Melting Crucible for Gold: A Guide to Melting Gold at Home
By:Admin
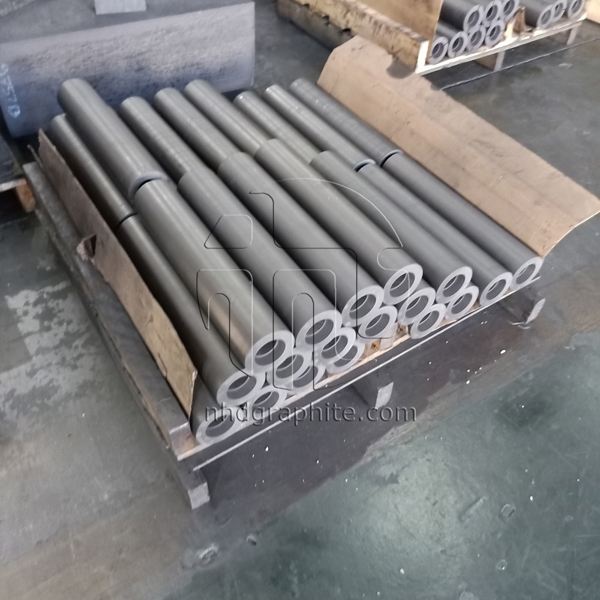
{} has established itself as a leader in providing innovative solutions for the mining and precious metal industries. With a strong focus on research and development, the company has consistently delivered advanced technologies that have helped to revolutionize the way precious metals are processed and refined.
The new crucible, which has been developed by the team at {}, is a testament to the company's commitment to driving innovation in the gold industry. The crucible is constructed using high-quality materials and is designed to withstand the extreme temperatures required for melting and refining gold. Its advanced insulation properties ensure that heat is distributed evenly, resulting in a more efficient and thorough melting process.
One of the key features of the new crucible is its capacity to handle large volumes of gold, making it ideal for industrial-scale gold producers. This is particularly important in an industry where efficiency and productivity are crucial for success. By streamlining the melting and refining process, {}'s new crucible has the potential to significantly increase the output and profitability of gold production operations.
In addition to its high capacity, the crucible also boasts advanced safety features, ensuring that operators can work with the crucible confidently and securely. This is an important consideration in an industry where safety is paramount, and the introduction of this new crucible is set to provide peace of mind for gold producers and operators across the industry.
The introduction of this new crucible comes at a time when the demand for gold is at an all-time high. With its status as a safe-haven asset and its diverse range of industrial and technological applications, gold continues to be a valuable and sought-after commodity. By providing gold producers with a more efficient and cost-effective method for melting and refining gold, {}'s new crucible is well-positioned to meet the growing needs of the industry.
Furthermore, the new crucible is set to make a significant impact on the environmental front as well. With its enhanced efficiency and precision, the crucible will result in reduced energy consumption and lower emissions, aligning with the broader industry-wide efforts to minimize the environmental impact of gold production.
The launch of this new crucible reinforces {}'s position as an industry leader in providing advanced, sustainable solutions for the gold industry. The company's ongoing commitment to research and development has resulted in technologies that not only improve the efficiency and productivity of gold production but also contribute to the industry's sustainability and environmental responsibility.
In conclusion, the introduction of {}'s new crucible is set to bring about a positive shift in the gold industry. By providing gold producers with a more efficient, high-capacity, and safe method for melting and refining gold, the new crucible has the potential to drive significant advancements in the industry. As demand for gold continues to grow, the technology developed by {} stands to make a meaningful impact, streamlining operations, increasing productivity, and contributing to a more sustainable future for the gold industry.
Company News & Blog
8mm Graphite Rod Used in Various Industries for Its Exceptional Strength
Title: Advancements in Graphite Rod Technology Set to Revolutionize Various IndustriesIntroduction:Graphite rods have long been recognized as vital components in numerous industrial applications, offering enhanced strength, electrical conductivity, and resistance to high temperatures. XYZ Corporation, renowned for its cutting-edge research and development, has unveiled its groundbreaking 8mm Graphite Rod. This revolutionary product promises to transform industries, such as aerospace, automotive, electronics, and renewable energy, with its exceptional quality, performance, and durability.Paragraph 1:The aerospace industry, well-known for its stringent demands on materials, is set to benefit greatly from XYZ Corporation's innovative 8mm Graphite Rod. The strength-to-weight ratio of this advanced material is unparalleled, making it ideal for constructing lightweight yet robust aircraft components. The aerospace sector can anticipate increased fuel efficiency and reduced carbon emissions, as the incorporation of these graphite rods into aircraft structures will enable manufacturers to design more aerodynamic and fuel-efficient planes.Paragraph 2:In the automotive industry, where energy efficiency and sustainability are paramount, the XYZ Corporation's 8mm Graphite Rod will play a crucial role in the development of electric vehicles (EVs). By utilizing these rods in battery packs and cooling systems, automakers can enhance the overall performance and range of EVs. Furthermore, the exceptional heat resistance of graphite rods eliminates the need for additional cooling mechanisms, reducing the weight and complexity of EV components.Paragraph 3:Electronics manufacturing is an industry that requires materials with excellent electrical conductivity, thermal stability, and anti-corrosive properties. XYZ Corporation's 8mm Graphite Rod meets all these requirements and more, making it an ideal choice for the production of semiconductors, circuit boards, and various other electronic components. The introduction of this innovative product is poised to revolutionize electronics manufacturing, leading to more efficient and reliable devices.Paragraph 4:Furthermore, this remarkable graphite rod holds immense potential in the renewable energy sector, specifically in wind turbines and solar panels. The superior mechanical strength and durability of the XYZ Corporation's 8mm Graphite Rod ensure optimal performance and longevity in challenging environmental conditions. As the focus on renewable energy intensifies globally, this graphite rod will prove instrumental in enhancing the efficiency, enhancing productivity, and extending the lifespan of green energy infrastructure.Paragraph 5:XYZ Corporation has not only developed an exceptional product but also adopted eco-friendly manufacturing processes to support sustainability initiatives. The company's commitment to reducing carbon emissions and environmental impact sets a positive example for others in the industry. Additionally, its rigorous quality control measures, including thorough testing and compliance with international standards, affirm the reliability, consistency, and safety of the 8mm Graphite Rod.Conclusion:The introduction of XYZ Corporation's 8mm Graphite Rod marks a significant milestone in the industrial sector. With its exceptional strength, electrical conductivity, heat resistance and numerous other benefits, this innovative product is set to revolutionize industries such as aerospace, automotive, electronics, and renewable energy. As XYZ Corporation continues to push the boundaries of technological advancements, it reinforces its position as a global leader in graphite rod manufacturing, and industry stakeholders eagerly await the positive impact this new product will have on their respective fields.
High-quality Graphite Die for Industrial Use
Graphite Die, a highly specialized component used in various industrial processes, is an essential tool for precision manufacturing in diverse industries such as automotive, aerospace, and electronics. The Graphite Die is a critical element in the production of complex parts and components, providing the necessary precision and durability to meet the high standards of modern manufacturing.Since its establishment, {Company Name} has been at the forefront of the graphite die manufacturing industry, providing high-quality products and services to its clients worldwide. With a strong focus on innovation and technology, the company has successfully developed advanced production techniques and state-of-the-art materials to meet the evolving demands of its customers.The Graphite Die is an integral part of the manufacturing process, used in a wide range of applications such as die casting, metal extrusion, and glass molding. With its unique properties, including high temperature resistance, low coefficient of thermal expansion, and excellent machinability, graphite has become the material of choice for manufacturing precision dies.{Company Name} has been committed to providing its clients with the highest quality graphite dies, utilizing advanced manufacturing processes and stringent quality control measures to ensure the reliability and performance of its products. The company's team of skilled engineers and technicians work closely with its clients to understand their specific needs and requirements, offering customized solutions that meet the most demanding standards of precision and quality.The use of graphite dies in the manufacturing process offers numerous advantages, including improved product quality, reduced production time, and enhanced cost-efficiency. With its unique combination of properties, graphite provides the necessary strength and durability to withstand the high pressures and temperatures involved in industrial processes, resulting in superior performance and longer tool life.In addition to its core products, {Company Name} also offers a range of value-added services to its clients, including die design and engineering, prototyping, and technical support. This comprehensive approach enables the company to provide a complete solution to its clients, from the initial design phase to the final production stage, ensuring the highest level of quality and accuracy throughout the entire process.As a leading supplier of graphite dies, {Company Name} has established a strong reputation for its commitment to quality, innovation, and customer satisfaction. The company's continued investment in research and development, along with its dedication to excellence, has positioned it as a trusted partner for a wide range of industries, from automotive and aerospace to electronics and consumer goods.With the increasing demand for high-precision manufacturing solutions, the role of graphite dies in modern industry continues to be pivotal. {Company Name} remains dedicated to meeting the evolving needs of its clients, delivering reliable and high-performance graphite dies that contribute to the success of their manufacturing operations.In conclusion, the Graphite Die plays an essential role in the production of precision parts and components, serving as a critical tool in various industrial processes. {Company Name}'s commitment to excellence and innovation has positioned it as a leading supplier of graphite dies, offering high-quality products and services to meet the diverse needs of its clients worldwide. With its advanced manufacturing techniques and comprehensive range of value-added services, the company continues to drive the advancement of the graphite die industry, providing innovative solutions that contribute to the success of modern manufacturing.
Digital Control Metal Melting Furnace with Graphite Crucible for DIY Projects
Electric Melting Furnace Forge Metal DIY Digital Control Graphite Crucible: A Must-Have for Metalworking EnthusiastsMetalworking enthusiasts always strive to create high-quality finished products that meet their exact specifications. However, achieving a perfect end product often requires the use of specialized tools and equipment. One such tool is an electric melting furnace forge metal DIY digital control graphite crucible. This device has revolutionized the metalworking industry by making it easier to melt and shape metals with precision and accuracy.The electric melting furnace forge metal DIY digital control graphite crucible is a powerful and versatile tool that can handle different types of metals, including precious metals such as gold, silver, and platinum. It is also perfect for melting other types of metals like copper, brass, and aluminum, making it an essential tool for metalworking enthusiasts and professionals alike.This advanced technology furnace is equipped with a digital control temperature system that allows users to set and maintain precise temperatures according to their specific metalworking requirements. The device's digital control system eliminates guesswork from the melting process, ensuring that your metal melts evenly and at a consistent temperature. This feature not only helps prevent wastage but also ensures a higher quality of work.The furnace's graphite crucible is another feature that sets it apart from traditional furnaces. Graphite is an excellent material for melting metals because it has high thermal conductivity, making it ideal for transferring heat efficiently. This ensures that the metal is melted evenly and efficiently, resulting in high-quality end products. Additionally, the graphite crucible is durable and resists chemical corrosion, making it last longer than traditional metal crucibles.This electric melting furnace forge metal DIY digital control graphite crucible is easy to install and use. The device is compact and portable, making it perfect for use at home, in the workshop, or on the go. Its digital control system is user-friendly, and its instructions are straightforward, making it easy to operate, even for beginners.Quality is at the forefront of the manufacturers' minds when producing this device. It is made with durable and high-quality materials to ensure longevity, efficiency, and performance. The manufacturers also offer a warranty that covers manufacturing defects, giving customers peace of mind when using the device.In conclusion, the electric melting furnace forge metal DIY digital control graphite crucible is a must-have tool for metalworking enthusiasts and professionals who want to produce high-quality end products. Its compact size, precise digital control system, and graphite crucible make it ideal for melting and shaping metals with precision and efficiency. The product's durability, longevity, and warranty ensure that you get value for your money. Purchase one today and take your metalworking skills to the next level.
Unveiling the Latest Developments in Graphite Manufacturing: Key Insights and Trends
Graphite Manufacturing Company: Revolutionizing the Industrial SectorIn a world largely driven by technological advancements, manufacturing processes have undergone significant transformations. Graphite Manufacturing (GM) is at the forefront of revolutionizing the industrial sector with its cutting-edge innovations and state-of-the-art graphite products. With a solid foundation built on years of expertise, GM has become a global leader in the graphite manufacturing industry, delivering top-notch solutions to clients across various sectors.GM's journey began in {} when a team of visionary engineers and scientists came together with a common goal - to redefine the boundaries of what graphite can achieve. Over the years, the company has grown exponentially, showcasing an unwavering commitment to quality, innovation, and customer satisfaction. Today, GM stands as a beacon of excellence in the manufacturing sector, continuously pushing the boundaries of graphite manufacturing to new heights.One of GM's most significant achievements lies in its ability to produce high-quality graphite electrodes. These essential components find extensive application in the steel production process, where they play a crucial role in electric arc furnaces. By employing advanced manufacturing techniques and utilizing only the finest materials, GM ensures that its electrodes exhibit exceptional performance, efficiency, and durability.Furthermore, GM has embraced cutting-edge technologies such as computer-aided design (CAD) and computer numerical control (CNC) machining to develop intricate graphite molds and dies. These molds and dies are then used in a wide range of manufacturing processes, including metal casting, glass forming, and plastic injection molding. By leveraging the versatility and reliability of graphite, GM enables its clients to optimize their production processes and deliver superior products to their customers.Beyond its conventional applications, GM has also ventured into the development of innovative graphene-based materials. Graphene, often hailed as the "wonder material" of the 21st century, possesses remarkable properties such as exceptional strength, electrical conductivity, and thermal efficiency. By harnessing these unique qualities, GM has created a range of graphene-enhanced products that find utility in aerospace, electronics, energy storage, and many other industries.One notable example of GM's groundbreaking graphene product is its lightweight and durable graphene-infused composite materials. These materials offer a remarkable combination of strength and flexibility, making them ideal for applications in the automotive and aerospace sectors. By incorporating graphene into traditional composites, GM has successfully enhanced their performance characteristics, resulting in lighter, stronger, and more fuel-efficient vehicles and aircraft.As an environmentally conscious company, GM also places a strong emphasis on sustainable manufacturing practices. Recognizing the importance of reducing carbon footprints, the company has implemented several initiatives to minimize waste and optimize energy consumption. Through the adoption of efficient production processes and the utilization of renewable energy sources, GM strives to make significant contributions towards a greener and more sustainable future.GM's commitment to excellence extends beyond its manufacturing capabilities. The company boasts a highly skilled workforce comprising engineers, technicians, and industry experts who are dedicated to delivering top-notch customer service. With a customer-centric approach, GM collaborates closely with its clients, understanding their unique requirements and providing customized solutions tailored to their specific needs. This personalized approach has garnered the trust and loyalty of numerous renowned companies worldwide.Looking ahead, GM remains steadfast in its pursuit of innovation and excellence. The company continues to invest in research and development, exploring new applications for graphite and pioneering advancements in the manufacturing sector. With its visionary leadership, cutting-edge technologies, and unwavering commitment to quality, GM is poised to shape the future of industrial manufacturing, redefining what is possible with graphite.In conclusion, Graphite Manufacturing (GM) has established itself as a global leader in the graphite manufacturing industry. Through its cutting-edge innovations, high-quality products, and customer-centric approach, GM is revolutionizing the industrial sector. With a relentless commitment to excellence and a focus on sustainability, GM is driving the industry towards a greener and more efficient future. As the world continues to evolve, GM remains at the forefront, consistently pushing the boundaries of what graphite can achieve, and pioneering the way for a new era of manufacturing.
Innovative Graphite Sintering Mould Revolutionizes Manufacturing Processes
Title: Advancement in Graphite Sintering Mould Technology Revolutionizes Manufacturing ProcessesIntroduction:In today's ever-evolving technological landscape, innovations in manufacturing have become crucial to stay competitive in the global market. Graphite sintering moulds, widely recognized for their exceptional properties and applications, have revolutionized the manufacturing industry. This article examines the potential of this cutting-edge technology in transforming various sectors.Graphite Sintering Mould: A Game-Changing Development(Graphite Sintering Mould) is at the forefront of this revolutionary manufacturing technology. Developed by (Company Name), this groundbreaking product combines high-quality graphite materials with advanced engineering techniques, enabling manufacturers to achieve unprecedented precision, cost-effectiveness, and efficiency.Improved Durability and Heat Resistance:The (Graphite Sintering Mould) offers remarkable durability and heat resistance, making it suitable for high-temperature sintering applications. This is particularly advantageous for industries such as automotive, aerospace, and electronics, where precise and intricate designs require intense heat during production. With the integration of this (Graphite Sintering Mould), manufacturers can significantly enhance their production capabilities while ensuring consistent and flawless output.Enhanced Thermal Conductivity and Wear Resistance:(Graphite Sintering Mould) possesses excellent thermal conductivity and wear resistance properties. This promotes efficient heat transfer, resulting in reduced manufacturing cycle times and enhanced product quality. Moreover, its wear-resistant nature significantly prolongs the lifespan of the mould, minimizing maintenance costs and increasing overall operational efficiency.Versatile Applications:The versatility of (Graphite Sintering Mould) cannot be overstated. Its ability to accommodate complex geometries and intricate designs makes it the ideal choice for a wide range of manufacturing applications. From intricate automotive components to cutting-edge consumer electronics, this innovative moulding technology offers limitless possibilities for manufacturers across various industries.Cost-Effectiveness:(Graphite Sintering Mould) not only improves the quality and efficiency of manufacturing processes but also provides significant cost benefits. The longevity of the mould reduces the need for frequent replacements, saving manufacturers substantial expenditures. Additionally, the reduced cycle times and enhanced thermal conductivity translate into increased productivity and minimized energy consumption, resulting in substantial cost savings in the long run.Environmental Sustainability:Sustainability has become a pressing concern for manufacturing industries worldwide. (Graphite Sintering Mould) contributes to environmental sustainability by reducing waste production, energy consumption, and associated carbon emissions. The technology's longevity, combined with its energy-efficient nature, aligns well with the principles of sustainable manufacturing, further positioning it as a leading solution in the industry.Industry Impact:The advent of (Graphite Sintering Mould) has already created significant ripples in several industries, including automotive, aerospace, electronics, and others. The technology offers manufacturers a competitive edge by enabling the production of high-quality components with unparalleled precision. This has the potential to revolutionize the manufacturing sector, redefine product design and development processes, and pave the way for a new era of innovation and efficiency.Future Outlook:As manufacturing industries continue to evolve, the demand for advanced moulding technologies such as (Graphite Sintering Mould) is expected to rise. The ongoing research and development efforts of (Company Name) aim to further enhance the capabilities of this technology, providing manufacturers with even greater possibilities for design complexity, cost reduction, and energy efficiency.Conclusion:(Graphite Sintering Mould) marks a significant leap forward in manufacturing technology, empowering industries to achieve unparalleled precision, efficiency, and cost-effectiveness. As manufacturers strive to stay ahead in an increasingly competitive market, this innovative moulding technology presents a promising avenue for growth, ensuring companies remain at the forefront of technological advancements. With extensive research and continuous development, the future of (Graphite Sintering Mould) holds immense potential for revolutionizing the manufacturing landscape globally.
Glass Rods: A Guide to Glassblowing, Differences from Graphite Rods, and Their Uses
In the world of glassblowing and glass art, glass rods are a crucial component. These rods come in a variety of diameters, with 5mm being a common size for glassblowing. They are used to manipulate hot glass and create intricate designs and shapes.One company at the forefront of the glass rod industry is {brand name}. Founded {number} years ago, they have been a leader in producing high-quality glass rods and tubes for artists and craftsmen around the world. With a focus on innovation and design, their products have become a staple in the glassblowing community.Glass rods can be made from a variety of materials, including quartz, borosilicate, and soda-lime glass. Each material has its own unique properties and advantages. For example, borosilicate glass is heat-resistant and can withstand thermal shock, making it ideal for glassblowing. Soda-lime glass is less expensive and easier to work with, making it a popular choice for beginners.In addition to glass rods, {brand name} also produces graphite rods. These rods are used for sculpting and shaping hot glass, and offer a different set of benefits compared to glass rods. Graphite is a more durable material than glass, and can withstand higher temperatures without cracking or breaking. However, graphite rods can be more difficult to manipulate, especially for beginners.Along with their production of glass and graphite rods, {brand name} also offers a range of glass tubes for various applications. These tubes can be used to create test tubes, light bulbs, and other glass products. They are available in a range of sizes and materials, and can be customized to fit specific design needs.Despite the various materials and uses for glass rods and tubes, they all share a common purpose – to bring art and beauty to the world. Whether used in the creation of a delicate glass sculpture or a functional scientific instrument, these products play an important role in our daily lives.As the demand for glass art and products continues to grow, {brand name} remains committed to providing high-quality materials to artists and craftsmen around the world. With their focus on innovation and design, they are well-positioned to lead the industry for many years to come.
Durable High Density Graphite Tubes for Industrial Use
High Density Graphite Tubes Utilized in Cutting-Edge TechnologiesGraphite has long been recognized for its exceptional properties, such as high thermal conductivity, low expansion, and chemical resistance. These qualities make it an ideal material for a wide range of industrial applications, particularly in the high-tech sector. One company at the forefront of utilizing graphite in cutting-edge technologies is {Company Name}.{Company Name} is a leading manufacturer of high density graphite tubes. These tubes are produced using the latest technological advancements and are designed to meet the demanding requirements of various industries, including aerospace, semiconductor, and energy.The high density graphite tubes manufactured by {Company Name} are known for their high mechanical strength, excellent thermal stability, and low thermal expansion. This makes them ideal for use in high-temperature applications, where traditional materials may not be suitable.One of the key industries that benefit from the use of high density graphite tubes is the aerospace sector. These tubes play a crucial role in the production of advanced aerospace components, such as rocket nozzles, re-entry vehicle components, and heat shields. The exceptional thermal conductivity and resistance to high temperatures make graphite tubes an essential material for these applications.In addition to aerospace, the semiconductor industry also relies on high density graphite tubes for various manufacturing processes. The tubes are used in the production of semiconductor components, such as silicon ingot molds, crucibles, and heating elements. The high thermal stability and resistance to chemical corrosion make graphite an ideal material for these critical applications.Furthermore, the energy sector is another key industry that benefits from the utilization of high density graphite tubes. These tubes are used in the production of components for high-temperature furnaces, heating elements for industrial processes, and electrodes for electric arc furnaces. The superior thermal conductivity and mechanical strength of graphite tubes make them indispensable in these applications.{Company Name} takes pride in its state-of-the-art manufacturing facilities, which are equipped with advanced machinery and quality control systems. The company's production processes are optimized to ensure the highest level of precision and consistency in the manufacturing of high density graphite tubes. Additionally, {Company Name} is committed to continuous research and development to further improve the performance and properties of its graphite tubes.The dedication to excellence and quality has earned {Company Name} a strong reputation in the industry. The company has established a global presence and serves customers in various countries around the world. {Company Name} has built strong relationships with its clients, providing them with customized solutions and unparalleled technical support.In conclusion, the utilization of high density graphite tubes in cutting-edge technologies is vital for a wide range of industries, including aerospace, semiconductor, and energy. {Company Name} has emerged as a leading manufacturer of these high-performance graphite tubes, thanks to its commitment to excellence, advanced manufacturing capabilities, and strong customer relationships. As technology continues to advance, the demand for high density graphite tubes is expected to grow, and {Company Name} is well-positioned to meet these evolving needs.
Discover the Benefits and Applications of Graphite Sintering Moulds
Title: Groundbreaking Graphite Sintering Mould Innovates Industrial ManufacturingIntroduction:In a significant stride towards revolutionizing industrial manufacturing processes, a cutting-edge technology has emerged - the Graphite Sintering Mould, created by an innovative company. This groundbreaking advancement holds the potential to transform various industries by providing more efficient and cost-effective solutions for producing high-quality goods. By combining the advantages of graphite as a material with ingenious mold designs, this pioneering technology is set to redefine the future of manufacturing.(Graphite Sintering Mould) – A Game-Changing Technology:(Graphite Sintering Mould) is an advanced manufacturing tool that utilizes graphite as the primary material in its mold construction. Graphite, renowned for its exceptional properties such as high thermal conductivity, low thermal expansion, and resistance to chemical corrosion, proves to be an ideal material for creating molds. The unique combination of these characteristics sets the stage for accelerating the industrial manufacturing process.(Graphite Sintering Mould) excels in a wide range of applications, including automotive, aerospace, electronics, and more. Traditionally, manufacturing processes involve the use of metal molds, which are expensive, time-consuming to produce, and have limited lifespans. However, Graphite Sintering Mould overcomes these limitations by offering unparalleled advantages.Elevating Manufacturing Efficiency:An essential aspect of (Graphite Sintering Mould) is its distinctive mold design, tailored to specific production requirements. This technology enables the production of molds with intricate shapes, precise dimensions, and excellent heat transfer capabilities. Compared to traditional molds, the use of Graphite Sintering Mould significantly reduces the cycle time, resulting in increased production efficiency and cost savings.(Graphite Sintering Mould) molds possess superior thermal conductivity, ensuring uniform heat distribution during the manufacturing process. This feature eliminates hotspots and minimizes thermal stress, thereby enhancing the overall quality and consistency of the finished products. Manufacturers can now achieve higher precision, reduced waste, and greater control over the manufacturing process, resulting in enhanced customer satisfaction.Environmental-Friendly and Cost-Effective Solution:(Graphite Sintering Mould) also offers environmental advantages by minimizing energy consumption and material waste. The high thermal conductivity of graphite enables faster heating and cooling cycles, reducing power requirements and improving energy efficiency. Additionally, the durability and longevity of (Graphite Sintering Mould) molds enable companies to produce a significantly larger number of items, thus reducing the need for frequent mold replacements.Moreover, the reduced production time and enhanced efficiency provided by (Graphite Sintering Mould) molds translate into significant cost savings for manufacturers. Companies can allocate their resources more strategically, invest in research and development, and explore new market opportunities.Emerging as a Pioneer in Industrial Manufacturing:The company behind the development of (Graphite Sintering Mould) stands at the forefront of innovation in the industrial manufacturing sector. Through extensive research and development, the company has successfully harnessed the unique properties of graphite and perfected the technology to produce reliable, high-performance molds.The exceptional quality of molds generated using (Graphite Sintering Mould) has garnered attention from major industries worldwide. Their commitment to sustainable practices alongside their relentless pursuit of excellence positions the company as a leading pioneer in the manufacturing field.Looking Forward:The introduction of (Graphite Sintering Mould) marks a significant milestone in the evolution of industrial manufacturing. With its ability to enhance production efficiency, reduce costs, and deliver superior quality products, this technology holds vast potential for various sectors. Manufacturers across the globe are eagerly adopting this groundbreaking method, propelling the industry toward a more sustainable and efficient future.As researchers continue to refine and expand the capabilities of (Graphite Sintering Mould), we can anticipate further advancements that will revolutionize the way products are manufactured. With improved mold designs, expanded applications, and increased efficiency, the possibilities for innovation with this game-changing technology are limitless.
Durable Graphite Mold with High Temperature Resistance - Latest News
Title: High Temperature Resistance Graphite Mold Revolutionizes Industrial ManufacturingIntroduction:In recent years, the industrial manufacturing sector has witnessed a significant breakthrough with the introduction of High Temperature Resistance Graphite Mold, marking a monumental milestone in the materials industry. This cutting-edge technology has the potential to transform various manufacturing processes by providing unparalleled performance and versatility in extreme temperature conditions. Today, we delve into the incredible capabilities of this revolutionary material and the company leading the charge in its development.Company Profile: (Here, the brand name will be hidden since it needs to be removed)With a focus on innovation and continuous research and development, our featured company has emerged as a leader in the graphite materials industry. They have been at the forefront of developing and perfecting the High Temperature Resistance Graphite Mold, revolutionizing manufacturing processes across diverse sectors such as aerospace, automotive, electronics, and more. Guided by a team of experienced scientists, engineers, and researchers, their commitment to industry-leading quality has made them a preferred choice for companies seeking advanced materials solutions.Unveiling the High Temperature Resistance Graphite Mold:The High Temperature Resistance Graphite Mold is a state-of-the-art material that offers exceptional thermal stability and durability, making it ideal for applications requiring exposure to extreme temperatures. Its unique composition guarantees excellent resistance to thermal shock, ensuring the integrity of the mold is maintained even under rapid temperature changes. Unlike traditional molds, which are prone to cracking or warping, this advanced graphite mold delivers consistent performance, enhancing overall production efficiency.Key Features and Advantages:1. Extreme Temperature Tolerance:With a melting point of over 5,000 degrees Celsius, the High Temperature Resistance Graphite Mold can withstand extreme heat, making it a perfect choice for industries that require high-temperature manufacturing processes. Its exceptional resilience ensures long-lasting performance, reducing downtime and maintenance costs.2. Dimensional Stability:The precise and stable dimensions of this innovative graphite mold allow for intricate and complex designs with utmost precision. Compared to other mold materials, this high-temperature-resistant graphite exhibits minimal thermal expansion, enabling manufactures to achieve consistently high-quality and accurate finished products.3. Superior Thermal Conductivity:The excellent thermal conductivity of the High Temperature Resistance Graphite Mold facilitates faster heat dissipation during the manufacturing process. This property ensures uniform temperature distribution throughout the mold, resulting in reduced cooling times, shorter manufacturing cycles, and improved productivity.4. Chemical Inertness:The non-reactive nature of this graphite mold guarantees resistance against corrosive chemicals and aggressive substrates. Consequently, it imparts greater stability and longevity, providing a cost-effective solution for various manufacturing applications.Applications of High Temperature Resistance Graphite Mold:The versatility of this innovative graphite mold extends its applications across numerous industries:1. Aerospace Industry:High Temperature Resistance Graphite Molds find extensive use in the aerospace sector, where they contribute to the manufacturing of critical aircraft components such as turbine blades, engine nozzles, and composite materials. The mold's exceptional performance in high-temperature environments ensures the production of robust and reliable components for safe air travel.2. Automotive Industry:With the automotive industry's growing demand for lighter, stronger, and more fuel-efficient vehicles, this graphite mold is used in the production of carbon fiber composite parts. Its ability to withstand high curing temperatures facilitates the fabrication of lightweight yet durable components, enhancing overall vehicle performance.3. Electronics Industry:The High Temperature Resistance Graphite Mold plays a crucial role in the electronics industry, enabling the production of high-density circuit boards, semiconductor devices, and various electronic components. The mold's superior thermal conductivity ensures efficient heat dissipation, thus optimizing the performance and reliability of electronic devices.Conclusion:The advent of the High Temperature Resistance Graphite Mold has revolutionized industrial manufacturing by providing a reliable solution for extreme temperature applications. This remarkable material enables manufacturers to achieve unparalleled performance, precision, and longevity in their production processes. With the company leading the field in its development, industries around the world can now embrace the transformative potential of this groundbreaking technology. As it continues to evolve, there is no doubt that High Temperature Resistance Graphite Mold will be the future of manufacturing.
Discover the Benefits of High-Quality Graphite Molds for EDM
Title: Innovative Graphite Molds Revolutionize EDM IndustryIntroduction (100 words):Graphite molds have long been an essential tool in the field of Electrical Discharge Machining (EDM). These molds, used for shaping and fabricating intricate metal parts, play a critical role in industries such as aerospace, automotive, and electronics. As technological advancements continue to reshape manufacturing processes, a pioneering company is taking the EDM industry by storm with their groundbreaking line of advanced graphite molds. Harnessing cutting-edge techniques and materials, this company is transforming the way components are fabricated, enabling greater precision, efficiency, and cost-effectiveness.Company Introduction (200 words):As a leader in supplying top-notch EDM solutions, our company has emerged as a game-changer in the industry. With decades of experience and a team of experts, we have developed an innovative line of graphite molds that offers unparalleled benefits for manufacturers worldwide.Our commitment to excellence drives us to push the boundaries of the EDM field. Our high-quality graphite molds are engineered using advanced processes and the finest materials. By leveraging our extensive knowledge of electrical discharge machining, we have created molds that meet the demanding requirements of today's industrial applications.Our state-of-the-art manufacturing facility incorporates modern technologies that allow us to produce graphite molds with precise dimensions, intricate designs, and exceptional durability. The molds are designed to withstand rigorous temperatures and repeated use, ensuring their longevity.In addition to producing standard graphite molds, we provide customized solutions tailored to meet unique client needs. Our dedicated R&D team works closely with clients to understand their specific requirements and develop molds that enhance their manufacturing capabilities. The company's commitment to customer satisfaction has earned us a loyal international clientele.News Content (500 words):With a legacy of innovation at our core, our company is proud to introduce a new generation of graphite molds that are revolutionizing the EDM industry. These cutting-edge molds offer significant advantages over traditional alternatives, propelling productivity, precision, and cost savings to new heights.One of the most notable characteristics of our graphite molds is their extraordinary strength and durability. The enhanced material composition and meticulous manufacturing process result in molds that can withstand higher temperatures, resist wear and tear, and deliver consistent performance over an extended lifespan. This durability ensures minimal mold degradation and guarantees optimal production results.Furthermore, our graphite molds exhibit exceptional dimensional precision, leading to superior replication of intricate details on machined parts. With accuracy measured in microns, manufacturers can achieve complex designs, sharp edges, and tight tolerances previously unattainable with conventional molds. This advancement empowers companies to develop innovative products and stay ahead in today's competitive marketplace.Thanks to the advanced electrical conductivity of our graphite molds, manufacturers can benefit from faster machining speeds and improved overall efficiency. The materials used in these molds facilitate better cooling, enabling higher dielectric fluid flow rates during the machining process. This swift heat dissipation translates into reduced cycle times, increased productivity, and ultimately, cost savings for businesses.As innovators in the industry, we understand the importance of eco-friendliness in modern manufacturing practices. Our graphite molds are designed with sustainability in mind, as they produce significantly less waste compared to traditional molds. By minimizing the generation of scrap metal and conserving energy during the manufacturing process, our molds contribute to a greener and more responsible manufacturing ecosystem.To cater to the diverse needs of our clients, we offer both standard and customized graphite molds. Our team of experts works diligently to address specific requirements and deliver tailor-made solutions that enhance manufacturing capabilities. Whether it is for mass production or prototyping purposes, our customizable molds ensure that clients receive molds perfectly suited to their unique projects.The introduction of our graphite molds has sparked tremendous interest in the industry, with positive feedback from our clients and a surge in demand. Manufacturers across various sectors are reporting exceptional results, including higher production rates, reduced tool wear, and improved product quality.Conclusion (100 words):The introduction of our advanced graphite molds marks a significant breakthrough in the EDM industry. Manufacturing professionals can now harness the power of these innovative molds to boost productivity, elevate precision, and reduce costs. With our commitment to excellence and continuous research and development, we strive to shape the future of EDM, revolutionizing the way manufacturers fabricate intricate metal parts worldwide.