Premium Graphite Mold For Fiberglass Manufacturing: Superior Quality and Durability
By:Admin
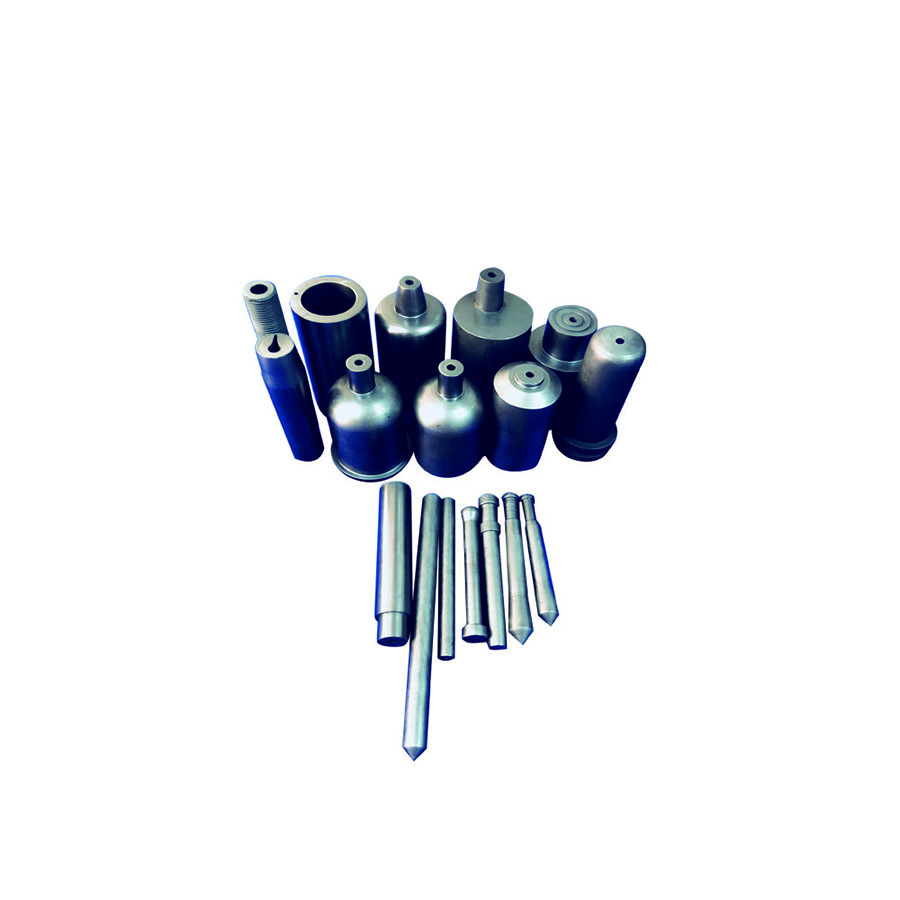
(Graphite Mold For Fiberglass) is revolutionizing the manufacturing industry with its innovative and high-quality graphite molds for fiberglass production. The company has been a leader in the industry for over a decade, providing top-of-the-line products to a wide range of clients in various sectors, including automotive, aerospace, marine, and construction.
The molds manufactured by (Graphite Mold For Fiberglass) are known for their durability, precision, and efficiency. They are designed to withstand high temperatures and pressures, making them ideal for the production of fiberglass components that require intricate and complex shapes. The company's state-of-the-art manufacturing facilities allow them to produce molds of various sizes and specifications, catering to the unique needs of each client.
(Graphite Mold For Fiberglass) prides itself on its commitment to quality and customer satisfaction. The company works closely with its clients to understand their specific requirements and ensures that the molds are tailored to meet their exact specifications. This personalized approach has earned (Graphite Mold For Fiberglass) a stellar reputation in the industry, with many clients commending the company for its reliability and consistency in delivering high-quality products.
The use of graphite molds for fiberglass production offers several advantages over traditional methods. Graphite is an excellent conductor of heat and can withstand extreme temperatures, making it an ideal material for creating molds for fiberglass production. This results in faster cycle times and improved efficiency in the manufacturing process, ultimately leading to cost savings for clients.
In addition to its superior thermal properties, graphite molds also offer exceptional dimensional stability, ensuring that the final fiberglass components maintain their precise shape and dimensions. This level of precision is crucial for industries such as aerospace and automotive, where tight tolerances are essential for optimal performance.
Furthermore, graphite molds are highly resistant to wear and tear, resulting in a longer lifespan compared to traditional molds. This durability means that clients can expect a higher return on their investment, as the molds require less frequent replacement and maintenance.
(Graphite Mold For Fiberglass) is at the forefront of research and development in the field of graphite mold manufacturing. The company continually invests in innovative technologies and processes to improve the performance and capabilities of its molds, staying ahead of industry trends and meeting the evolving needs of its clients.
The use of advanced computer-aided design (CAD) and computer-aided manufacturing (CAM) software allows (Graphite Mold For Fiberglass) to create highly intricate and complex mold designs with exceptional accuracy. This digital design and manufacturing approach also streamlines the production process, reducing lead times and enhancing overall efficiency.
As sustainability and environmental responsibility are increasingly important considerations for businesses, (Graphite Mold For Fiberglass) is committed to minimizing its environmental impact. Graphite is a highly recyclable material, and the company adheres to strict recycling and waste management practices, ensuring that its manufacturing processes are as eco-friendly as possible.
The superiority of graphite molds for fiberglass production has led to a surge in demand for (Graphite Mold For Fiberglass)'s products. The company has seen significant growth in recent years, expanding its client base and establishing itself as a trusted partner for businesses seeking high-quality and reliable graphite molds.
(Graphite Mold For Fiberglass) continues to set the standard for excellence in the manufacturing industry, delivering cutting-edge solutions that empower its clients to achieve their production goals with unparalleled efficiency and precision. With a steadfast commitment to quality, innovation, and customer satisfaction, (Graphite Mold For Fiberglass) is poised to remain a leader in the field for years to come.
Company News & Blog
Top-Quality Graphite Ingot Mould for Efficient Melting
Title: Cutting-Edge Graphite Ingot Mould Revolutionizes the Melting ProcessIntroduction:In today's fast-paced industry, innovation is key to staying ahead of the competition. Company XYZ, a renowned manufacturer specializing in advanced industrial solutions, has unveiled a groundbreaking product – the Graphite Ingot Mould for Melting. This game-changing ingot mould is set to revolutionize the melting process, providing businesses with improved efficiency, cost-effectiveness, and superior quality results.Company XYZ: Pioneers of Industrial SolutionsEstablished over three decades ago, Company XYZ has consistently been at the forefront of industrial advancements. With a strong commitment to research and development, the company has earned a stellar reputation for delivering cutting-edge solutions to global industries. By leveraging the latest technologies and materials, XYZ has consistently revolutionized various sectors.The Groundbreaking Graphite Ingot Mould for Melting:Utilizing state-of-the-art technologies, Company XYZ has developed a graphite ingot mould for melting that surpasses traditional mould material counterparts, such as steel or ceramic. The unique properties of graphite make it an ideal material for this purpose.1. Enhanced Thermal Conductivity: Graphite's exceptional thermal conductivity ensures optimum heat transfer during the melting process, leading to reduced melting times and increased efficiency.2. Superior Heat Resistance: The high mechanical strength and thermal stability of the graphite mould allow it to withstand extreme temperatures without deformation or cracking. This resilience ensures product consistency and longevity.3. Cost-Effective Solution: Compared to conventional mould materials, graphite offers a longer lifespan, reducing the need for frequent replacements or repairs. This results in significant cost savings for businesses.4. Improved Metal Quality: The use of a graphite mould minimizes the risk of contamination during the melting process. Graphite's non-reactive properties prevent unwanted reactions between the mould and the metal, resulting in cleaner, higher-quality ingots.5. Customization Options: Company XYZ provides a comprehensive range of graphite ingot mould sizes and shapes, catering to the diverse needs of different industries. Customization options ensure that businesses can find the perfect mould to suit their requirements.Elevating Industry Standards:The introduction of the Graphite Ingot Mould for Melting by Company XYZ is set to redefine industry standards, driving success in a wide range of sectors, including automotive, aerospace, electronics, and manufacturing, among others. The benefits offered by this innovative solution extend beyond immediate cost savings and efficiency improvements.1. Environmental Sustainability: Graphite is a more eco-friendly alternative compared to traditional mould materials due to its non-reactive nature and reduced energy requirements during the melting process. Using the graphite ingot mould contributes to a greener, cleaner industry.2. Increased Productivity: By reducing melting times and enhancing process efficiency, the mould helps businesses increase their overall productivity. This translates into a higher output within the same timeframe, enabling companies to meet growing demands.3. Quality Assurance: The use of graphite ensures optimal results by preventing mold-induced impurities, resulting in superior-grade ingots. This premium quality enhances the reputation of businesses and paves the way for long-term success.Conclusion:Company XYZ's Graphite Ingot Mould for Melting signals a significant milestone in the advancement of industrial melting processes. By harnessing the exceptional properties of graphite, this innovative product offers businesses unparalleled benefits ranging from improved efficiency and cost-effectiveness to enhanced metal quality and environmental sustainability. Companies across various industries can now elevate their operations with this cutting-edge solution, potentiaŝlly fostering industry-wide growth and success.
Graphite Products Enhance Glass Fiber Strength and Durability
Title: Graphite Product Revolutionizes Glass Fiber Production ProcessIntroduction:In an era marked by rapid technological advancements, the materials used in manufacturing processes are continuously evolving. One remarkable innovation in the field of glass fiber production is the introduction of an exceptional graphite product. This groundbreaking development has been achieved through years of dedicated research and development by a leading company in the field. By leveraging the exceptional properties of this graphite product, they have successfully revolutionized the glass fiber production process, leading to enhanced efficiency, improved product quality, and cost-effectiveness.Company Introduction:Established in [year], [Company Name] has cemented its position as a pioneer in the manufacturing industry. With a focus on innovation and excellence, they have consistently pushed the boundaries of conventional practices. Their commitment to research and development has resulted in several groundbreaking products that have redefined industrial processes across multiple sectors. Leveraging a team of highly skilled professionals and state-of-the-art facilities, [Company Name] has consistently delivered solutions that address the evolving needs of global manufacturers.Graphite Product for Glass Fiber:[Company Name]'s newly developed graphite product for the glass fiber industry is a game-changer. This versatile material possesses exceptional properties that significantly augment the glass fiber production process. Its integration within this industry has the potential to transform the entire manufacturing landscape, boosting efficiency and ultimately driving growth.1. High Thermal Conductivity:The innovative graphite product demonstrates superior thermal conductivity, allowing for better control and management of the production process. By optimizing heat transfer at various stages, it ensures uniform heat distribution, reducing the risk of thermal inconsistencies and material defects. This breakthrough property of the graphite product leads to improved product quality and significantly minimizes manufacturing downtime.2. Enhanced Material Strength:Graphite's inherent strength and resistance to chemical corrosion enable it to withstand the demanding conditions encountered during the glass fiber production process. This reliability equates to longer product life, resulting in reduced downtime due to maintenance and repairs. Additionally, the longevity of the product translates into cost savings for manufacturers in the long run.3. Increased Productivity:By incorporating the graphite product into their production lines, glass fiber manufacturers have reported significant improvements in overall productivity. The material's exceptional lubricity ensures smooth and continuous operations, reducing the risk of equipment breakdown and hindrances. The reduced downtime and enhanced efficiency allow manufacturers to optimize their output, meet increasing market demands, and maintain a competitive edge.4. Environmentally Friendly:[Company Name]'s graphite product is also eco-friendly, aligning with the global trend towards sustainability. Its composition is free from harmful substances, diminishing the industry's environmental footprint. By adopting this innovative product, glass fiber manufacturers underscore their commitment to responsible production and sustainable practices.Conclusion:The integration of [Company Name]'s graphite product into the glass fiber production process represents a monumental advancement within the industry. With its exceptional thermal conductivity, enhanced material strength, increased productivity, and environmentally friendly properties, this revolutionary material offers unparalleled benefits to manufacturers. By reducing manufacturing downtime, improving product quality, and promoting sustainability, [Company Name]'s graphite product paves the way for a more efficient and sustainable glass fiber industry. The collaboration between [Company Name] and glass fiber manufacturers facilitates the realization of untapped potentials, ensuring an exciting and prosperous future for this sector.
Isostatic Graphite Blocks and Rounds: Applications and Properties
Honsin Industry Launches New Range of Isostatic Graphite Blocks & RoundsHonsin Industry, a leading supplier of specialty graphite materials, has launched a new range of Isostatic Graphite Blocks & Rounds. Formed by means of CIP (cold isostatic pressing) technique, isostatic graphite is characterized by its homogeneous structure and excellent isotropic electrical, thermal and mechanical properties. This range of high-quality graphite blocks and rounds offers superior performance and can be used in a variety of industrial and scientific engineering applications.Isostatic graphite is widely used in the metals, glass, semiconductor, biomedical, and aerospace industries. Due to its unique properties, it is used in a wide range of industrial applications and is also highly sought after by scientific researchers. The blocks and rounds produced by Honsin Industry are made from high-quality raw materials that are carefully selected to ensure the final product is of the highest quality. The company uses a special-designed graphitization furnace to remove non-carbonaceous impurities and to ensure the product is purified to an advanced level.The Isostatic Graphite Blocks & Rounds offered by Honsin Industry are known for their excellent isotropic properties. They have a homogeneous structure and proper machinability. The high density and high mechanical strength make them ideal for use in a variety of settings. The blocks and rounds are highly resistant to thermal and chemical reactions, and their resistance to thermal shock (low thermal expansion) makes them perfect for use in high-temperature environments.The new range of Honsin Industry graphite blocks and rounds is ideal for use in a variety of applications. They can be used in the production of molds for continuous casting systems, sintering molds for cemented carbides, diamond tools, and electronic components. The blocks and rounds are ideal for use in the production of molded glass, as well as for use in crucibles for melting precious metals or alloys. In addition, they are useful as electrodes for EDM (Electronic Discharge Machine).The blocks and rounds can be used in heating elements, heat shields, crucibles, boats in furnaces for pulling monocrystalline silicon or optical fibers. Anodes for production of manganese dioxide, metallic magnesium, and rare metals are other applications in which this range of graphite blocks and rounds can be used.Honsin Industry is committed to providing high-quality products that meet the needs of their customers. The company's graphite blocks and rounds are produced using advanced technology and are of the highest quality. They are ideal for use in industrial and scientific engineering and offer a range of benefits that make them ideal for a wide range of applications.The Isostatic Graphite Blocks & Rounds offered by Honsin Industry have excellent electrical conductivity and can be used in a variety of settings. They are ideal for use in electrode applications and can be used in the production of components for a range of applications. The company's blocks and rounds are highly durable and offer a range of advantages over other materials. They are resistant to corrosion, they have excellent thermal conductivity, and they are highly resistant to thermal shock.Overall, the launch of the new range of Isostatic Graphite Blocks & Rounds by Honsin Industry is set to revolutionize the graphite industry. The company's commitment to providing high-quality products that meet the needs of their customers is evident in the quality and performance of their products. Honsin Industry is committed to providing a range of products that meet the needs of their customers and they are confident that their new range of graphite blocks and rounds will do just that.
Discover the Benefits and Applications of Graphite Sintering Moulds
Title: Groundbreaking Graphite Sintering Mould Innovates Industrial ManufacturingIntroduction:In a significant stride towards revolutionizing industrial manufacturing processes, a cutting-edge technology has emerged - the Graphite Sintering Mould, created by an innovative company. This groundbreaking advancement holds the potential to transform various industries by providing more efficient and cost-effective solutions for producing high-quality goods. By combining the advantages of graphite as a material with ingenious mold designs, this pioneering technology is set to redefine the future of manufacturing.(Graphite Sintering Mould) – A Game-Changing Technology:(Graphite Sintering Mould) is an advanced manufacturing tool that utilizes graphite as the primary material in its mold construction. Graphite, renowned for its exceptional properties such as high thermal conductivity, low thermal expansion, and resistance to chemical corrosion, proves to be an ideal material for creating molds. The unique combination of these characteristics sets the stage for accelerating the industrial manufacturing process.(Graphite Sintering Mould) excels in a wide range of applications, including automotive, aerospace, electronics, and more. Traditionally, manufacturing processes involve the use of metal molds, which are expensive, time-consuming to produce, and have limited lifespans. However, Graphite Sintering Mould overcomes these limitations by offering unparalleled advantages.Elevating Manufacturing Efficiency:An essential aspect of (Graphite Sintering Mould) is its distinctive mold design, tailored to specific production requirements. This technology enables the production of molds with intricate shapes, precise dimensions, and excellent heat transfer capabilities. Compared to traditional molds, the use of Graphite Sintering Mould significantly reduces the cycle time, resulting in increased production efficiency and cost savings.(Graphite Sintering Mould) molds possess superior thermal conductivity, ensuring uniform heat distribution during the manufacturing process. This feature eliminates hotspots and minimizes thermal stress, thereby enhancing the overall quality and consistency of the finished products. Manufacturers can now achieve higher precision, reduced waste, and greater control over the manufacturing process, resulting in enhanced customer satisfaction.Environmental-Friendly and Cost-Effective Solution:(Graphite Sintering Mould) also offers environmental advantages by minimizing energy consumption and material waste. The high thermal conductivity of graphite enables faster heating and cooling cycles, reducing power requirements and improving energy efficiency. Additionally, the durability and longevity of (Graphite Sintering Mould) molds enable companies to produce a significantly larger number of items, thus reducing the need for frequent mold replacements.Moreover, the reduced production time and enhanced efficiency provided by (Graphite Sintering Mould) molds translate into significant cost savings for manufacturers. Companies can allocate their resources more strategically, invest in research and development, and explore new market opportunities.Emerging as a Pioneer in Industrial Manufacturing:The company behind the development of (Graphite Sintering Mould) stands at the forefront of innovation in the industrial manufacturing sector. Through extensive research and development, the company has successfully harnessed the unique properties of graphite and perfected the technology to produce reliable, high-performance molds.The exceptional quality of molds generated using (Graphite Sintering Mould) has garnered attention from major industries worldwide. Their commitment to sustainable practices alongside their relentless pursuit of excellence positions the company as a leading pioneer in the manufacturing field.Looking Forward:The introduction of (Graphite Sintering Mould) marks a significant milestone in the evolution of industrial manufacturing. With its ability to enhance production efficiency, reduce costs, and deliver superior quality products, this technology holds vast potential for various sectors. Manufacturers across the globe are eagerly adopting this groundbreaking method, propelling the industry toward a more sustainable and efficient future.As researchers continue to refine and expand the capabilities of (Graphite Sintering Mould), we can anticipate further advancements that will revolutionize the way products are manufactured. With improved mold designs, expanded applications, and increased efficiency, the possibilities for innovation with this game-changing technology are limitless.
High-quality Graphite Crucibles Ideal for Melting Tin
Title: Graphite Crucible for Melting: A Reliable Choice for Industrial ApplicationsIntroduction:In various industrial sectors, the process of melting metals and other high-temperature applications plays a significant role. To ensure the success of these operations, the selection of high-quality equipment is essential. Graphite crucibles, popularly used for melting purposes, have gained immense popularity due to their exceptional properties and reliability. In this blog post, we will delve into the features, benefits, and applications of graphite crucibles for melting various materials in industrial settings.1. Understanding Graphite Crucibles:Graphite crucibles are specialized containers designed for holding and melting metals and other materials at extremely high temperatures. These crucibles are made from high-purity graphite, which exhibits remarkable thermal conductivity, corrosion resistance, and mechanical strength. The unique properties of graphite make it an ideal material for melting purposes.2. Key Features of Graphite Crucibles:2.1 High Thermal Conductivity:Graphite crucibles offer excellent heat transfer capabilities. Their high thermal conductivity ensures efficient and uniform melting of metals, eliminating the formation of hotspots, and providing consistent results.2.2 Corrosion Resistance:The chemical inertness of graphite makes crucibles highly resistant to corrosive agents. They can withstand aggressive molten materials, preventing contamination and maintaining the purity of the melted substance.2.3 Mechanical Strength:Graphite crucibles possess exceptional mechanical strength, allowing them to endure high temperatures and withstand thermal shock. This durability ensures longevity and enables multiple reuse cycles, making them a cost-effective choice.2.4 Excellent Insulation:Graphite crucibles exhibit excellent insulation properties, minimizing heat loss during melting operations. This feature increases energy efficiency and reduces operating costs.3. Benefits of Using Graphite Crucibles for Melting:3.1 Versatility:Graphite crucibles are compatible with a wide range of metals and materials. From precious metals like gold and silver to high-temperature alloys, graphite crucibles offer versatility for diverse melting requirements.3.2 Clean and Contamination-Free Melting:The non-reactive nature of graphite minimizes unwanted reactions, ensuring clean and pure melting processes. This aspect is crucial in industries like jewelry-making, where precise composition and flawless quality are imperative.3.3 Cost-Effective Solution:Graphite crucibles are highly durable and can withstand repeated use, making them a cost-effective solution in the long run. Additionally, their exceptional thermal conductivity reduces melting time and energy consumption, further contributing to cost savings.3.4 Easy Handling and Maintenance:Graphite crucibles are lightweight and easy to handle, simplifying the overall melting process and reducing the operational burden. Basic maintenance practices like periodic cleaning ensure the longevity of these crucibles.4. Applications of Graphite Crucibles:4.1 Metallurgy and Foundry:Graphite crucibles find extensive usage in the metallurgical and foundry industries for melting and casting various metals such as iron, steel, aluminum, and copper. Their thermal resistance and durability make them an ideal choice in these demanding operations.4.2 Jewelry-Making:The jewelry industry relies heavily on graphite crucibles for melting precious metals, enabling the creation of intricate and high-quality jewelry designs. The purity maintained during melting ensures flawless end products.4.3 Laboratory Applications:Graphite crucibles are widely employed in laboratory settings for experiments requiring high temperatures and controlled melting processes. Their reliability and consistency make them a trusted choice for scientific research and analysis.Conclusion:Graphite crucibles are a reliable and efficient solution for melting operations in diverse industries. Their exceptional properties, including high thermal conductivity, corrosion resistance, and mechanical strength, make them ideal for applications ranging from foundries to jewelry-making and laboratory experiments. With their cost-effectiveness and versatility, graphite crucibles continue to be the go-to choice for achieving efficient and contamination-free melting processes.
Leading Manufacturers and Suppliers of Graphite Electrodes in China
Graphite Rods for Electrodes: A Complete GuideGraphite rods for electrodes are an essential component in the manufacture of electric arc furnaces (EAFs) and other high-temperature applications. Their high thermal and electrical conductivity, low coefficient of thermal expansion, and chemical inertness make them an ideal material for the creation of electrodes. In this article, we will provide a complete guide on graphite rods for electrodes, including their manufacturing process, properties, and applications.Graphite Rods for Electrodes: Manufacturing ProcessGraphite rods for electrodes are typically made from petroleum coke, which is a byproduct of oil refining. First, the petroleum coke is crushed and pulverized into a fine powder. Then, the powder is mixed with a binder, such as coal tar pitch, and extruded into the desired shape and size. After extrusion, the rods are baked at high temperatures, typically above 2000°C, to convert the binder into a rigid, carbonaceous material.Graphite Rods for Electrodes: PropertiesGraphite rods for electrodes have a number of unique properties that make them well-suited for high-temperature applications. First and foremost, graphite is an excellent conductor of both heat and electricity. This means that it can quickly transfer heat and electrical current to the material being melted or heated.In addition to its conductivity, graphite also has a low coefficient of thermal expansion, which means that it does not expand or shrink significantly when subjected to changes in temperature. This property is particularly important in high-temperature applications, as changes in size can cause the material to crack or break.Graphite also has a high melting point, typically over 3000°C, making it an ideal material for use in EAFs and other high-temperature industrial processes. Lastly, graphite is highly chemically inert, which means it has excellent resistance to corrosion and chemical attack.Graphite Rods for Electrodes: ApplicationsGraphite rods for electrodes are widely used in a variety of applications, the most common of which is the production of steel in EAFs. In this process, the graphite electrodes are used to create an electric arc that heats up and melts the scrap metal being fed into the furnace.In addition to steel production, graphite electrodes are used in a number of other industrial processes, including the production of aluminum, copper, and other metals. They are also used in the production of chemicals, such as chlorine and sodium hydroxide, as well as in the production of graphite crucibles for use in high-temperature applications.Graphite Rods for Electrodes: ConclusionIn conclusion, graphite rods for electrodes are an essential component in a number of high-temperature industrial processes. Their unique properties, including high thermal and electrical conductivity, low coefficient of thermal expansion, and chemical inertness, make them well-suited for use in EAFs and other high-temperature applications.If you are in need of high-quality graphite rods for electrodes, look no further than our China-based graphite electrode factory. With years of experience and state-of-the-art equipment, we can provide you with the graphite rods you need to keep your operations running smoothly and efficiently. Contact us today to learn more about our products and services.
Innovative Graphite Boat for Sintering: Ideal for Tableware and Housewares Manufacturing
Title: Xmyangquan.com Introduces Innovative Graphite Sintering Boats for Enhanced Tableware ProductionIntroduction:Xmyangquan.com takes pride in announcing the latest addition to its product line - the graphite sintering boat. This innovative solution is set to revolutionize the tableware industry by providing manufacturers with a reliable and efficient method for sintering ceramics, porcelain, and other materials seamlessly. With its superior qualities and advanced manufacturing techniques, Xmyangquan.com's graphite sintering boats are a game-changer in the pursuit of high-quality tableware production.Setting New Industry Standards:Xmyangquan.com's graphite sintering boats are designed to withstand extremely high temperatures, making them ideal for use in the production of tableware. By utilizing state-of-the-art technology, these sintering boats offer exceptional heat resistance, low thermal expansion, and excellent thermal conductivity. This unique combination ensures an even and efficient distribution of heat, resulting in enhanced and uniform product quality.Superior Material Properties:The secret behind the exceptional performance of Xmyangquan.com's graphite sintering boats lies in the extraordinary properties of graphite. Known for its superior strength-to-weight ratio and excellent thermal conductivity, graphite helps optimize the sintering process. Additionally, its chemical stability minimizes contamination risks, ensuring the purity and integrity of the final products.Innovative Design and Manufacturing Excellence:Xmyangquan.com's graphite sintering boats are crafted with the utmost precision and attention to detail. The company employs advanced manufacturing techniques, such as isostatic pressing and high-temperature treatment, to create sintering boats with consistent dimensions and exceptional durability. The strong and robust structure of these boats guarantees their longevity and enables repetitive use, further maximizing their value for manufacturers.Sustainable and Eco-Friendly Solution:As an environmentally conscious company, Xmyangquan.com is committed to producing sustainable products. Graphite sintering boats contribute to this mission as they are reusable and have a minimal environmental footprint. By investing in these boats, manufacturers can reduce waste and energy consumption, thus contributing to a greener future for the tableware industry.Versatile Applications:The graphite sintering boats offered by Xmyangquan.com are not limited to a specific range of tableware production. Their versatility allows manufacturers to sinter a multitude of materials, including ceramics, porcelain, glass, and various metal alloys. Their non-reactive properties make them suitable for applications with different chemical compositions, further expanding their usefulness.Competitive Advantage:By incorporating Xmyangquan.com's graphite sintering boats into their production processes, tableware manufacturers gain a significant competitive advantage. These boats facilitate higher production volumes, reduce the risk of defects, and produce consistently high-quality products. Manufacturers can streamline their operations, leading to increased efficiency and customer satisfaction.Conclusion:Xmyangquan.com's introduction of the graphite sintering boat reshapes the tableware industry by offering a reliable and efficient sintering solution. With superior material properties, innovative design, and a focus on sustainability, this new product line sets new industry standards. Manufacturers can now benefit from increased productivity, improved quality control, and a reduced environmental impact. Xmyangquan.com's commitment to excellence ensures that the tableware industry will experience significant advancements in the coming years.
Exothermic Welding Moulds for Precise Welding - Graphite Material Available
Exothermic Welding Graphite Moulds: The Perfect Solution for WeldingExothermic welding, also known as exothermic bonding, thermit welding, or thermite welding, is a method of welding that uses heat generated by a chemical reaction to join two metals. This method of welding is widely used in various industries and applications, including construction and electrical work.One essential component of exothermic welding is the graphite mould used to contain and shape the weld. These moulds are essential to ensure a proper bond between the two metals and are available in different sizes and shapes to meet various welding needs.China is a leading manufacturer and supplier of exothermic welding graphite moulds. Chinese manufacturers offer high-quality moulds that meet international standards at affordable prices, making it an attractive option for businesses worldwide.CAD Exothermic Welding MouldsCAD exothermic welding moulds are a popular option among businesses looking for precise and efficient exothermic welding. These moulds are designed using computer-aided design (CAD) technology, enabling manufacturers to produce moulds with exact specifications.The use of CAD technology ensures that these moulds have a consistent and accurate shape, which results in a uniform weld. These moulds are also highly durable and can withstand high temperatures, ensuring they can be used repeatedly.Graphite Welding MouldsGraphite is a popular material used to manufacture exothermic welding moulds due to its ability to withstand high temperatures, which is essential in exothermic welding. Graphite moulds are also easy to handle, lightweight, and offer a high level of flexibility when it comes to shaping and designing them.Graphite welding moulds are highly durable, making them an excellent choice for businesses that rely on welding frequently. Graphite moulds are also easy to maintain, which makes them a cost-efficient option for businesses.Exothermic Weld MaterialThe exothermic weld material used in exothermic welding is a mixture of metal powder and a metal oxide, along with other compounds that help initiate the chemical reaction that creates the heat required for welding.The exothermic welding material is available in different sizes, depending on the size of the welding job, and can weld all types of conductors, including copper, brass, aluminum, steel, and others.ConclusionExothermic welding is an essential method of welding used in various industries worldwide. Graphite moulds and the exothermic weld material used in exothermic welding are two critical components that ensure the welding process works correctly.China is one of the leading manufacturers and suppliers of exothermic welding graphite moulds, which are known for their high quality, durability, and affordability. The use of CAD technology has made it possible for manufacturers to produce highly accurate and efficient moulds.Businesses that rely on exothermic welding should consider using China's graphite moulds and exothermic weld material to achieve the best welding results.
Small Electric Foundry for Bronze Casting: Tips and Techniques for Successful Results
Electric Foundry for Small Bronze Casting – Crucible for Melting BronzeBronze casting has been around for thousands of years. It is an ancient method of creating beautiful objects of art. Today, modern technology has made it easier for people to attempt bronze casting on their own. This is where a small electric foundry comes in handy. In this article, we will discuss how to make a small foundry for melting tin bronze.First, let's talk about the materials we will need. The following items are essential for building a small foundry:1. Soft fire bricks – These bricks are used to build the walls of the foundry. They are designed to withstand high temperatures.2. Insulator – This is a high-temperature insulation material that is used to line the inside of the foundry. It keeps the heat inside the foundry and prevents it from escaping.3. Nichrome coil – This is a heating element that is used to provide the heat needed to melt the tin bronze.4. Crucible – This is a container used to melt the bronze. It must be made of a material that can withstand high temperatures and is resistant to corrosion.Now that we have the materials, let's get started on building the foundry. The first step is to build a frame with the soft fire bricks. The size of the frame will depend on the size of the crucible. The frame should be built to support the crucible and the insulator.Next, place the insulator inside the frame. The insulator should be cut to size and placed inside the frame. It should be wrapped around the sides and the bottom of the frame. The insulator is what will keep the heat inside the foundry.After the insulator is in place, wrap the nichrome coil around the outside of the insulator. The coil should be wrapped tightly and evenly around the entire foundry. It should be wired to a 240V 10amp socket. The coil is what will provide the heat necessary to melt the tin bronze.Once the coil is in place, it's time to add the crucible. The crucible should be placed inside the foundry and centered on the coil. It should be large enough to hold the amount of bronze you plan to melt. The crucible should be made of a material that can withstand high temperatures, such as graphite or ceramic.Finally, turn on the power to the coil. The heat should be gradually increased until the bronze is fully melted. Once the bronze is melted, it's ready for casting.ConclusionBuilding a small foundry for melting tin bronze is not a difficult task. With the right materials, it can be done easily at home. By using a soft fire brick frame, high-temperature insulation, a nichrome coil, and a crucible, you can create your own electric foundry. This will allow you to create beautiful bronze objects of art in the comfort of your own home. So, get started today and let your creativity flow!
Top-grade Machined Graphite Blocks: A Cost-effective and Durable Solution for High-performance Applications
Machined Graphite Block : A Revolutionary Product for Various IndustriesIn today's rapidly developing world, innovations and advancements have changed the face of various industries. One such remarkable and revolutionary product that has been introduced in recent years is Machined Graphite Block. Machined Graphite Blocks are widely used in various industrial applications because of their superior properties, such as high resistance to heat, chemical reaction, and oxidation. Machined Graphite Blocks have proved to be an essential material for manufacturing high-performance products. Its extensive range of applications includes nuclear reactors, aerospace, semiconductors, medical equipment, and many others.Company IntroductionThe company is a leading manufacturer and supplier of high-quality Machined Graphite Blocks. The company has been established for many years and has gained a strong reputation for producing high-performance Machined Graphite Blocks. Their team of professionals, engineers, and technicians possess comprehensive knowledge and experience in manufacturing graphite materials. They are dedicated to providing top-quality products that meet the needs of their customers.Currently, the main focus of the company is to provide customers with top-quality Machined Graphite Blocks that meet and exceed their expectations. The company has a state-of-the-art facility that is equipped with the latest technology and machinery to manufacture high-quality Machined Graphite Blocks. They have a team of skilled professionals that ensure that they are producing the highest quality products possible. The company also has a dedicated team of customer service representatives, who are always ready to help their customers with any queries and concerns they might have.Application of Machined Graphite Block:Machined Graphite Blocks are widely used in various industries because of their superior properties. Here are some of the applications for Machined Graphite Blocks:1. Chemical Industries: Machined Graphite Blocks are widely used in chemical industries because of their high resistance to chemical reactions. They are used to manufacture chemical equipment that is used to store, transfer, and process chemicals.2. Aerospace and Defense: Machined Graphite Blocks are used in the aerospace and defense industry to manufacture rocket nozzles. Graphite is an excellent conductor of heat, and it is a lightweight material, making it an ideal material choice for manufacturing rocket nozzles.3. Semiconductor Industry: Machined Graphite Blocks are used in the semiconductor industry to manufacture various equipment and components. This is because graphite has a high resistance to heat, making it an ideal material for manufacturing equipment that can operate at high temperatures.4. Nuclear Reactors: Machined Graphite Blocks are widely used in the nuclear industry because of their high thermal conductivity and electrical resistance. They are also used to manufacture the core of nuclear reactors.Benefits of Machined Graphite Blocks:1. High Resistance to Heat: Machined Graphite Blocks are known for their high resistance to heat. They can withstand high temperatures up to 3600°F or more, making them an ideal material for manufacturing high-temperature equipment.2. Chemical Resistance: Machined Graphite Blocks have a high resistance to chemical reactions, making them ideal for manufacturing chemical equipment.3. Non-toxic: Machined Graphite Blocks are non-toxic, making them an ideal material for manufacturing medical equipment.4. Low Thermal Expansion: Machined Graphite Blocks have a low thermal expansion rate, making them ideal for manufacturing equipment that requires stability at high temperatures.Conclusion:Machined Graphite Blocks are an excellent material for manufacturing various industrial equipment. Their superior properties, such as high resistance to heat, chemical reaction, and oxidation, make them an ideal material choice for many industries. The company is dedicated to providing top-quality Machined Graphite Blocks to meet and exceed the needs of their customers. The company's commitment to quality and customer satisfaction is reflected in their state-of-the-art facility, experienced team of professionals, and exceptional customer service. Whether you are in the aerospace, chemical, semiconductor, or medical industry, Machined Graphite Blocks can help you achieve a superior-level product that will outperform other materials.