carbon graphite plates offer a remarkable strength-to-weight ratio, making them significantly lighter than traditional metal alternatives. This characteristic improves fuel efficiency, reduces transportation costs, and enhances overall productivity.- High Strength: These plates possess exceptional mechanical strength, allowing them to withstand heavy loads and resist deformation, ensuring prolonged product lifespan.- Thermal Stability: Carbon graphite plates exhibit exceptional resistance to extreme temperatures, making them viable candidates for applications subjected to thermal cycling or in contact with high-temperature fluids.- Electrical Conductivity: The superior electrical conductivity of carbon graphite plates enables efficient energy transfer, reducing power losses and enhancing overall system performance.- Chemical Resistance: Carbon graphite plates are highly resistant to corrosive chemicals and environmental factors that can degrade conventional materials. This property ensures their longevity and reduces maintenance costs.Conclusion:The introduction of Carbon Graphite Plates by [Company name] signifies a significant breakthrough in industrial materials. With their remarkable strength, lightweight nature, and exceptional electrical and thermal conductivity, these plates offer unmatched performance across diverse applications. The widespread implementation of carbon graphite plates presents an opportunity for industries to enhance productivity, efficiency, and sustainability. As [Company name] continues to innovate in this field, the potential applications for carbon graphite plates are boundless, driving a revolution in industrial manufacturing and technology.
Top Suppliers of Graphite Products and Adhesives for Vacuum Furnaces
Graphite Products for Vacuum Furnace: The Ultimate GuideGraphite products help engineers and manufacturers optimize their application's performance in high-temperature environments, such as vacuum furnaces. Graphite is known for its exceptional thermal stability, thermal conductivity, and chemical inertness, which makes it the go-to material for many critical applications. In this blog post, we will explore the different types of graphite products for vacuum furnace and their benefits.Graphite Heating ElementsGraphite heating elements are primarily used to generate high temperatures inside the vacuum furnace. They consist of graphite rods or tubes that radiate heat when an electric current passes through them. Graphite heating elements are preferred over traditional heating elements because they offer fast heat-up and cool-down times, are energy-efficient, and reliable.Graphite CruciblesGraphite crucibles are ideal for melting and casting operations in vacuum furnaces. They are commonly used to melt metals, alloys, and other materials that require high temperatures and a non-reactive environment. Graphite crucibles are preferred over other materials because they can withstand extreme temperatures without deteriorating or reacting with the material being melted.Graphite InsulationGraphite insulation is used to maintain the high-temperature environment inside the vacuum furnace. It consists of graphite fibers in a high-temperature-resistant matrix. Graphite insulation is used as a liner inside the furnace walls to prevent heat loss and maintain a consistent temperature. It also helps to reduce energy consumption and improve furnace performance.Graphite FoilGraphite foil is a versatile material used in vacuum furnace applications, such as insulation, heating elements, and gaskets. It is a thin and flexible material made from high-purity graphite that is compressed and rolled into sheets. Graphite foil offers excellent thermal conductivity, chemical resistance, and mechanical properties, making it an ideal material for vacuum furnace applications.Graphite GasketsGraphite gaskets are used to seal various components inside the vacuum furnace, such as doors, lids, and flanges. They are preferred over other gasket materials because of their thermal stability, chemical resistance, and low outgassing properties. Graphite gaskets are also easy to install and remove, making them ideal for frequent maintenance.Graphite TubesGraphite tubes are commonly used as heating elements inside the vacuum furnace. They are made from high-purity graphite and can withstand extreme temperatures and corrosive environments. Graphite tubes are also used to transport corrosive gases and liquids in vacuum furnace applications.ConclusionGraphite products are essential components of vacuum furnace applications. They provide exceptional thermal stability, thermal conductivity, and chemical inertness, making them ideal for high-temperature environments. Graphite heating elements, crucibles, insulation, foil, gaskets, and tubes are just a few examples of the many types of graphite products available for vacuum furnace applications. Choosing the right graphite product for your specific application can help you optimize its performance and efficiency.
Expert Graphite and Carbon Services for Industrial Applications
Graphite Rotors and Shafts: The Ultimate Solution for Industrial ApplicationsGraphite rotors and shafts have been extensively used in industrial applications due to their exceptional physical and mechanical properties. From chemical processing to semiconductor manufacturing, graphite-based products have proven to be a reliable and cost-effective solution. These components are widely used in chemical pumps, mixers, compressors, and other equipment, where high-performance and corrosion-resistant materials are critical.Graphite is a naturally occurring crystalline form of carbon that exhibits unique properties such as high thermal conductivity, low coefficient of thermal expansion, high strength, and excellent chemical resistance. Graphite rotors and shafts are manufactured using high-purity graphite and are designed to withstand extreme operating conditions and aggressive chemical environments.Graphite rotors are an essential part of chemical pumps, which are used in various industries to transfer corrosive liquids. These rotors are typically used to pump fluids such as hydrochloric acid, sulfuric acid, and nitric acid, which can corrode and damage conventional pump components. By using graphite rotors, chemical pump manufacturers can improve equipment durability, reduce maintenance costs, and improve process efficiency.Moreover, graphite shafts are frequently used in the manufacturing of mixing equipment. These shafts are ideal for applications that require high torque, such as mixing viscous materials. Graphite shafts are highly durable, have low torsional deflection, and can withstand high temperatures. These properties make them ideal for use in chemical processing, food and beverage, pharmaceutical, and other industries.Graphite rotors and shafts are also utilized in the production of semiconductor components. The semiconductor manufacturing process is highly complex and requires precise and robust equipment to produce high-quality products. Graphite rotors and shafts are used in semiconductor manufacturing equipment to transfer and process corrosive chemicals and gases. These components provide superior corrosion resistance, improve process efficiency, and reduce equipment downtime.Choosing the Right Graphite Rotor and Shaft SupplierWhen selecting a supplier for graphite rotors and shafts, it’s crucial to find a company that provides high-quality products and exceptional service. The supplier should have experience in manufacturing graphite-based products and should use only the highest quality materials. Additionally, the supplier should have a skilled team of engineers to help customers customize components based on their specific needs.One such company is (removed brand name), which provides high-quality graphite rotors and shafts for various industrial applications. The company has an experienced team of engineers who can design and manufacture components based on customer requirements. They use only the highest quality graphite materials to ensure that their products meet the highest industry standards.Final ThoughtsIn conclusion, graphite rotors and shafts are essential components for a wide range of industrial applications. These components provide exceptional physical and mechanical properties, such as high-temperature resistance, chemical resistance, and low coefficient of thermal expansion. Selecting the right supplier for graphite rotors and shafts can make a significant difference in equipment durability, process efficiency, and overall production cost. By choosing a reliable supplier, businesses can ensure that their equipment operates efficiently and optimally.
Graphite Container for Hard Alloy: An Essential Tool for Industrial Applications
Graphite Container For Hard Alloy, a leading manufacturer in the field of graphite products, has introduced a new and innovative solution for the production of hard alloy tools. This breakthrough technology is set to revolutionize the hard alloy industry by providing a more efficient and cost-effective method for manufacturing high-quality tools.The company, which has been in operation for over 20 years, has a long-standing reputation for producing top-notch graphite products for various industries, including metallurgy, electronics, and chemicals. With their team of experienced engineers and state-of-the-art manufacturing facilities, Graphite Container For Hard Alloy has become a trusted partner for businesses in need of high-quality graphite products.The new graphite container for hard alloy is designed to address the challenges faced by manufacturers in producing hard alloy tools. Traditionally, the production process for hard alloy tools involves melting and sintering the raw materials in a graphite container. However, this method often results in high production costs and long processing times, making it inefficient for large-scale production.Recognizing the need for a more efficient solution, Graphite Container For Hard Alloy has developed a unique graphite container that offers superior thermal stability and resistance to chemical corrosion. This innovative design allows for faster and more uniform heating of the raw materials, resulting in shorter processing times and lower energy consumption.In addition to improving production efficiency, the new graphite container also delivers enhanced performance and durability for hard alloy tools. The high thermal stability of the graphite material ensures consistent processing temperatures, leading to improved material properties and higher tool quality. Furthermore, the container's resistance to chemical corrosion prevents contamination of the hard alloy, resulting in a longer lifespan for the tools."The introduction of our new graphite container for hard alloy is a game-changer for the industry," said the CEO of Graphite Container For Hard Alloy. "We have harnessed our expertise in graphite technology to develop a solution that not only improves production efficiency but also enhances the quality and durability of hard alloy tools. We are confident that this innovation will set new standards in the hard alloy industry and bring significant benefits to manufacturers."The launch of the new graphite container has already garnered significant interest from companies in the hard alloy industry. Several leading manufacturers have expressed their eagerness to adopt the new technology, citing its potential to streamline their production processes and improve the quality of their products. Graphite Container For Hard Alloy is currently in discussions with these companies to implement the new graphite container into their production lines.In conclusion, Graphite Container For Hard Alloy has once again demonstrated its commitment to innovation and excellence with the introduction of the new graphite container for hard alloy. This breakthrough technology is poised to transform the hard alloy industry by offering a more efficient, cost-effective, and high-quality solution for tool manufacturing. As the company continues to work closely with industry partners to implement the new technology, it is expected to bring significant advancements to the production of hard alloy tools.
High-Quality Graphite Crucible for Efficiently Melting Silver
Graphite Crucible For Melting Silver Offers Superior Quality for Precious Metal Applications[Company Name], a leading manufacturer of high-quality graphite products, is proud to announce the release of their specialized graphite crucible for melting silver. This new product is designed to meet the demanding needs of the precious metal industry and offers superior quality and performance.The graphite crucible is an essential tool for melting and casting silver and other precious metals. It is designed to withstand the high temperatures and harsh conditions of the melting process, making it an indispensable tool for any jewelry maker, metalworker, or industrial manufacturer.[Company Name] has utilized their extensive experience and expertise in graphite manufacturing to develop a crucible that is specifically tailored to the needs of melting silver. The crucible is made from high-quality graphite materials that are capable of withstanding temperatures of up to 3000°C, ensuring that it can handle the extreme heat generated during the silver melting process.One of the key features of the graphite crucible is its exceptional thermal conductivity. This allows for efficient heat transfer, ensuring uniform melting and casting of silver without the risk of hot spots or uneven temperature distribution. As a result, users can expect consistent and high-quality results with every use.In addition to its superior thermal conductivity, the graphite crucible also boasts excellent resistance to thermal shock and chemical corrosion. This makes it an extremely durable and long-lasting tool that can withstand the rigors of repeated use in industrial settings.The crucible is also designed with user convenience in mind. It features a smooth and polished interior surface to facilitate easy pouring and extraction of molten silver, as well as a secure and stable base to prevent tipping or spilling during the melting process. Furthermore, it is available in a range of sizes to accommodate different melting capacities and workflows.[Company Name] takes pride in offering high-quality products that meet the needs of their customers. Their graphite crucible for melting silver is no exception, as it has been rigorously tested and proven to deliver exceptional performance and reliability. With this new product, customers can expect to achieve precise and consistent results in their silver melting and casting operations.Whether used in jewelry making, metalworking, or industrial manufacturing, the graphite crucible for melting silver from [Company Name] is a valuable tool that can enhance the efficiency and quality of precious metal applications. Its superior quality, durability, and user-friendly design make it an ideal choice for professionals and hobbyists alike.In conclusion, [Company Name] continues to demonstrate their commitment to excellence with the release of their specialized graphite crucible for melting silver. This new product is a testament to their dedication to providing innovative and high-quality graphite solutions for a wide range of industrial applications. With its exceptional performance and reliability, the graphite crucible is set to become an indispensable tool for the precious metal industry.
Innovative Graphite Technology Revolutionizes Sintering Mould for Industry Applications
Graphite Sintering Moulds Revolutionize Manufacturing Processes(Graphite Company Name), a leading innovator in the field of advanced materials and manufacturer of cutting-edge graphite products, has recently introduced a groundbreaking new product - Graphite Sintering Moulds. These molds are set to revolutionize manufacturing processes across various industries, providing enhanced durability, heat resistance, and improved production efficiency.(Graphite Company Name) has been at the forefront of graphite-based innovations for over a decade, catering to the needs of industries such as automotive, aerospace, electronics, and more. With a dedicated research and development team, their focus has always been on developing advanced materials that push the boundaries of what is possible.The recently launched Graphite Sintering Moulds are the latest addition to (Graphite Company Name)'s extensive product portfolio. Traditionally, manufacturing processes involving high temperatures and pressure require molds that can withstand these extreme conditions. This is where Graphite Sintering Moulds come into play.One of the key advantages of these molds is their exceptional durability. Graphite, already known for its strength and resilience, has been further optimized in the development of these molds to withstand extreme heat conditions. This means that manufacturers can now produce high-quality, complex components without having to constantly worry about mold degradation due to high temperatures.Furthermore, the heat resistance of Graphite Sintering Moulds significantly reduces the cooling time required during the manufacturing process. The molds dissipate heat quickly and evenly, allowing for a rapid cooling process. This translates into increased production efficiency as manufacturers can achieve shorter cycle times, ultimately leading to higher productivity and reduced costs.In addition to their durability and heat resistance, these molds also offer excellent thermal conductivity. This unique property allows for more uniform heat distribution, resulting in consistent product quality and minimal defects. Manufacturers can rely on Graphite Sintering Moulds to deliver precise and reliable results, meeting the stringent requirements of various industries.Another notable advantage of Graphite Sintering Moulds is their versatility. These molds can be used in a wide range of manufacturing processes, including powder metallurgy, metal injection molding, and ceramic sintering. They have proven to be particularly effective in industries where the production of intricate and delicate components is required. The use of these molds enables precise replication of complex designs, ensuring consistent quality across batches.(Graphite Company Name)'s commitment to sustainability is also reflected in the development of these molds. Graphite is a naturally occurring mineral, and by utilizing it in manufacturing processes, the company minimizes the environmental impact associated with conventional mold materials. Additionally, the long lifespan of Graphite Sintering Moulds reduces the need for frequent replacements, further reducing waste generation.To cater to the diverse needs of their clients, (Graphite Company Name) offers customization options for their Graphite Sintering Moulds. The molds can be tailored to specific requirements, including sizes, shapes, and surface finishes. This flexibility allows manufacturers to optimize their production processes and achieve superior end-products.Overall, the introduction of Graphite Sintering Moulds represents a significant advancement in manufacturing technology. By providing exceptional durability, heat resistance, and thermal conductivity, these molds empower manufacturers to improve production efficiency and achieve consistent product quality. With their commitment to innovation and sustainability, (Graphite Company Name) continues to set new industry standards, driving progress and revolutionizing manufacturing processes across various sectors.
Durable Container for Hard Alloy: Innovative Solution for Storing Graphite Materials
Graphite Container for Hard Alloy Revolutionizes the Manufacturing Industry(Graphite Container for Hard Alloy) – In a groundbreaking development, a new innovative product, the Graphite Container for Hard Alloy, has been introduced by an industry-leading company. This game-changing technology is set to revolutionize the manufacturing industry by enhancing the production process of hard alloy materials.Hard alloys, also known as cemented carbides, are widely used in various industries due to their exceptional hardness, wear resistance, and strength. They are particularly prevalent in the automotive, aerospace, and tool manufacturing sectors. However, the conventional manufacturing process for hard alloys involves sintering, which involves compacting powdered metals at high temperatures and pressures. This process often leads to various challenges, such as deformation, cracks, and high scrap rates.The Graphite Container for Hard Alloy, developed by the pioneering company, aims to overcome these obstacles by providing a more efficient and cost-effective sintering solution. This advanced technology utilizes graphite, a material known for its high thermal conductivity and strength, as a container for the sintering process.By employing the Graphite Container for Hard Alloy, manufacturers can achieve greater control over the heat transfer during sintering. The unique properties of graphite allow for even distribution of heat, eliminating the risk of deformation and cracks in the hard alloy materials. This groundbreaking technology ensures consistent sintering quality, reducing scrap rates significantly.Moreover, the use of the Graphite Container for Hard Alloy offers several additional advantages. Firstly, the thermal conductivity of graphite allows for faster heat transfer, thereby reducing overall sintering time. This efficiency improvement translates into increased productivity and reduced production costs for manufacturers.Secondly, the graphite container boasts high chemical resistance, preventing any reaction between the container and the hard alloy material during the sintering process. This compatibility ensures the purity and integrity of the final product, enhancing its quality and performance.The Graphite Container for Hard Alloy is also highly durable and long-lasting. Its robust design enables it to withstand multiple sintering cycles without degradation or performance loss. This longevity contributes to the cost-effectiveness of the technology by reducing the need for frequent container replacements.In addition to these functional benefits, the implementation of the Graphite Container for Hard Alloy aligns with the growing focus on sustainability and eco-friendly manufacturing practices. This advanced technology reduces energy consumption and CO2 emissions since the shorter sintering time leads to lower energy requirements. Furthermore, the reduction in scrap rates minimizes material waste, contributing to a greener manufacturing process.The company behind this groundbreaking innovation, known for its commitment to research and development, has an established track record of delivering cutting-edge solutions to the manufacturing industry. With years of experience and expertise in the field of hard alloy production, they have successfully harnessed the potential of graphite to develop the Graphite Container for Hard Alloy.As this new technology gains traction in the manufacturing industry, it has the potential to revolutionize the way hard alloys are produced. The enhanced control over the sintering process, improved quality of the final product, increased productivity, and reduced environmental impact make the Graphite Container for Hard Alloy a game-changer in the industry.Manufacturers across various sectors will now have access to an innovative solution that addresses the challenges associated with traditional sintering methods. The introduction of this technology paves the way for more efficient, cost-effective, and sustainable production of hard alloy materials.In conclusion, the Graphite Container for Hard Alloy, developed by an industry-leading company, offers a revolutionary solution to the manufacturing industry. By harnessing the unique properties of graphite, this innovative technology enhances the sintering process, ensuring quality, efficiency, and sustainability. As manufacturers adopt this game-changing solution, they can look forward to improved production processes and enhanced hard alloy materials.
Unveiling the Power of Ignot Molds for Graphite Mold Formation
Graphite Ignite Mold Revolutionizing Casting IndustryThe ever-evolving world of manufacturing has seen significant advancements in recent years, one of which is the development of the revolutionary Graphite Ignot Mold. (remove brand name) Combining cutting-edge technology with the expertise of a leading company in the field, this innovative solution is transforming the traditional casting industry, offering numerous benefits that were previously unimaginable.Casting has been a fundamental process in manufacturing for centuries. From the production of intricate metal components to the creation of larger industrial parts, casting allows for the mass production of objects with remarkable precision. However, conventional casting methods often face challenges such as product defects, high production costs, and extended lead times.Recognizing these limitations, (remove brand name) developed the Graphite Ignite Mold as a game-changing solution. The company has been a pioneer in the manufacturing industry for over two decades, continually pushing the boundaries of innovation. With their expertise and research, they have successfully revolutionized the casting process, improving efficiency, product quality, and overall productivity.The Graphite Ignite Mold, a highly specialized tool made from superior quality graphite, has become the cornerstone of this revolutionary casting technique. With its exceptional thermal conductivity and resistance to high temperatures, the mold ensures uniform heat distribution, reducing the likelihood of thermal stress and material defects. Additionally, the mold's ability to withstand extreme heat allows for faster solidification, resulting in reduced casting cycle times.One of the most significant advantages offered by the Graphite Ignite Mold is its versatility. Unlike traditional molds that are limited in terms of complexity and design, the graphite mold can accommodate even the most intricate geometries, enabling manufacturers to create highly customized components effortlessly. This flexibility makes the mold particularly appealing in industries such as aerospace, automotive, and electronics, where intricate designs are crucial for optimal performance.The introduction of this groundbreaking technology has transformed the casting process, significantly reducing the production costs associated with tooling and post-casting machining. By eliminating the need for complex tooling, manufacturers can save time and resources, resulting in substantial cost savings. Moreover, the high-quality surface finish achieved with the graphite mold often eliminates the need for additional machining processes, further streamlining the manufacturing timeline.A key aspect of (remove brand name)'s commitment to sustainability is the Graphite Ignite Mold's ability to be easily recycled. Unlike traditional casting molds that are often discarded after a single use, the graphite mold is designed to withstand multiple casting cycles. Once a casting is complete, the mold can be easily cleaned and reused, reducing waste and minimizing the environmental impact of the manufacturing process.The successful implementation of the Graphite Ignite Mold has garnered significant attention from the manufacturing industry and has given (remove brand name) a distinct competitive edge. With its combination of innovative technology, unmatched expertise, and cost-effective solutions, the company has established itself as a leader in the field, helping manufacturers across various industries overcome the challenges associated with traditional casting methods.Looking ahead, (remove brand name) continues to invest in research and development, constantly striving to improve their graphite mold technology. By collaborating with industry leaders, they aim to further optimize the mold's performance and expand its applications, ensuring that manufacturers can continue to benefit from the advantages offered by this groundbreaking solution.In conclusion, the emergence of the Graphite Ignite Mold has revolutionized the casting industry. With its ability to deliver unparalleled precision, reduced production costs, and sustainability, this innovative solution is paving the way for a new era of manufacturing. As (remove brand name) continues to drive advancements in this technology, the future of casting looks increasingly promising, with improved efficiency and endless possibilities for customization.
How to Make Graphite Crucible: A Step-by-Step Guide
The demand for graphite crucibles is increasing in various industries such as metallurgy, jewelry making, and laboratory applications. Graphite crucibles are essential for the melting and refining of metals and alloys, as they can withstand high temperatures and are resistant to chemical erosion. To meet this growing demand, {Company Name} is expanding its production capacity and introducing innovative technologies to manufacture high-quality graphite crucibles.As a leading manufacturer of graphite products, {Company Name} has been providing reliable solutions for the metal casting and smelting industry for over a decade. The company has built a strong reputation for its commitment to quality, precision engineering, and exceptional customer service. With a state-of-the-art manufacturing facility and a team of experienced professionals, {Company Name} is well-positioned to deliver superior graphite crucibles that meet the exact requirements of its customers.The process of making graphite crucibles involves several intricate steps that require precision and expertise. First, the raw materials, including high-quality graphite powders and binders, are carefully selected and mixed in precise proportions to form a homogenous mixture. This mixture is then compacted and molded into the desired shape using advanced molding techniques. The formed crucibles are then subjected to a high-temperature baking process to carbonize the binder and enhance the strength and density of the crucible.In addition to traditional manufacturing methods, {Company Name} is leveraging advanced technologies such as computer-aided design (CAD) and computer numerical control (CNC) machining to enhance the quality and precision of its graphite crucibles. These technologies enable the company to produce crucibles with intricate designs and tight tolerances, ensuring consistent performance and reliability in demanding applications.With a strong focus on research and development, {Company Name} is constantly exploring new materials and manufacturing processes to further improve the performance of its graphite crucibles. The company has established collaboration with leading research institutions and industry experts to stay at the forefront of innovation and address the evolving needs of its customers. This proactive approach has enabled {Company Name} to introduce advanced graphite crucibles that offer exceptional thermal stability, resistance to thermal shock, and prolonged service life.In response to the increasing demand for graphite crucibles, {Company Name} is expanding its production capacity and optimizing its manufacturing processes to ensure timely delivery and cost-effective solutions for its customers. The company is also investing in training and skill development programs to empower its workforce with the knowledge and expertise required to produce high-quality graphite crucibles consistently.The graphite crucibles manufactured by {Company Name} are widely used in various applications, including the melting and casting of precious metals such as gold, silver, and platinum in jewelry making and refining processes. They are also utilized in the production of high-performance alloys and the analysis of metals in laboratory settings. {Company Name} offers a wide range of graphite crucibles in different sizes and configurations to cater to the diverse needs of its customers.In conclusion, {Company Name} is dedicated to meeting the growing demand for graphite crucibles by leveraging its expertise, advanced technologies, and commitment to quality. The company's ongoing investment in research and development, manufacturing capabilities, and customer-centric approach positions it as a trusted partner for industries that rely on high-performance graphite crucibles. With a focus on innovation and continuous improvement, {Company Name} is poised to drive further advancements in graphite crucible technology and contribute to the success of its customers.
Sintered Ndfeb Mould Box: Latest News and Updates
Ndfeb Sintered Mould Box Revolutionizes the IndustryAs technology continues to advance at an exponential rate, industries across the world are constantly looking for innovative solutions to improve productivity and efficiency. One such industry that has recently seen a major breakthrough is the manufacturing sector, with the introduction of the Ndfeb Sintered Mould Box. This revolutionary product has the potential to completely transform the way manufacturers approach the process of molding, setting a new standard for the industry as a whole.The Ndfeb Sintered Mould Box is the brainchild of a leading manufacturing company, dedicated to pushing the boundaries of what is possible in the industry. Combining cutting-edge materials and design principles, this new product promises to deliver unprecedented performance and durability, ultimately benefiting manufacturers and their end customers.One of the key features of the Ndfeb Sintered Mould Box is its use of Ndfeb sintered magnets, which are known for their exceptional strength and magnetic properties. By utilizing these magnets in the design of the mould box, the company has been able to create a product that offers superior magnetic force and resistance to demagnetization, ensuring consistent and reliable performance over time. This is a significant departure from traditional mould boxes, which often suffer from a loss of magnetism and therefore require frequent maintenance and replacement.In addition to its enhanced magnetic properties, the Ndfeb Sintered Mould Box also boasts a unique design that promotes ease of use and flexibility. The box is meticulously engineered to provide a seamless and secure fit with the mould, eliminating the risk of slippage or misalignment during the molding process. This not only helps to improve the quality and accuracy of the final product, but also reduces the need for manual adjustments and corrections, saving valuable time and resources.Furthermore, the Ndfeb Sintered Mould Box is constructed from high-quality materials that are capable of withstanding the rigors of the manufacturing environment. Its robust construction means that it can endure heavy use and exposure to extreme temperatures without compromising its performance, making it a reliable and long-lasting investment for manufacturers. This durability sets it apart from other mould boxes on the market, many of which are prone to damage and wear over time, leading to costly replacements and downtime.The introduction of the Ndfeb Sintered Mould Box is a testament to the company's commitment to innovation and excellence. For years, the company has been a leading force in the manufacturing industry, constantly pushing the boundaries of what is achievable through the application of advanced materials and design concepts. The Ndfeb Sintered Mould Box represents the culmination of these efforts, offering manufacturers a game-changing solution that can significantly improve their operations and competitiveness.As the manufacturing industry continues to evolve, it is clear that forward-thinking companies like this one will play a crucial role in driving progress and setting new standards for excellence. With the introduction of the Ndfeb Sintered Mould Box, manufacturers can now look forward to a future where the limitations of traditional mould boxes are a thing of the past, replaced by a new era of efficiency, reliability, and performance.In conclusion, the Ndfeb Sintered Mould Box stands as a testament to the power of innovation and the potential for transformation within the manufacturing industry. Its unique combination of advanced materials, design principles, and engineering expertise has paved the way for a new standard in mould box technology, opening up exciting opportunities for manufacturers to elevate their capabilities and achieve unprecedented levels of productivity and quality.The company's dedication to pushing the boundaries of what is possible in the industry will undoubtedly continue to drive progress and shape the future of manufacturing. With the Ndfeb Sintered Mould Box leading the charge, manufacturers can look forward to a new era of innovation and success.