Exploring the Applications and Advantages of Graphite Stirring Rods
By:Admin
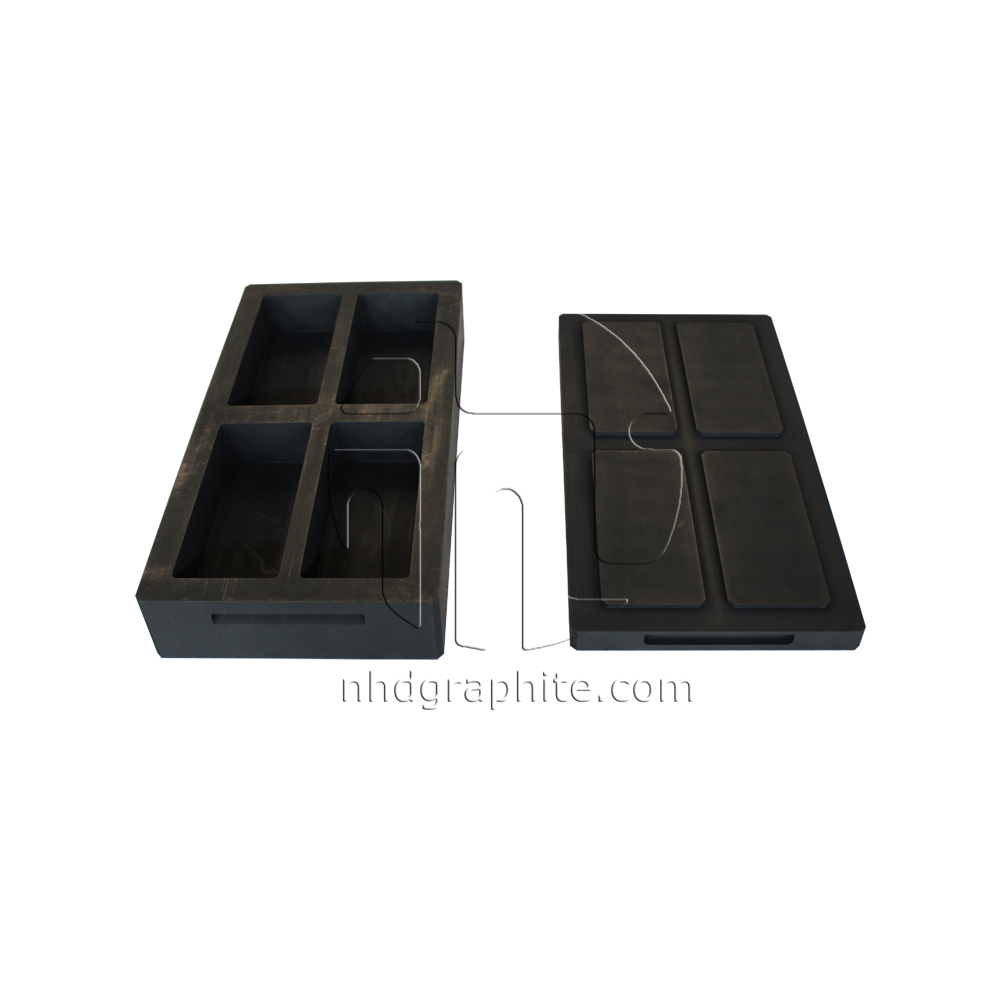
Innovative materials and tools are the backbone of technological advancements in various industries. One such breakthrough in the world of manufacturing and chemical processes is the Graphite Stirring Rod, a remarkable tool known for its superior performance. Deployed in diverse sectors, this tool is revolutionizing industrial processes, enabling companies to achieve higher efficiency, cost-effectiveness, and improved product quality. This article explores the limitless possibilities of this groundbreaking tool and the company behind its exceptional design and manufacturing.
Graphite, a form of carbon, possesses exceptional properties that make it an ideal material for a wide range of applications. Its high melting point, superior thermal and electrical conductivity, and excellent chemical resistance make it an invaluable resource for various industrial processes. The Graphite Stirring Rod harnesses these properties to overcome traditional limitations and provide unparalleled performance in mixing, blending, and stirring applications.
At the forefront of producing high-quality graphite stirring rods is a leading company that has pioneered the manufacture and development of advanced carbon-based products. With a legacy of excellence spanning several decades, their relentless pursuit of perfection and commitment to technological innovation have propelled them to the forefront of the industry.
The company's state-of-the-art manufacturing facilities are equipped with cutting-edge technologies, enabling the production of graphite stirring rods with unmatched precision, consistency, and reliability. Their team of experts, comprising engineers and materials scientists, continually work towards refining their manufacturing processes and leveraging the latest advancements in material science. This dedication to staying ahead of the technological curve ensures the delivery of top-of-the-line products that cater to the evolving needs of diverse industries.
The Graphite Stirring Rod, produced by this company, stands out due to its exceptional design and performance-enhancing features. Its unique composition and surface properties allow for efficient mixing and stirring of various substances, including liquids, powders, and viscoelastic materials. With its exceptional heat resistance and minimal reaction tendencies, the rod ensures the complete eradication of impurities while preventing product contamination, making it an indispensable tool in critical industries such as pharmaceuticals and food processing.
The versatility of the Graphite Stirring Rod extends beyond its unrivaled performance in mixing and stirring applications. Its robustness and durability enable its usage in extreme environments and aggressive chemical processes. The rod's high thermal conductivity ensures efficient heat transfer, facilitating temperature control during reactions. Additionally, its electrical conductivity makes it suitable for applications requiring grounding or electrochemical reactions, thus amplifying its range of applications across various industries.
In an era driven by sustainability and energy efficiency, the Graphite Stirring Rod possesses several environmentally-friendly attributes. The rod's long lifespan and resistance to corrosion and degradation significantly reduce waste generation and maintenance costs. Furthermore, the manufacturing process prioritizes eco-friendly practices, minimizing carbon footprint and promoting responsible consumption.
The applications of the Graphite Stirring Rod span across multiple industries, including pharmaceuticals, chemicals, food processing, research laboratories, and energy production. In the pharmaceutical sector, this tool ensures the homogeneity of drug formulations, leading to increased efficacy and patient safety. In chemical processes, it aids in achieving uniformity and facilitating reactions, resulting in improved product quality and reduced waste. The food processing industry benefits from this tool's hygienic properties, assuring contamination-free production processes.
In conclusion, the revolutionary Graphite Stirring Rod, manufactured by the leading carbon-based products company, has transformed industrial processes across various sectors. With its unparalleled performance, durability, and environmentally-friendly attributes, this exceptional tool exemplifies the potential of innovative materials in advancing technological capabilities. As this tool continues to redefine industry standards, companies across the globe are poised to benefit from its exceptional performance and optimized processes.
Company News & Blog
Discover the Essential Functions and Applications of a Rotary Kiln
Title: Revolutionary Rotary Kiln Technology Poised to Transform the IndustryIntroduction:In a world constantly seeking more sustainable alternatives, the renowned engineering company {} is set to revolutionize the industry with their groundbreaking rotary kiln technology. Offering a comprehensive solution to address the challenges of traditional processes, their innovative rotary kiln design aims to significantly reduce carbon emissions, improve energy efficiency, and enhance the long-term sustainability of production across various sectors.Body:1. The Need for Innovations in Rotary Kiln Technology (150 words):The conventional rotary kiln has been widely used in industries like cement, minerals, and chemicals, among others, for decades. However, it inherently suffers from several shortcomings, including high energy consumption, significant greenhouse gas emissions, and limited operational flexibility. As the world increasingly prioritizes eco-friendliness and sustainability, there has been a growing demand for advanced technologies that can mitigate the environmental impact of manufacturing processes.2. Introducing the Revolutionary {} Rotary Kiln (150 words):{} has heeded this call for change by developing an exceptional rotary kiln technology that promises to reshape the industry. By incorporating cutting-edge engineering principles, this innovative design optimizes energy efficiency while drastically reducing carbon emissions. Transforming the conventional rotary kiln into an advanced and sustainable solution, the new design enables production plants to meet strict environmental regulations, achieve substantial cost savings, and enhance operational flexibility.3. Key Features and Benefits (200 words):The updated rotary kiln design integrates several game-changing features, elevating its performance and sustainability. A few significant highlights include:a. Enhanced Energy Efficiency: The {} rotary kiln utilizes advanced heat recovery systems and optimized insulation techniques, significantly improving thermal efficiency and reducing energy consumption. This leads to substantial cost savings and a more sustainable manufacturing process.b. Reduced Carbon Footprint: By effectively capturing and neutralizing harmful greenhouse gas emissions, the new rotary kiln technology helps industries make substantial progress towards achieving their carbon reduction goals. The design minimizes toxic pollutant discharge into the atmosphere, ensuring compliance with stringent environmental regulations.c. Operational Flexibility: {} rotary kiln technology offers remarkable flexibility, allowing for the processing of a wide range of materials, including cement, minerals, and even industrial waste. This versatility enables production plants to adapt quickly to changing market demands, minimizing downtime and maximizing operational efficiency.d. Enhanced Safety Features: The new rotary kiln design incorporates state-of-the-art safety measures, ensuring the well-being of workers while minimizing the risk of accidents or incidents during operation.4. Applications and Potential Impact (200 words):The profound impact of the revolutionary {} rotary kiln technology extends to a myriad of industries. Cement manufacturers can vastly reduce their carbon footprint and energy costs, while simultaneously increasing cement production capacity. Furthermore, the mineral processing industry can achieve greater efficiency and cost-effectiveness in extracting valuable minerals.Additionally, the steel industry can leverage this technology to improve energy efficiency and decrease carbon emissions in the production of iron ore pellets. Other potential applications include the treatment of hazardous waste and the production of alternative fuels from biomass and municipal solid waste, fostering a circular economy.5. Collaboration and Future Outlook (100 words):{} is actively seeking collaborative partnerships with industry leaders to further refine and implement their cutting-edge rotary kiln technology. By combining their technical expertise with the industry's demands, {} aims to continuously enhance their innovative solution and drive sustainability across various sectors globally.Conclusion:With the introduction of their revolutionary rotary kiln technology, {} has opened up a new era for the industry, providing a transformative approach to energy efficiency, reduced carbon emissions, and enhanced operational flexibility. As industries rapidly transition towards sustainability, this innovation stands poised to become the go-to solution, ensuring a greener and more efficient manufacturing landscape for generations to come.
Top Graphite Rod Manufacturers and Suppliers in China - Mutual Benefits Await Overseas Customers
Graphite is one of the most commonly used materials in industries such as aerospace, automotive, and manufacturing. One of its unique properties is that it is a good conductor of electricity, making it ideal for use in products that require the transfer of electrical current. Graphite rods are a type of graphite product that is used in various applications.A graphite rod is a cylindrical bar made from a specific grade of graphite that is processed and machined to meet specific requirements. The rods are available in different diameters, lengths, and shapes. They are usually manufactured using high-purity graphite, which helps to improve their mechanical properties. Graphite rods are suitable for use in high-temperature, high-pressure, and corrosive environments.Teflon graphite rods are a type of graphite rod that is coated with Teflon, a fluoropolymer that is widely used in industries such as cooking, textiles, and aerospace. The Teflon coating helps to improve the overall characteristics of the graphite rod. Teflon graphite rods can withstand high temperatures and pressures, making them ideal for use in applications such as sealing systems, bearings, and gaskets.The use of Teflon graphite rods can help to reduce friction in machines and equipment, thereby improving their efficiency and performance. The Teflon coating can also help to protect the graphite rod from corrosion and chemical attack, thereby increasing its lifespan.Graphite rods are essential components in many industries, and their importance cannot be overstated. They are used in various applications such as nuclear reactors, aerospace, and automotive industries. Graphite rods have excellent thermal and electrical conductivity, which makes them ideal for use in products that require the transfer of electrical or thermal energy.In conclusion, Teflon graphite rods are a type of graphite rod that has been coated with Teflon. They are widely used in industrial applications where high temperatures and pressures are involved. The Teflon coating helps to improve the overall performance and lifespan of the graphite rod. Graphite rods, in general, are essential components in many industries, and their applications are limitless. They are an excellent choice for industry professionals who seek products with high thermal and electrical conductivity.
1 oz Hexagon High Density Graphite Mold for Making Loaf Bars - Ideal for Silver or Gold Ingot Casting
Make Your Own Gold Bars Launches New Gold and Silver Mold for Investment EnthusiastsMake Your Own Gold Bars, a leading manufacturer and supplier of gold and silver casting products, has launched a new gold and silver mold for investment enthusiasts. The Gold Hexagon High Density Graphite Mold is designed to help investors create their own unique gold and silver bars with ease.The Gold Hexagon High Density Graphite Mold allows investors to create 1-ounce gold hexagon bars and 1/2-ounce silver ingots with a perfect fit. The inside size of the mold is approximately 11/16 across and 1/4 deep. The mold is machined graphite ingot with a slight wall taper for better metal removal and accuracy. This Mold is great for making old-style loaf bars.The Gold Hexagon High Density Graphite Mold is easy to use. The investor can fill the mold with melted gold or silver, let it cool and then remove the finished product. The weight of each bar depends on the metal being used and how full the cavity is. Filling it to the top will give the investor a perfect bar that is the exact weight they desire.Make Your Own Gold Bars is a leading manufacturer and supplier of gold and silver casting products. The company offers a wide range of products, including molds, crucibles, tongs, and other casting tools. The company was founded by Martin Hannon in 2008. He started the company because he wanted to help people with the process of making their own gold and silver bars.We are excited to launch our new Gold Hexagon High Density Graphite Mold, said Martin Hannon, founder of Make Your Own Gold Bars. This product is perfect for investment enthusiasts who want to create their own gold and silver bars. We have designed this mold to be easy to use and to produce perfect bars every time. We are committed to providing our customers with the best possible products and services, and this new mold is an important addition to our product line.Make Your Own Gold Bars has been serving the investment community for over a decade. The company offers a wide range of products to help investors make their own gold and silver bars with ease. The company's products are designed to be user-friendly and provide investors with the best possible results. These products are perfect for anyone who wants to invest in gold and silver without the high costs associated with buying finished products.In addition to selling gold and silver casting products, Make Your Own Gold Bars also offers advice and guidance to customers who are new to investing in precious metals. The company offers tips on the best ways to store gold and silver, as well as advice on how to get started with investing in precious metals. The company has also developed a reputation for providing excellent customer service, which has helped it to build a loyal customer base.Make Your Own Gold Bars is committed to providing its customers with high-quality products and excellent service. The company's products are designed to help investors create their own unique gold and silver bars with ease. The Gold Hexagon High Density Graphite Mold is the perfect addition to the company's product line, and it is sure to be popular among investment enthusiasts.Investing in gold and silver is a great way to diversify your portfolio and protect your wealth. With Make Your Own Gold Bars, investors can create their own gold and silver bars with ease. The Gold Hexagon High Density Graphite Mold is just one of the many products offered by the company, which is sure to help investors achieve their investment goals. Make Your Own Gold Bars is the go-to destination for anyone who wants to invest in gold and silver.
Cutting Disk Manufacturing Advances: Hot-Pressing Graphite Die Process Unveiled
Title: Advancements in Hot-Pressing Graphite Die for Cutting Disk Propels Manufacturing Industry Efficiency and SustainabilityIntroduction:[Company Name], a global leader in innovative manufacturing solutions, has recently introduced an advanced hot-pressing graphite die for cutting disks. With increasing demand for high-performing cutting tools in various industries, this cutting-edge technology is set to revolutionize the manufacturing sector by enhancing efficiency, precision, and sustainability in the production process.Defining the Hot-Pressing Graphite Die:Hot-pressing graphite die technology involves subjecting graphite powders to intense heat and pressure to create molds with exceptional strength and durability. It enables the production of cutting disks with superior hardness, wear resistance, and thermal stability, leading to extended tool life and improved performance.Enhanced Efficiency:By utilizing hot-pressing graphite dies, manufacturers can achieve significant improvements in efficiency. The ability to produce complex cutting disk designs accurately and consistently enables streamlined manufacturing processes, reducing downtime and increasing productivity. The high thermal conductivity of graphite dies also ensures effective heat dissipation during production, preventing overheating and maintaining product quality.Additionally, the exceptional machinability of graphite enables faster production cycles, allowing manufacturers to meet tight deadlines and respond to market demands promptly. This increased efficiency translates into cost savings and a competitive edge for companies operating in the manufacturing industry.Precision and Quality Advancements:The hot-pressing graphite die technology also brings unprecedented precision and quality to the production of cutting disks. Through the use of advanced computer-controlled systems, manufacturers can achieve micron-level accuracy and consistency in the die-casting process. This precision guarantees the quality and uniformity of each cutting disk produced, driving customer satisfaction and reliability.Moreover, the improved hardness and wear resistance of cutting disks created using hot-pressing graphite dies ensure longer tool life. This reduction in tool breakdown and replacement not only saves manufacturers substantial costs but also contributes to a more sustainable manufacturing process by reducing material waste, energy consumption, and carbon footprint.Sustainable Manufacturing Solutions:Addressing the growing concern for environmental sustainability, hot-pressing graphite die technology promotes a greener manufacturing industry. The use of graphite, a naturally occurring and recyclable material, significantly reduces the reliance on non-renewable resources. Additionally, the energy-efficient hot-pressing process minimizes carbon emissions and waste generation.By incorporating this innovative technology into their production processes, manufacturers can align their operations with global sustainability goals, enhance their brand image, and attract environmentally conscious consumers.Market Outlook and Conclusion:The introduction of the hot-pressing graphite die for cutting disks marks a significant milestone in the manufacturing industry. Its ability to enhance efficiency, precision, and sustainability paves the way for improved manufacturing processes and promotes the development of high-performing cutting tools.With rising global demand for cutting disks in industries such as automotive, aerospace, and construction, manufacturers equipped with this advanced technology are well-positioned to capitalize on the market opportunities. Increased production efficiency, superior product quality, and sustainable practices will be the key differentiators that drive success in a rapidly evolving manufacturing landscape.As companies like [Company Name] continue to push the boundaries of technological innovation, it is expected that hot-pressing graphite die technology will become an industry standard, revolutionizing manufacturing processes and contributing to a more sustainable future.
Top-quality Isostatic Metal Casting Molds for High-performance EDM Graphite Marble Mold
High Performance EDM Graphite Marble Mold: A Boon for Isostatically Bearing Metal Casting MoldsMetal casting is one of the most widely used techniques employed for producing various metal products. It involves pouring molten metal into a mold and allowing it to solidify into the desired shape. However, this process is not as simple as it sounds. The metal has to be cast with precision to ensure that the final product meets the desired specifications. One way to ensure this is by using high-quality graphite molds. Graphite molds are extensively used in the metal casting industry due to their exceptional properties such as high thermal conductivity, excellent machinability, and low thermal expansion coefficient. The recent development of High-Performance EDM Graphite Marble Mold has revolutionized the industry.High-Performance EDM Graphite Marble Mold is one of the most advanced forms of graphite molds available today. This type of mold is made using high-quality isostatic graphite, which is a versatile and durable material. It is ideally suited for producing intricate and complex metal castings. The use of isostatic graphite ensures that the molds are free from any internal defects or cracks, which can affect the quality of the final product.The High-Performance EDM Graphite Marble Mold also employs the technique of Electrical Discharge Machining (EDM) to produce a precise and accurate mold. EDM is an advanced machining process in which electrical discharges are used to shape the material. It is an effective process for producing complex shapes with very high accuracy. The use of EDM in graphite mold production ensures that the molds are of the highest quality and precision.One of the key advantages of using High-Performance EDM Graphite Marble Mold is its exceptional thermal conductivity. Graphite has one of the highest thermal conductivity rates of any material. This allows the mold to quickly heat up and cool down, which is essential for producing metal castings with a high degree of accuracy. Moreover, the low thermal expansion coefficient of graphite enables the mold to maintain its shape and dimensions even at high temperatures.Isostatically Bearing Metal Casting Molds are particularly challenging to produce due to their complex geometry and tight tolerances. However, the use of High-Performance EDM Graphite Marble Mold has made this process much more manageable. The exceptional precision and accuracy of these molds make them ideal for producing isostatically bearing metal castings with a high degree of quality and consistency.The production of High-Performance EDM Graphite Marble Mold is a highly specialized process that requires expertise and experience. It involves the use of advanced equipment and techniques such as CAD modeling, CNC machining, and EDM. Therefore, it is essential to work with a reputable and experienced custom graphite molds manufacturer who can deliver high-quality molds tailored to your specific requirements.In conclusion, the development of High-Performance EDM Graphite Marble Mold has improved the quality and consistency of isostatically bearing metal casting molds. These molds offer exceptional precision, accuracy, and thermal conductivity, which are essential for producing high-quality metal castings. The use of isostatic graphite and EDM technology ensures that these molds are of the highest quality and can meet even the most demanding requirements of the industry. Therefore, the widespread adoption of High-Performance EDM Graphite Marble Mold is expected to significantly improve the efficiency and productivity of the metal casting industry.
Discover the Benefits and Applications of Graphite Sintering Moulds
Title: Groundbreaking Graphite Sintering Mould Innovates Industrial ManufacturingIntroduction:In a significant stride towards revolutionizing industrial manufacturing processes, a cutting-edge technology has emerged - the Graphite Sintering Mould, created by an innovative company. This groundbreaking advancement holds the potential to transform various industries by providing more efficient and cost-effective solutions for producing high-quality goods. By combining the advantages of graphite as a material with ingenious mold designs, this pioneering technology is set to redefine the future of manufacturing.(Graphite Sintering Mould) – A Game-Changing Technology:(Graphite Sintering Mould) is an advanced manufacturing tool that utilizes graphite as the primary material in its mold construction. Graphite, renowned for its exceptional properties such as high thermal conductivity, low thermal expansion, and resistance to chemical corrosion, proves to be an ideal material for creating molds. The unique combination of these characteristics sets the stage for accelerating the industrial manufacturing process.(Graphite Sintering Mould) excels in a wide range of applications, including automotive, aerospace, electronics, and more. Traditionally, manufacturing processes involve the use of metal molds, which are expensive, time-consuming to produce, and have limited lifespans. However, Graphite Sintering Mould overcomes these limitations by offering unparalleled advantages.Elevating Manufacturing Efficiency:An essential aspect of (Graphite Sintering Mould) is its distinctive mold design, tailored to specific production requirements. This technology enables the production of molds with intricate shapes, precise dimensions, and excellent heat transfer capabilities. Compared to traditional molds, the use of Graphite Sintering Mould significantly reduces the cycle time, resulting in increased production efficiency and cost savings.(Graphite Sintering Mould) molds possess superior thermal conductivity, ensuring uniform heat distribution during the manufacturing process. This feature eliminates hotspots and minimizes thermal stress, thereby enhancing the overall quality and consistency of the finished products. Manufacturers can now achieve higher precision, reduced waste, and greater control over the manufacturing process, resulting in enhanced customer satisfaction.Environmental-Friendly and Cost-Effective Solution:(Graphite Sintering Mould) also offers environmental advantages by minimizing energy consumption and material waste. The high thermal conductivity of graphite enables faster heating and cooling cycles, reducing power requirements and improving energy efficiency. Additionally, the durability and longevity of (Graphite Sintering Mould) molds enable companies to produce a significantly larger number of items, thus reducing the need for frequent mold replacements.Moreover, the reduced production time and enhanced efficiency provided by (Graphite Sintering Mould) molds translate into significant cost savings for manufacturers. Companies can allocate their resources more strategically, invest in research and development, and explore new market opportunities.Emerging as a Pioneer in Industrial Manufacturing:The company behind the development of (Graphite Sintering Mould) stands at the forefront of innovation in the industrial manufacturing sector. Through extensive research and development, the company has successfully harnessed the unique properties of graphite and perfected the technology to produce reliable, high-performance molds.The exceptional quality of molds generated using (Graphite Sintering Mould) has garnered attention from major industries worldwide. Their commitment to sustainable practices alongside their relentless pursuit of excellence positions the company as a leading pioneer in the manufacturing field.Looking Forward:The introduction of (Graphite Sintering Mould) marks a significant milestone in the evolution of industrial manufacturing. With its ability to enhance production efficiency, reduce costs, and deliver superior quality products, this technology holds vast potential for various sectors. Manufacturers across the globe are eagerly adopting this groundbreaking method, propelling the industry toward a more sustainable and efficient future.As researchers continue to refine and expand the capabilities of (Graphite Sintering Mould), we can anticipate further advancements that will revolutionize the way products are manufactured. With improved mold designs, expanded applications, and increased efficiency, the possibilities for innovation with this game-changing technology are limitless.
Discover the Advantages of Carbon Graphite Plates: A Comprehensive Guide
Title: Carbon Graphite Plates: A Revolutionary Advancement in Industrial ApplicationsIntroduction:[Company name] is proud to introduce its pioneering line of Carbon Graphite Plates, which are set to revolutionize various industrial applications. With their exceptional strength, durability, and conductivity, these plates offer unparalleled performance, making them an ideal choice for a wide range of industries. This breakthrough innovation is expected to have a significant impact on the manufacturing sector, electrical engineering, aerospace, automotive, and other relevant industries.Body:1. Background and Significance:Carbon graphite plates are composite materials made from carbon fibers and a matrix material (typically resin). They exhibit superior properties, including high strength-to-weight ratio, resistance to chemicals and extreme temperatures, electrical conductivity, and low thermal expansion. These outstanding characteristics make carbon graphite plates highly coveted materials for industrial applications.2. Industrial Applications:Carbon graphite plates find extensive usage in various sectors, including:Automotive Industry:With the constant need to reduce vehicle weight and enhance fuel efficiency, carbon graphite plates are increasingly used in manufacturing lightweight components like chassis, body panels, and battery enclosures. The impressive strength and heat resistance of these plates ensure improved safety, sustainability, and overall performance in the automotive sector.Aerospace Industry:The aerospace industry demands materials that can withstand extreme conditions while providing reliability and efficiency. Carbon graphite plates are ideally suited for applications such as aircraft wings, fuselage structures, and rocket nozzle components. Their lightweight nature significantly reduces aircraft weight, leading to increased fuel efficiency and enhanced maneuverability.Electrical Engineering:Carbon graphite plates are excellent electrical conductors, making them ideal for manufacturing components such as current collectors, brushes, and commutators in electric motors and generators. These plates offer low resistance, optimal thermal conductivity, and outstanding resistance to wear, making them the preferred choice in electrical engineering applications.Manufacturing and Machinery:In the manufacturing and machinery sector, carbon graphite plates are utilized in fabricating heat shields, furnace parts, and other components that require resistance to extreme temperatures and harsh chemical environments. The plates' superior thermal stability and resistance to corrosion increase equipment longevity and improve operational efficiency.Renewable Energy Sector:Carbon graphite plates are instrumental in the renewable energy sector, contributing to the efficient generation and storage of clean energy. They are employed in the production of wind turbine blades, solar panel frames, and battery technologies, aiding in the transition towards a sustainable future.3. Advantages of Carbon Graphite Plates:- Lightweight: Carbon graphite plates offer a remarkable strength-to-weight ratio, making them significantly lighter than traditional metal alternatives. This characteristic improves fuel efficiency, reduces transportation costs, and enhances overall productivity.- High Strength: These plates possess exceptional mechanical strength, allowing them to withstand heavy loads and resist deformation, ensuring prolonged product lifespan.- Thermal Stability: Carbon graphite plates exhibit exceptional resistance to extreme temperatures, making them viable candidates for applications subjected to thermal cycling or in contact with high-temperature fluids.- Electrical Conductivity: The superior electrical conductivity of carbon graphite plates enables efficient energy transfer, reducing power losses and enhancing overall system performance.- Chemical Resistance: Carbon graphite plates are highly resistant to corrosive chemicals and environmental factors that can degrade conventional materials. This property ensures their longevity and reduces maintenance costs.Conclusion:The introduction of Carbon Graphite Plates by [Company name] signifies a significant breakthrough in industrial materials. With their remarkable strength, lightweight nature, and exceptional electrical and thermal conductivity, these plates offer unmatched performance across diverse applications. The widespread implementation of carbon graphite plates presents an opportunity for industries to enhance productivity, efficiency, and sustainability. As [Company name] continues to innovate in this field, the potential applications for carbon graphite plates are boundless, driving a revolution in industrial manufacturing and technology.
Durable Graphite Boat for Square Applications Rises in Popularity: Market Insights and Analysis
Title: High-Quality Graphite Boat Facilitates Diverse Industrial ApplicationsIntroduction:Graphite, a versatile and durable material known for its excellent thermal and electrical conductivity, has taken center stage in various industrial applications. Amongst the leaders in graphite manufacturing, a renowned company has recently unveiled their cutting-edge Square Graphite Boat - a breakthrough product that is revolutionizing multiple industries. With a commitment to innovation and an unwavering focus on quality, this new graphite boat is set to address the needs of diverse sectors and contribute to their growth. 1. The Versatility of Graphite:Graphite, an allotrope of carbon, is highly valued for its unique properties, making it indispensable in numerous industries. It is widely used in manufacturing electrical products, semiconductors, batteries, fuel cells, and even in the aerospace industry due to its lightweight nature. The thermal stability and corrosion resistance of graphite also make it an ideal material for use in high-temperature furnaces, crucibles, and electrodes. Recognizing the potential of graphite, this pioneering company has introduced the Square Graphite Boat to enhance industrial processes across sectors.2. The Key Features of Square Graphite Boat:The Square Graphite Boat boasts several noteworthy features, making it stand out in the market. First and foremost, its impeccable design ensures uniform heat distribution, reducing the possibility of thermal stress cracks during high-temperature applications. The boat's superior thermal conductivity guarantees efficient heat transfer, resulting in enhanced productivity and reduced energy consumption. Furthermore, the boat's high-density graphite composition coupled with its exceptional machinability allows for intricate and precise customization, catering to the unique requirements of different industrial applications.3. Revolutionary Applications of Square Graphite Boat:(a) Semiconductor Manufacturing Sector:In the semiconductor industry, where precision and reliability are paramount, the high-purity graphite material of the Square Graphite Boat proves to be indispensable. Used as a critical component in thermal processes, this boat ensures optimal heat distribution, preventing defects in the delicate semiconductor wafers. The boat's longevity and resistance to chemical reactions make it a sustainable and cost-effective solution.(b) Energy Storage and Microelectronics Industry:With the rapid advancement in the development of energy storage devices such as lithium-ion batteries and fuel cells, the demand for quality graphite boats has surged. The Square Graphite Boat, with its excellent electrical conductivity, corrosion resistance, and uniform heat distribution, ensures the efficient functioning and extended lifespan of these energy storage devices, consequently benefiting the electric vehicle and renewable energy sectors.(c) Metallurgical and Chemical Industries:Graphite boats find their application in high-temperature processes like smelting and refining metals due to their superb thermal resistance. The Square Graphite Boat, thanks to its seamless design and superior thermal conductivity, optimizes these processes by reducing energy loss and enhancing heat transfer efficiency. Its chemical stability further ensures a clean, contaminant-free environment, making it invaluable in controlled chemical reactions and laboratory settings.4. Commitment to Quality and Sustainability:The company behind the Square Graphite Boat is committed to producing high-quality, sustainable products. They adhere to stringent quality control measures, ensuring that every boat manufactured meets industry standards and customer specifications. Additionally, their responsible sourcing practices guarantee the usage of eco-friendly materials, minimizing the environmental impact.Conclusion:The Square Graphite Boat represents a significant technological milestone in the graphite industry, addressing the evolving needs of diverse sectors. Its impeccable design, high thermal conductivity, and resistance to thermal stress cracks make it an indispensable tool in various high-temperature industrial processes. The versatile applications of this boat, from semiconductor manufacturing to energy storage and metallurgical industries, highlight its immense potential. With a strong focus on quality and sustainable practices, the company behind this innovative product is steadfastly contributing to the growth and development of industries around the globe.
Professional Graphite Crucible Manufacturer for Metal Melting and Casting in China. Get a Quick Quote Now.
Densification Treatment Graphite Crucible - What You Need to KnowGraphite crucibles are widely used in a variety of industrial processes ranging from metal melting to chemical production. Their high thermal conductivity, low coefficient of thermal expansion, and excellent resistance to corrosion and oxidation make them an ideal material for such applications. However, not all graphite crucibles are created equal, and one crucial aspect that sets them apart is their level of densification treatment.Densification treatment involves subjecting the graphite material to high pressure and high temperature to remove any residual porosity, resulting in a denser and more uniform structure. This process has significant implications for the thermal and mechanical properties of the finished product.In metal melting applications, for instance, a denser graphite crucible means better heat transfer and less thermal shock. A denser crucible can also withstand higher temperatures without cracking or degrading, allowing for longer service life and fewer replacements. In addition, a higher level of densification can improve the crucible's resistance to chemical attack, a critical factor in chemical production processes.Metal Melting & Casting Graphite Crucible Manufacturer offers a range of graphite crucibles with varying levels of densification treatment to suit different industrial needs. For example, their isostatic graphite crucibles are made through a unique process that ensures uniformity in density, resulting in high purity and excellent resistance to thermal shock.Another key factor to consider when choosing a graphite crucible is its grain size. A smaller grain size means a denser and stronger product, but it also makes the crucible more brittle and prone to cracking under impact. Manufacturers like Metal Melting & Casting Graphite Crucible Manufacturer carefully control the manufacturing process to balance the crucible's properties and ensure optimum performance.In addition to densification and grain size, the quality of the raw materials used in the manufacturing process also affects the final product's properties. Graphite crucibles made from high-quality graphite, such as isostatic graphite, offer superior performance in demanding applications due to their excellent thermal and mechanical properties.In conclusion, densification treatment is a critical factor to consider when choosing a graphite crucible for industrial processes. It affects the crucible's thermal and mechanical properties, resistance to chemical attack, and service life. Choosing a reputable manufacturer like Metal Melting & Casting Graphite Crucible Manufacturer that offers high-quality graphite crucibles with varying levels of densification treatment can help ensure optimum performance for your application.
Top Suppliers of Graphite Products and Adhesives for Vacuum Furnaces
Graphite Products for Vacuum Furnace: The Ultimate GuideGraphite products help engineers and manufacturers optimize their application's performance in high-temperature environments, such as vacuum furnaces. Graphite is known for its exceptional thermal stability, thermal conductivity, and chemical inertness, which makes it the go-to material for many critical applications. In this blog post, we will explore the different types of graphite products for vacuum furnace and their benefits.Graphite Heating ElementsGraphite heating elements are primarily used to generate high temperatures inside the vacuum furnace. They consist of graphite rods or tubes that radiate heat when an electric current passes through them. Graphite heating elements are preferred over traditional heating elements because they offer fast heat-up and cool-down times, are energy-efficient, and reliable.Graphite CruciblesGraphite crucibles are ideal for melting and casting operations in vacuum furnaces. They are commonly used to melt metals, alloys, and other materials that require high temperatures and a non-reactive environment. Graphite crucibles are preferred over other materials because they can withstand extreme temperatures without deteriorating or reacting with the material being melted.Graphite InsulationGraphite insulation is used to maintain the high-temperature environment inside the vacuum furnace. It consists of graphite fibers in a high-temperature-resistant matrix. Graphite insulation is used as a liner inside the furnace walls to prevent heat loss and maintain a consistent temperature. It also helps to reduce energy consumption and improve furnace performance.Graphite FoilGraphite foil is a versatile material used in vacuum furnace applications, such as insulation, heating elements, and gaskets. It is a thin and flexible material made from high-purity graphite that is compressed and rolled into sheets. Graphite foil offers excellent thermal conductivity, chemical resistance, and mechanical properties, making it an ideal material for vacuum furnace applications.Graphite GasketsGraphite gaskets are used to seal various components inside the vacuum furnace, such as doors, lids, and flanges. They are preferred over other gasket materials because of their thermal stability, chemical resistance, and low outgassing properties. Graphite gaskets are also easy to install and remove, making them ideal for frequent maintenance.Graphite TubesGraphite tubes are commonly used as heating elements inside the vacuum furnace. They are made from high-purity graphite and can withstand extreme temperatures and corrosive environments. Graphite tubes are also used to transport corrosive gases and liquids in vacuum furnace applications.ConclusionGraphite products are essential components of vacuum furnace applications. They provide exceptional thermal stability, thermal conductivity, and chemical inertness, making them ideal for high-temperature environments. Graphite heating elements, crucibles, insulation, foil, gaskets, and tubes are just a few examples of the many types of graphite products available for vacuum furnace applications. Choosing the right graphite product for your specific application can help you optimize its performance and efficiency.